- Joined
- Jul 16, 2007
- Messages
- 2,987
- Reaction score
- 1,055
The last two pictures show the mounting holes tapped, everything cleaned up and one shot with a penny for comparison of size. Tomorrow the ribbing and the most time consuming part will be finished.
gbritnell
gbritnell
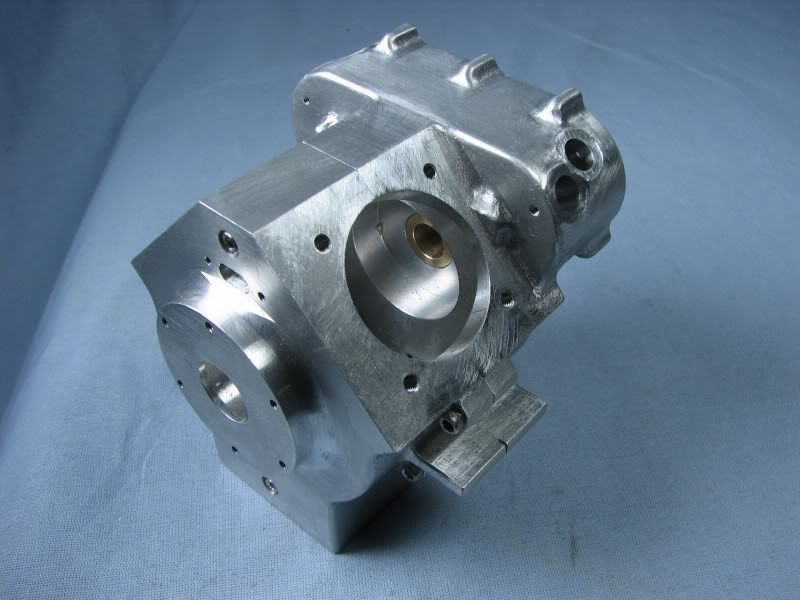
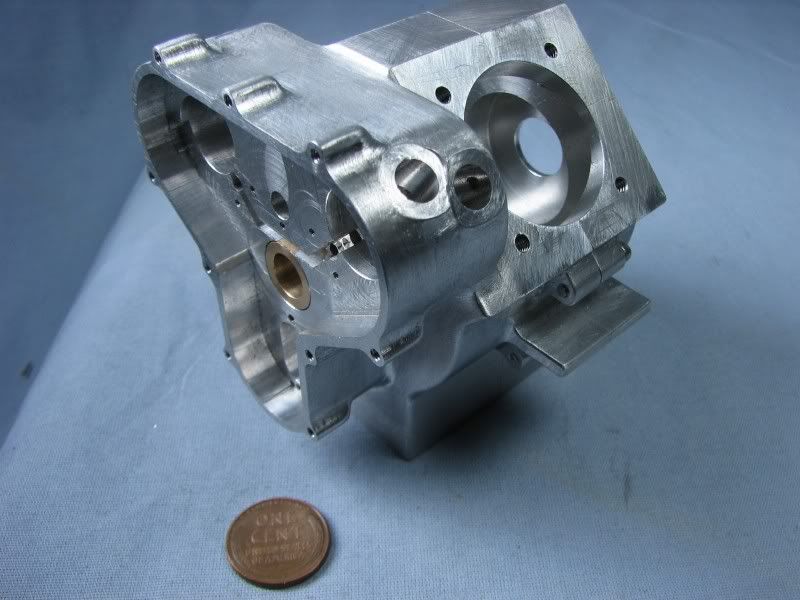