- Joined
- Jun 4, 2008
- Messages
- 3,285
- Reaction score
- 630
Some more halting progress. Made the first part of the 2-piece throttle reach rod from 1/4" 303 stainless, then a brass pin to connect it to the valve spindle crank. The assembly is retained by a small stainless latch pin as show in the pic. The through hole in the brass was drilled with a #56 drill, the smallest hole I can ever remember drilling.
While not visible in the photo, each end of the rod was milled flat half way through the diameter to provide a better mating surface.
The second part of the rod will be identical to the first, except its length will be determined by the size and position of the turret when made.
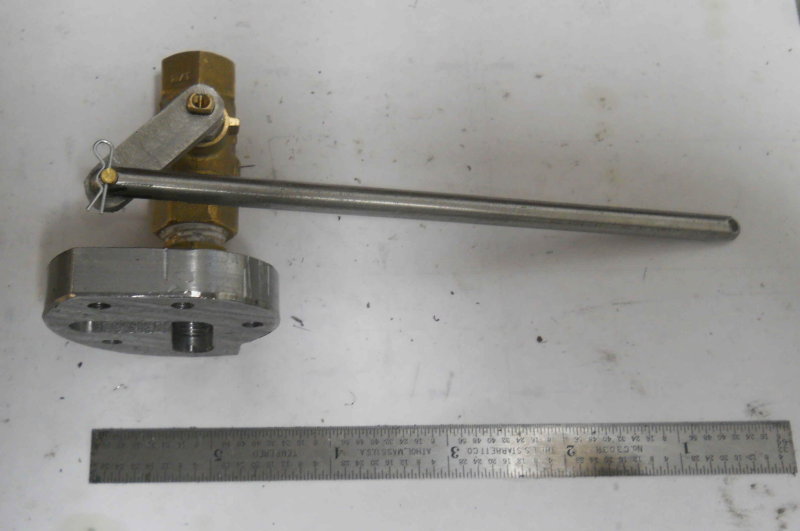
While not visible in the photo, each end of the rod was milled flat half way through the diameter to provide a better mating surface.
The second part of the rod will be identical to the first, except its length will be determined by the size and position of the turret when made.
Last edited: