- Joined
- Jun 4, 2008
- Messages
- 3,285
- Reaction score
- 630
After much blood, sweat, and tears, I finally got two useable parts made on the new CNC mill. There was a pretty steep learning curve, but I feel a lot more confident (before the fall?) about further progress.
Anyway, here's the two outer frames. No scale items, but they are about 4" tall.
Mill head tram was out for the first one on the left, but the ridges will polish out. :-[
I finally worked out how to hold the small flat parts on a fixture plate. I use some Rhino carpet tape, which holds quite well and is also fairly easy to remove at the end. For these two parts I also used clamps at various stages.
Anyway, here's the two outer frames. No scale items, but they are about 4" tall.
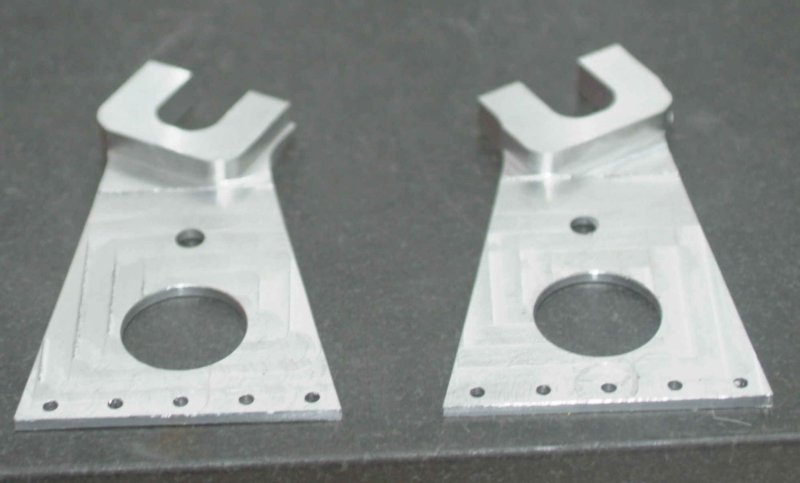
Mill head tram was out for the first one on the left, but the ridges will polish out. :-[
I finally worked out how to hold the small flat parts on a fixture plate. I use some Rhino carpet tape, which holds quite well and is also fairly easy to remove at the end. For these two parts I also used clamps at various stages.