Well, thats enough for me for one Saturday. I'm tuckered out!! For all who worried about my setup---Each bearing stand was bolted to the aluminum plate with 2 bolts. The aluminum plate was clamped to the angle with two c-clamps, and the angle was bolted to the mill table with two 10MM bolts and T-nuts. Nothing moved, nor tried to move. Thank you for your concern. You are probably right about something under the cantilevered bearing stands being a good idea, and if they had been steel I definitly would have had additional bracing.
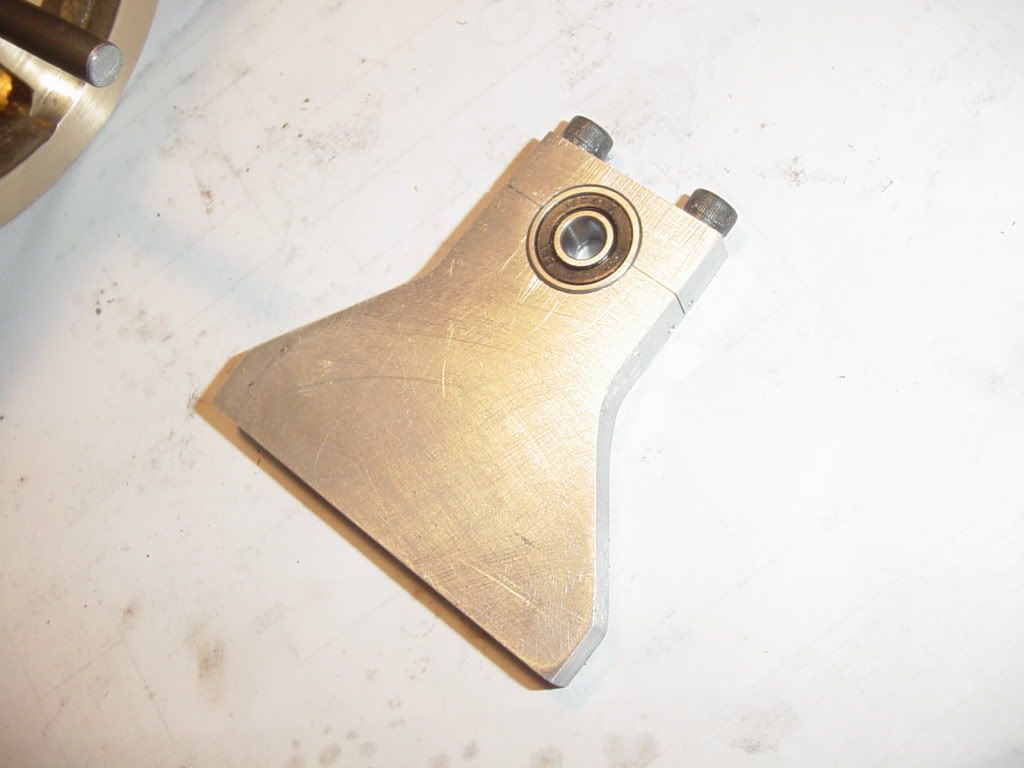
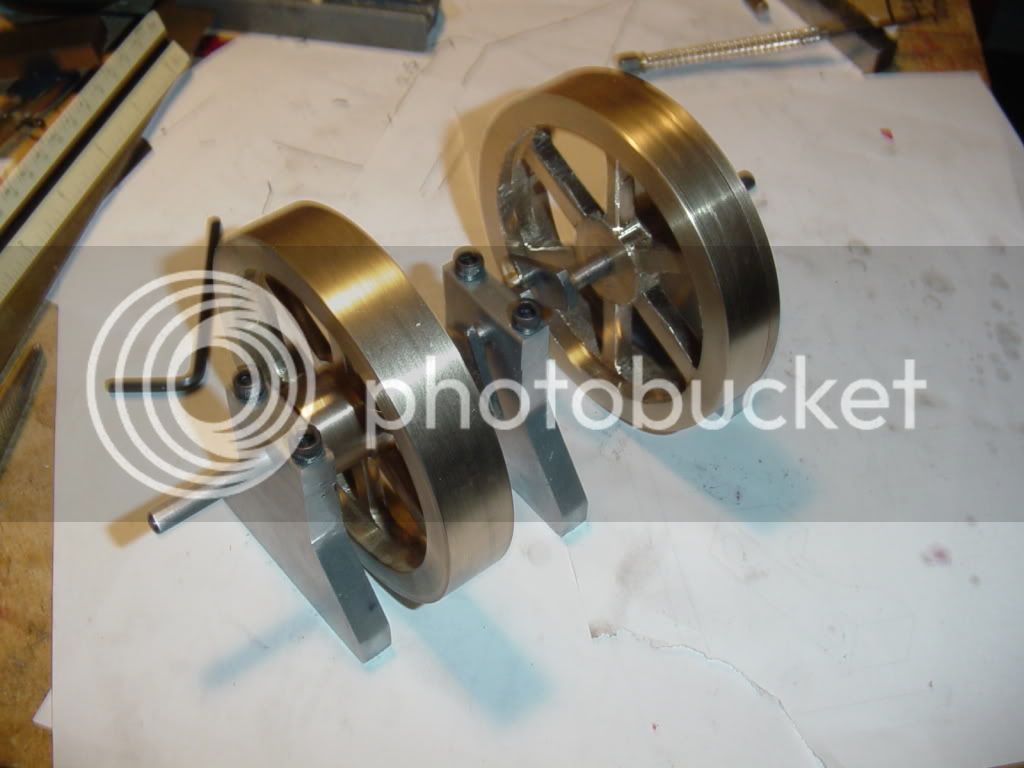
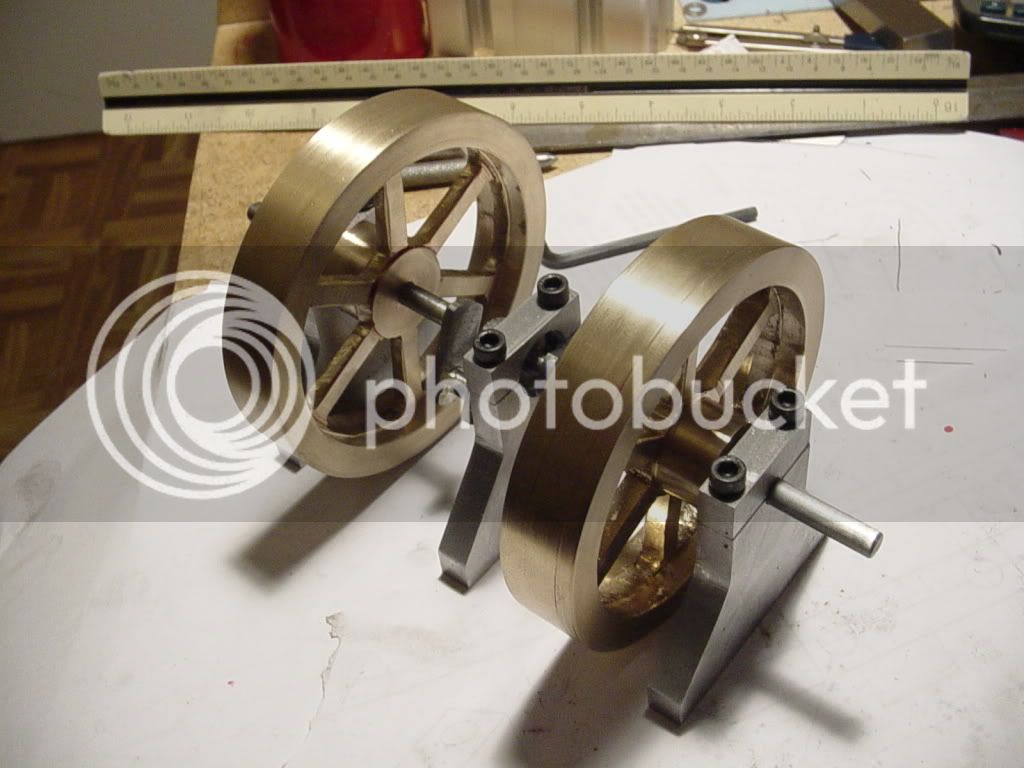