- Joined
- Jan 17, 2009
- Messages
- 887
- Reaction score
- 81
Thanks Arnold
Well yesterday was yet another case of "best laid skeams of mice and men all gang away". I could see the whole day in front of me in the shop, but I'd forgotten about the Boss, we'd booked seats for a Don McClane (of American Pie Fame) In Liverpool for the evening, but the Boss thought it would be a good idea to go early and have a wander around the shops visit the Tate modern art Gallery at the Albert Docks etc etc so strike one afternoon in the shop. Enjoyed the visit and concert though, and came across one interesting fact you guys across the pond will be interested in, theirs a very nice bronze statue at Albert Dock commemorating emigration donated to the city by the Mormon Church, it's plaque states that over 9 Million people emigrated from Europe to North America through the port of Liverpool:- just what % of the population are decended from those emigrants now :scratch: the mind boggles.
Back on topic:-
The wings of the fire box rapper need to be extended to do this I will have to make a joint, this can be a simple lap joint but this will take up some water space or a joggled joint, I'm going to use a joggle joint. First thing make a joggling tool, now this isn't going to be a fancy tool just dog rough and functional.
Mill a bit of flat steel (garage door thanks Ralph) flat and put a groove up it 1/4" + plate thickness + a bit for luck.
Then with the plate well annealed and a 1/4" square bar squeeze the plate into the grooves.
This will bend it out a bit wack it back square with a bit of ally bar and a hammer.
And thats the joggled joint formed.
Cheers
Stew
Well yesterday was yet another case of "best laid skeams of mice and men all gang away". I could see the whole day in front of me in the shop, but I'd forgotten about the Boss, we'd booked seats for a Don McClane (of American Pie Fame) In Liverpool for the evening, but the Boss thought it would be a good idea to go early and have a wander around the shops visit the Tate modern art Gallery at the Albert Docks etc etc so strike one afternoon in the shop. Enjoyed the visit and concert though, and came across one interesting fact you guys across the pond will be interested in, theirs a very nice bronze statue at Albert Dock commemorating emigration donated to the city by the Mormon Church, it's plaque states that over 9 Million people emigrated from Europe to North America through the port of Liverpool:- just what % of the population are decended from those emigrants now :scratch: the mind boggles.
Back on topic:-
The wings of the fire box rapper need to be extended to do this I will have to make a joint, this can be a simple lap joint but this will take up some water space or a joggled joint, I'm going to use a joggle joint. First thing make a joggling tool, now this isn't going to be a fancy tool just dog rough and functional.
Mill a bit of flat steel (garage door thanks Ralph) flat and put a groove up it 1/4" + plate thickness + a bit for luck.

Then with the plate well annealed and a 1/4" square bar squeeze the plate into the grooves.
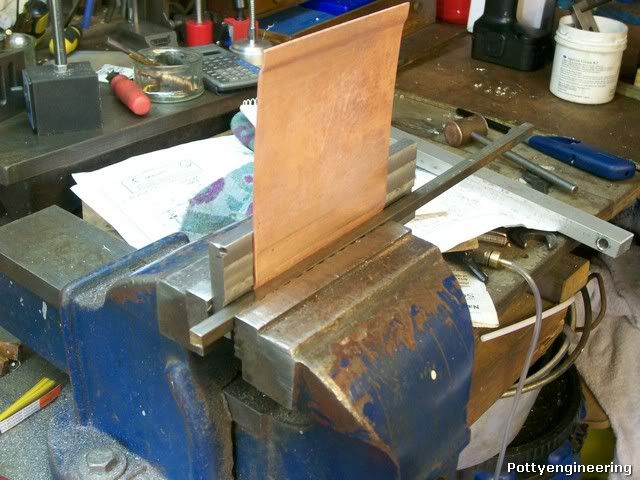
This will bend it out a bit wack it back square with a bit of ally bar and a hammer.
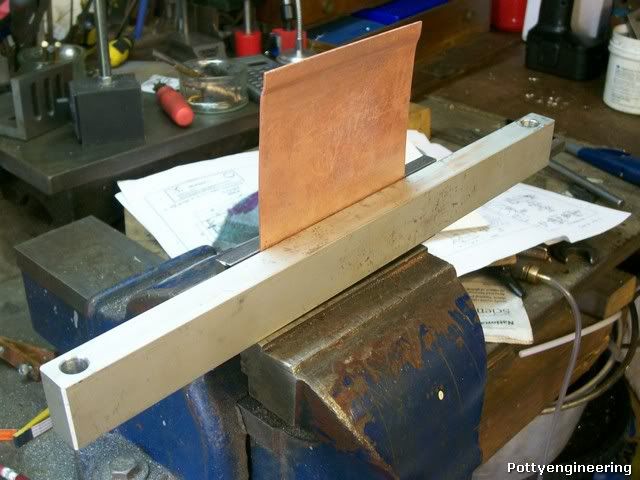
And thats the joggled joint formed.
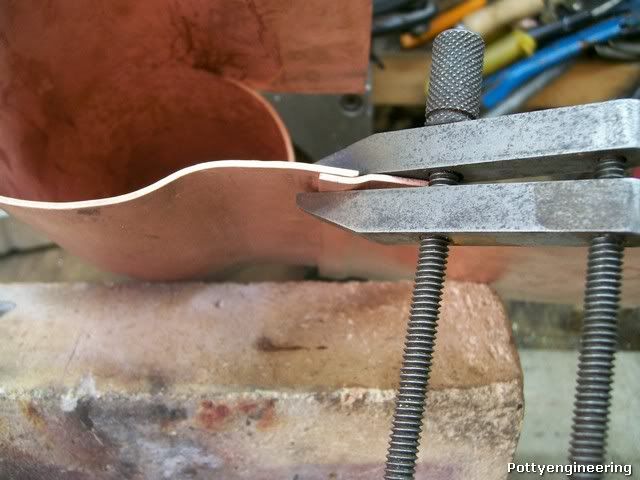
Cheers
Stew