Ok, time to get back to the engine. Its another cold one here in the Midwest so I didnt spend much time in the shop. For those that looked in on the vise stop build this is what I needed it for. I put the clearance holes in the valve and cover plates.
The part to be drilled was set up on parallels and indicated in using the edge sticking out and the fixed jaw of the vise, there wasnt enough of the part sticking out to get the edge finder on it. The vise stop was also set in place and tightened down.
Once the hole was located it was a simple matter of drilling it.
Here is where the stop came in handy. The part is symmetrical, the holes are in the same place relative to the corners. Once a hole is drilled the part is simply flipped and placed against the stop and the next hole drilled.
The part is then flipped again for the next hole, and so on till all are finished.
I also cut a piece for the steam chest and fly cut it to size. Next job is some 4-jaw work on the lathe. I get to work in heat for a change. Yes!
Thanks for looking in.
The part to be drilled was set up on parallels and indicated in using the edge sticking out and the fixed jaw of the vise, there wasnt enough of the part sticking out to get the edge finder on it. The vise stop was also set in place and tightened down.
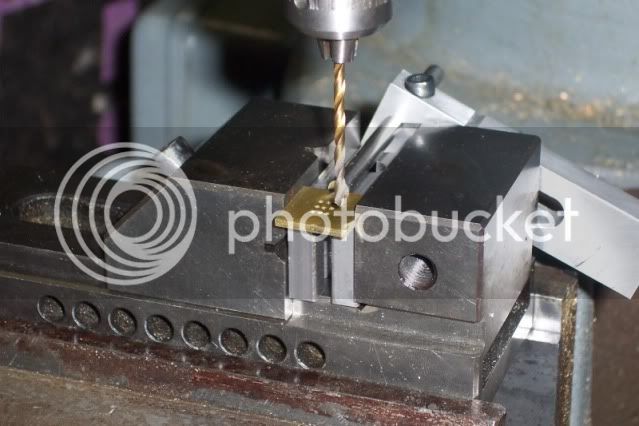
Once the hole was located it was a simple matter of drilling it.
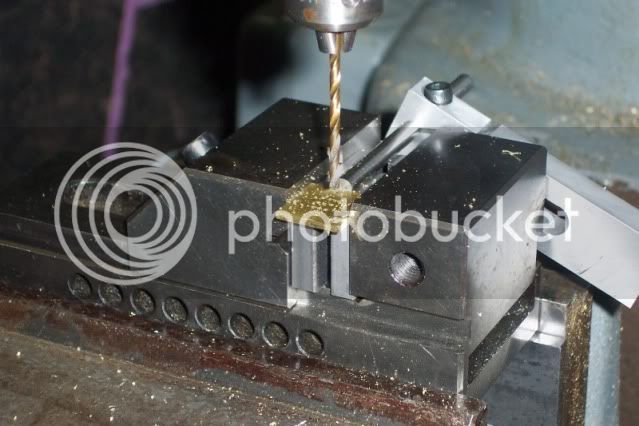
Here is where the stop came in handy. The part is symmetrical, the holes are in the same place relative to the corners. Once a hole is drilled the part is simply flipped and placed against the stop and the next hole drilled.
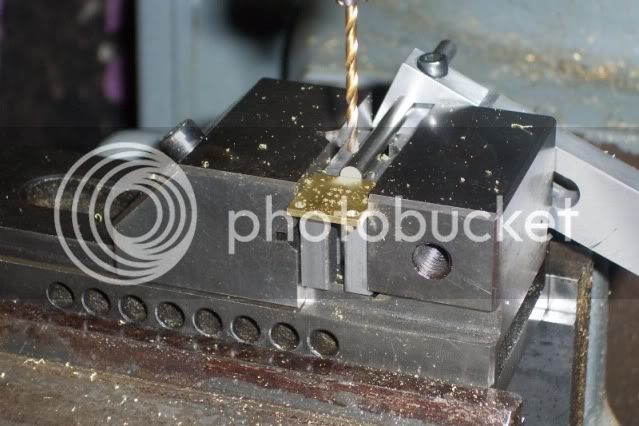
The part is then flipped again for the next hole, and so on till all are finished.
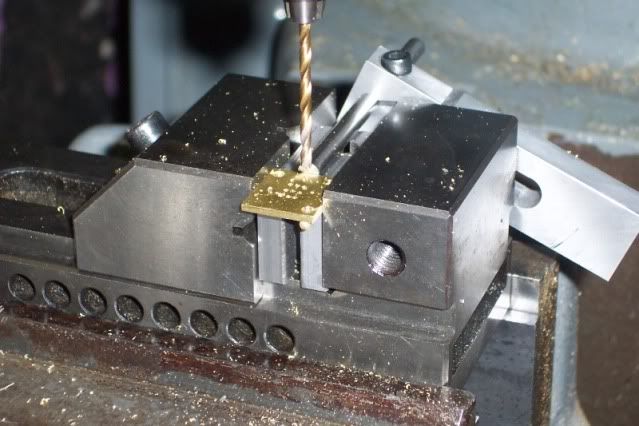
I also cut a piece for the steam chest and fly cut it to size. Next job is some 4-jaw work on the lathe. I get to work in heat for a change. Yes!
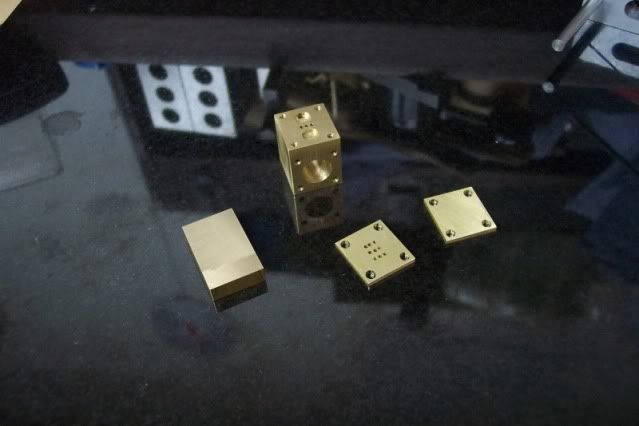
Thanks for looking in.