- Joined
- Jun 4, 2008
- Messages
- 3,285
- Reaction score
- 630
Starting to put the floats together. First need to bend the brackets. I use the bench vise and line up the scribed line with the top of the jaw, and hit it with a deadblow hammer.
Next, use the die block to start the drive screws through the bracket.
With the ends of the screws exposed they can be aligned with the float and started using a small hammer.
Drive the screw heads flush with the bracket using the vise and die block.
Clamp the bracket in the mill vise and mill off the protruding ends of the screws. I used a 1/2" ball nose mill for this.
Test with paint. Using tractor implement spray paint; result looks good thus far.
Should finish up the others and ready for paint next shop session. Still need to make two more brackets.
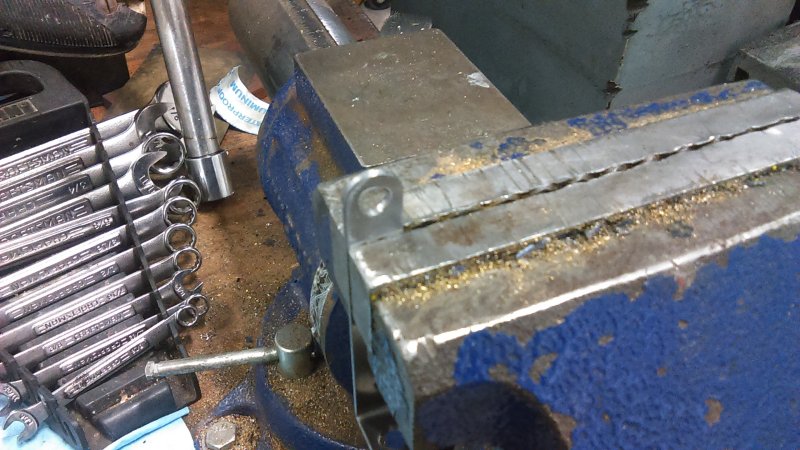
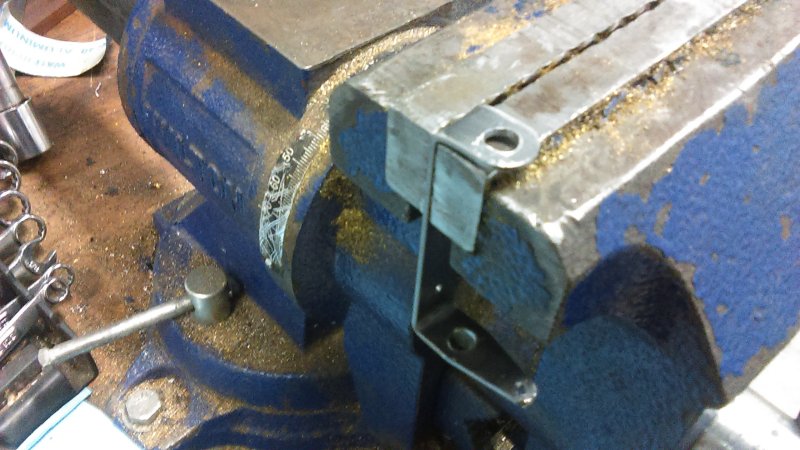
Next, use the die block to start the drive screws through the bracket.
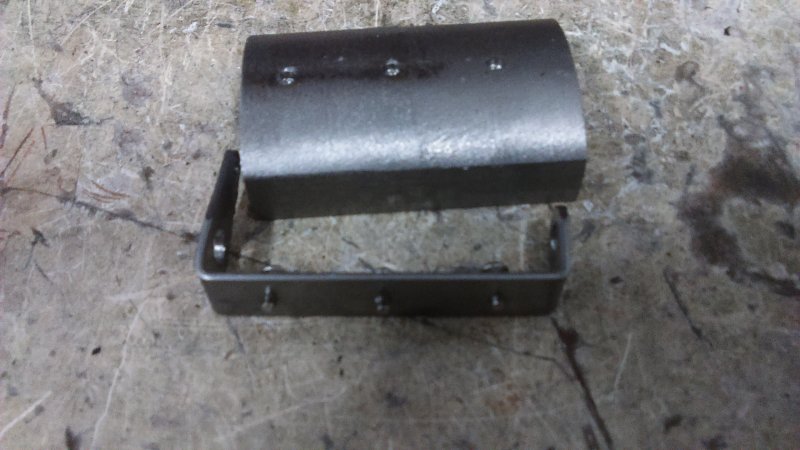
With the ends of the screws exposed they can be aligned with the float and started using a small hammer.
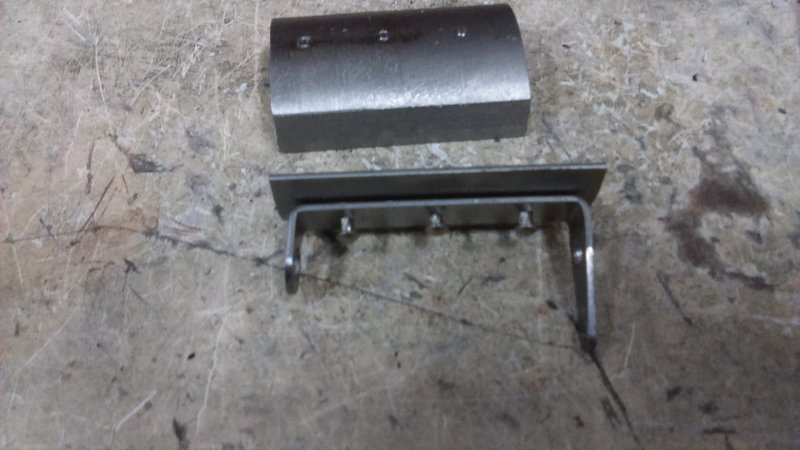
Drive the screw heads flush with the bracket using the vise and die block.
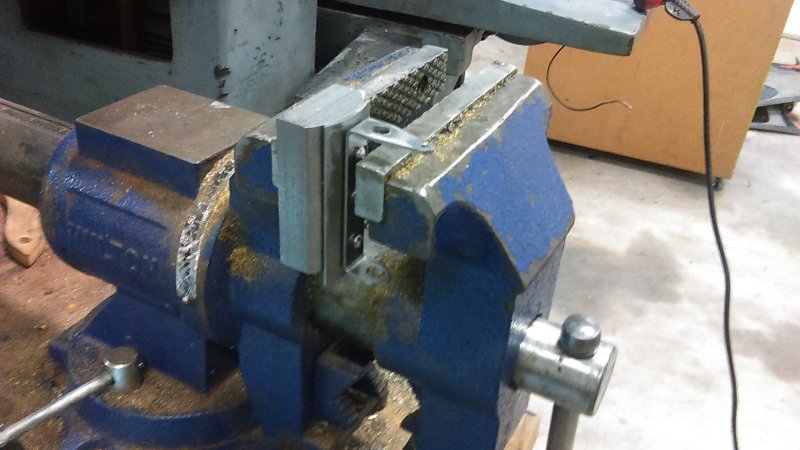
Clamp the bracket in the mill vise and mill off the protruding ends of the screws. I used a 1/2" ball nose mill for this.
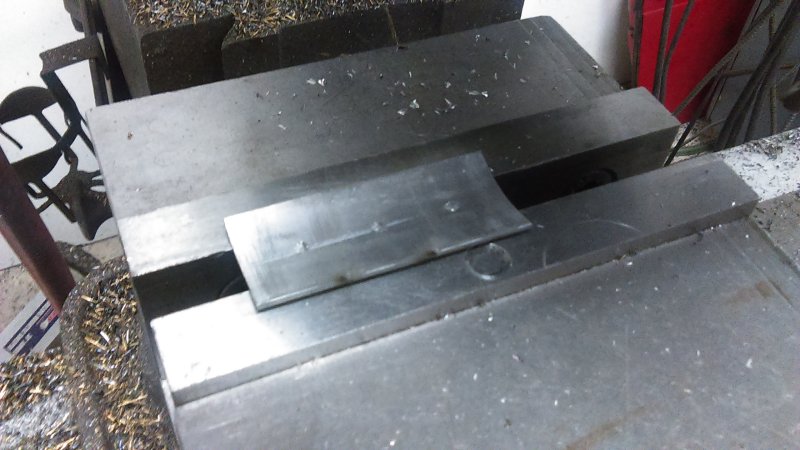
Test with paint. Using tractor implement spray paint; result looks good thus far.
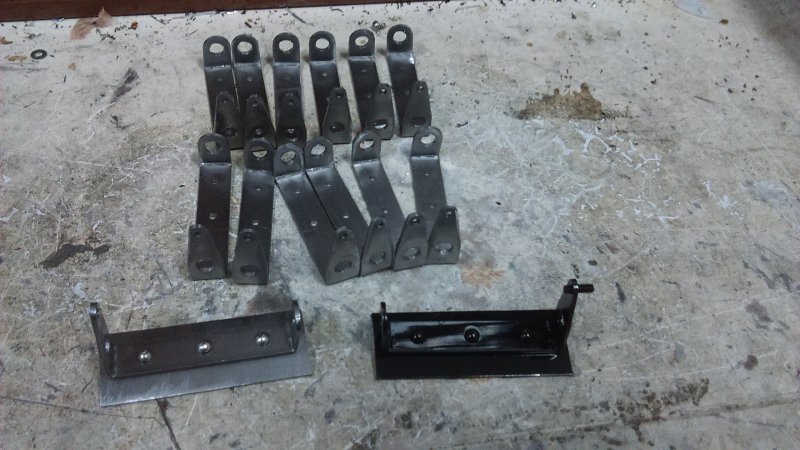
Should finish up the others and ready for paint next shop session. Still need to make two more brackets.