It doesn't look like much, and its not a great photograph, but two little parts were made and fitted this afternoon. The cam shaft, which passes thru the large gear and anchors in the engine sideplate, and the spacer that sets the distance from the sideplate to the side of the gear. I have to approach building these small engines the same way you would eat an elephant----one small bite at a time. If you consider ALL of the pieces, you would throw up your hands and find a different hobby. As a side note, when I built the gears and drilled a test block with the correct hole centers for a pair of dummy shafts, the gears meshed perfectly, as can be seen in the video clip at the beginning of this thread. Once I got them installed on the engine however, they wanted to bind very badly. After a lot of head scratching and measuring, I determined that "somehow" I had drilled the hole in the engine sideplate .020" too close to the crankshaft gear. Since the camshaft is locked in the sideplate with a set screw, I was able to "stretch" the hole .020" farther away from the crankshaft, and the gears mesh fine now.
Brian
Brian
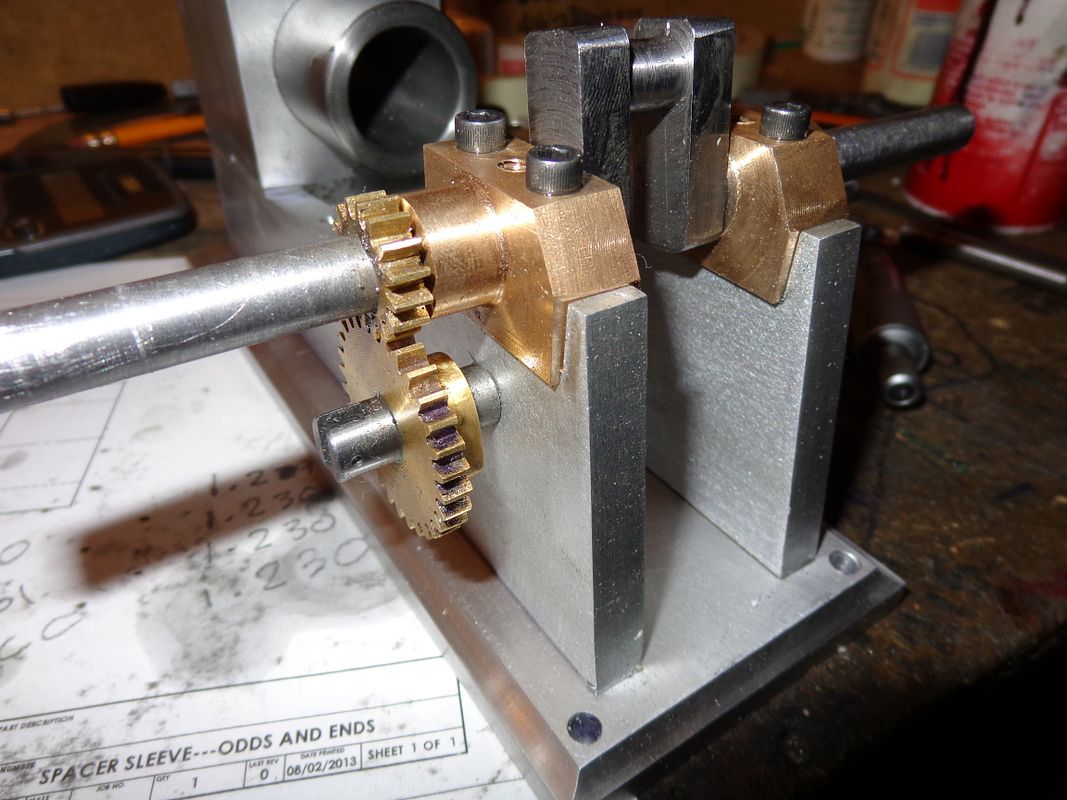