Tin Falcon
Well-Known Member
- Joined
- Jul 9, 2007
- Messages
- 7,207
- Reaction score
- 788
and a couple shots of my piston con rods flat metal with holes and tapered with a file.
Tin
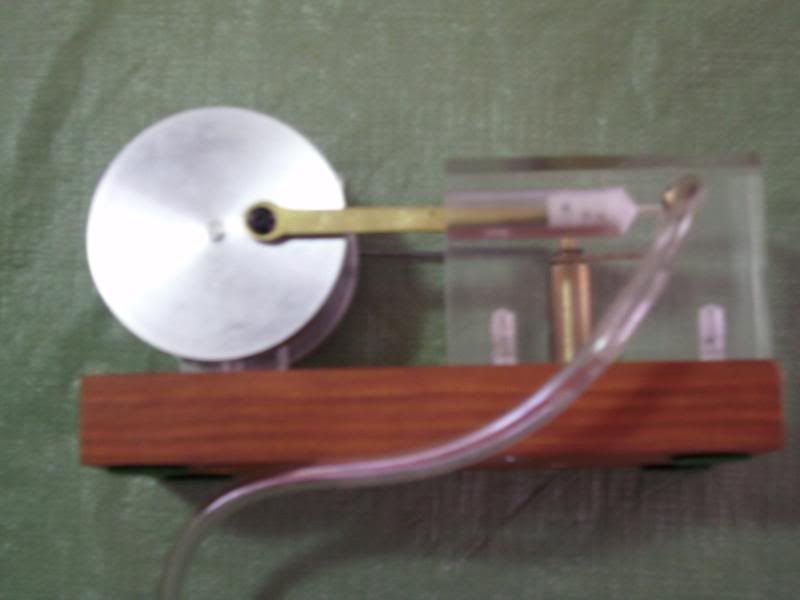
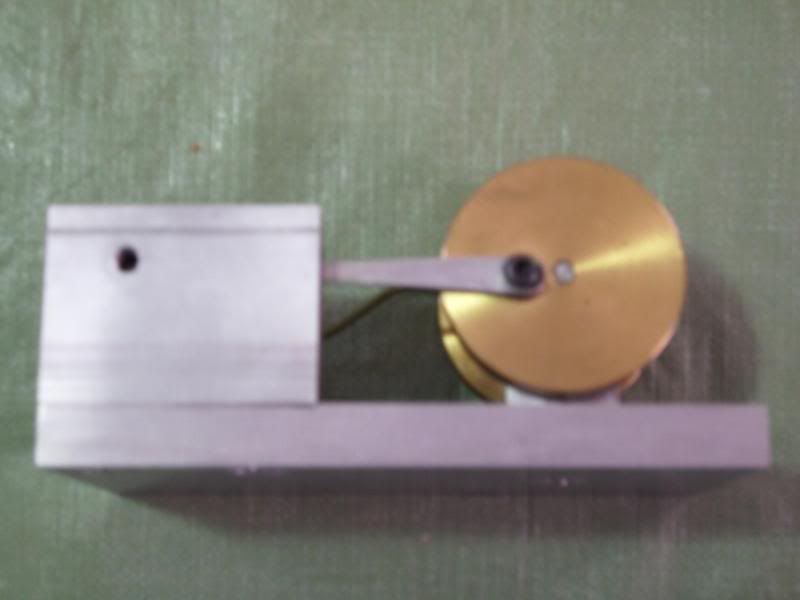
Tin