Here we have the 4 peices of aluminum stacked and fastened with "crazy glue" , and the top peice coated with layout dye, and layed out.
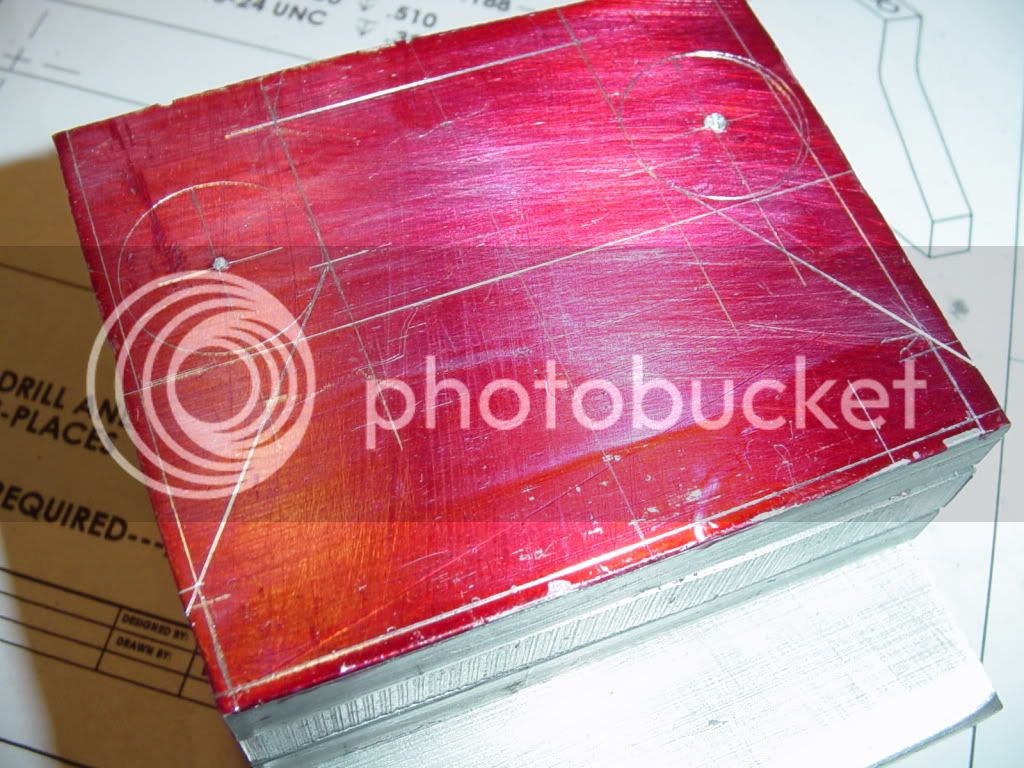
I don't have a flood coolant option on my mill, but thats okay. I have discovered over the course of my 62 years on this planet, that adhesives, in general do not work for me. For one thing, I never have the time to wait for them to set up. If I am going to do something, then I want to do it RIGHT NOW!!! None of this "glue now and come back in 4 hours stuff". Other than Elmers wood glue, (on wood) and 2 part 5 minute epoxy on anything that isn't wood, I stay away from adhesives as much as I can. This latest crazy glue fiasco only confirms what I thought already--"If its machinery, use a metal fastener".steamboatmodel said:Hi Brian,
If you are cutting dry the material will heat up and cause the crazy glue to release. Any time I held material together with crazy glue I used flood coolant, and never had any problems.
Brian Rupnow said:And here is the second soldering, set up in the jig. If it looks messy and ugly on your monitor, thats because it is messy and ugly. However, it will be going for beuaty treatment shortly.
Brian Rupnow said:the mill wants to levitate if I run it at more than 675 RPM .
Enter your email address to join: