- Joined
- Jul 16, 2007
- Messages
- 2,987
- Reaction score
- 1,055
The block was removed from the vise and the burrs cleaned up and then flipped to start on the other side. After setting my height to clear my longest tool I repicked up my centers and moved to the distributor hole. I successively plunged end mills into the hole until I got to .95 diameter. (1.00 sharpened many times) I then went back with a .375 end mill and walked around the inside cavity to cut the bottom surface flat and to depth. Finally I put the new 1.00 end mill in and opened up the hole. The little bit of bottom relief on the end mill won't bother anything for .025 per side. The next step was to drill out the extra hole for the timing cover.
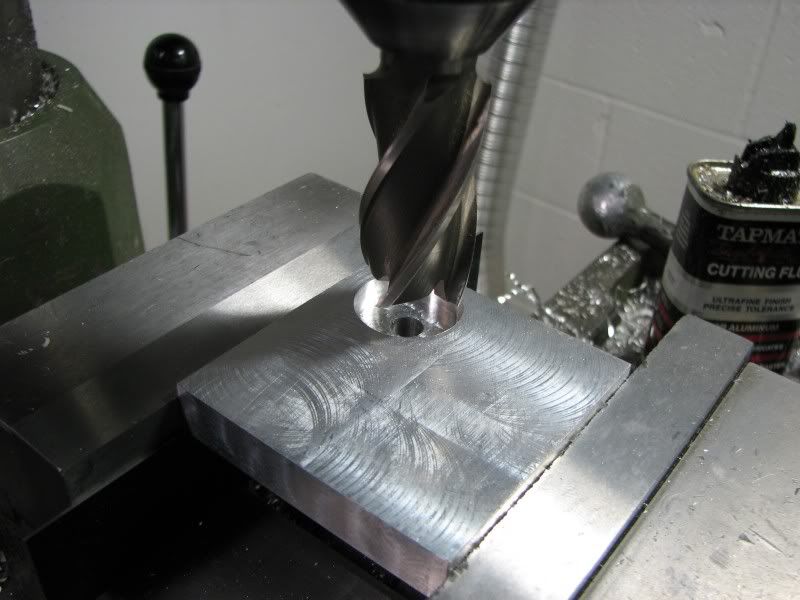
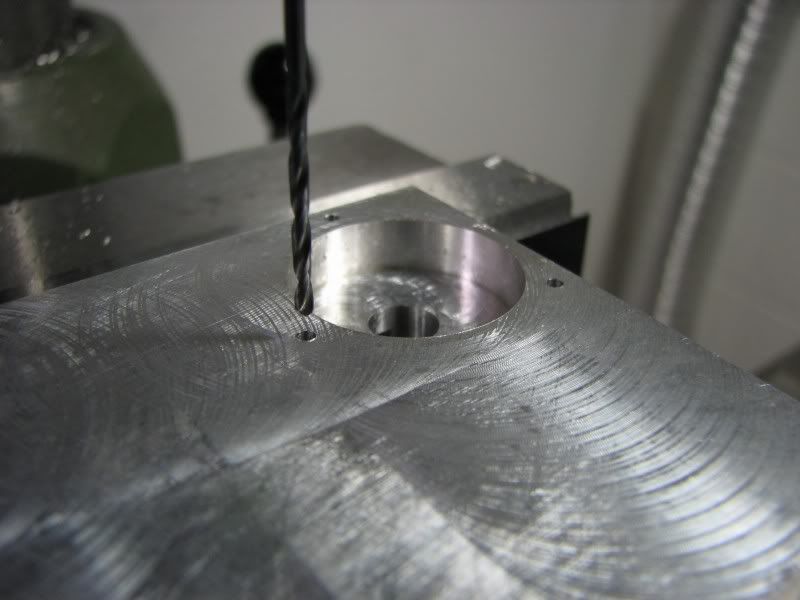