- Joined
- Jul 16, 2007
- Messages
- 2,986
- Reaction score
- 1,055
I lightly clamped the piece in the vise and cut it to length, .800. You can see where the drilled holes came through the part.
The part was raised in the vise to give enough room to cut the clearance for the screw heads. I needed to cut for .075 radius but not having a .150 end mill I just used a .125 and shifted it .012 on both sides.
The next step was to start trimming away the extra stock to form the circular shape on the outlet flange. I turned up a plug to fit in the port and also the diameter I would need to scribe the layout and do the final fitting to. With the face blued I scribed a layout line around the plug.
The outer shape was just a matter of nibbling away the stock close to the line.
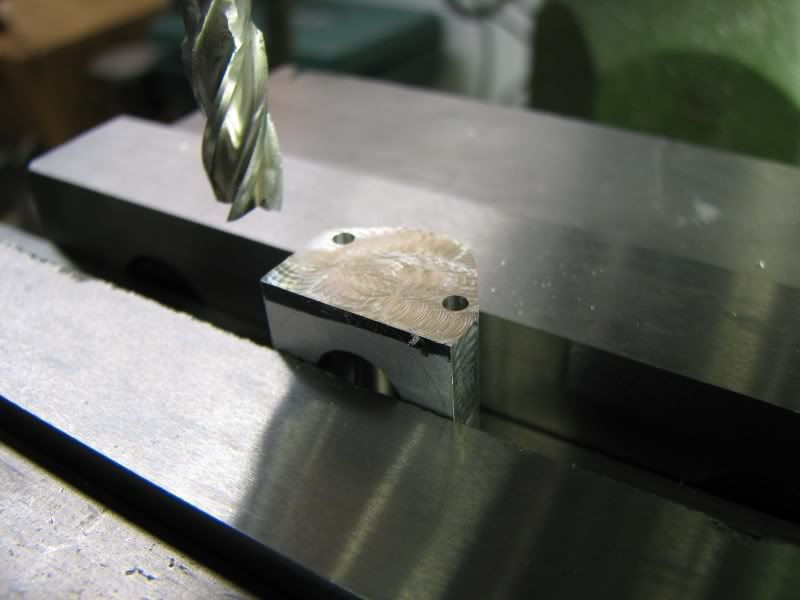
The part was raised in the vise to give enough room to cut the clearance for the screw heads. I needed to cut for .075 radius but not having a .150 end mill I just used a .125 and shifted it .012 on both sides.
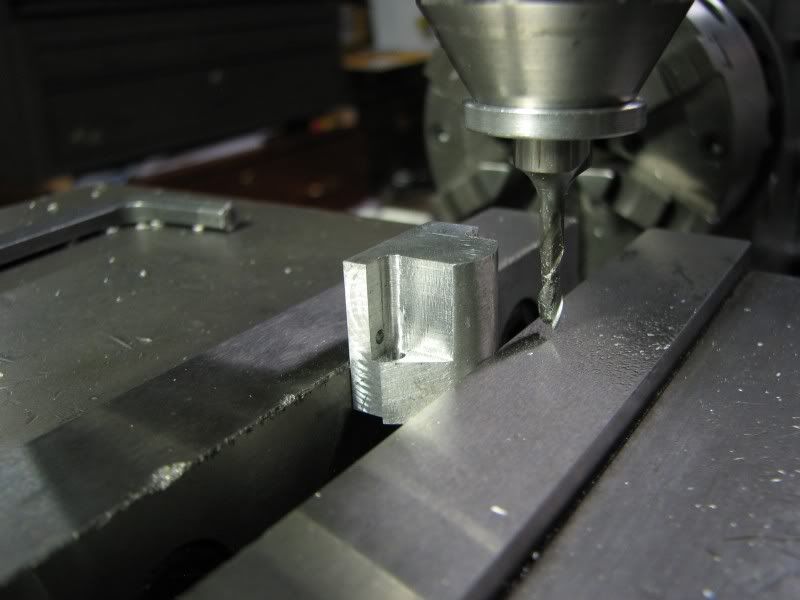
The next step was to start trimming away the extra stock to form the circular shape on the outlet flange. I turned up a plug to fit in the port and also the diameter I would need to scribe the layout and do the final fitting to. With the face blued I scribed a layout line around the plug.
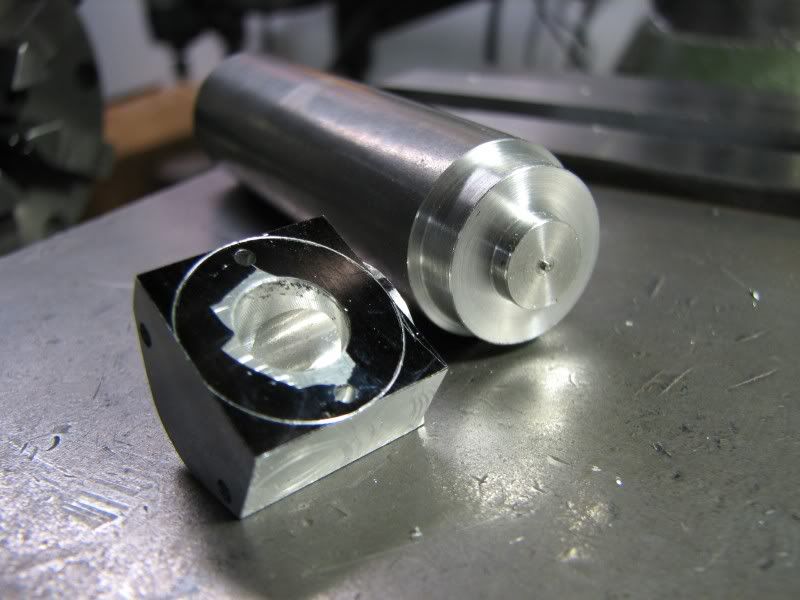
The outer shape was just a matter of nibbling away the stock close to the line.
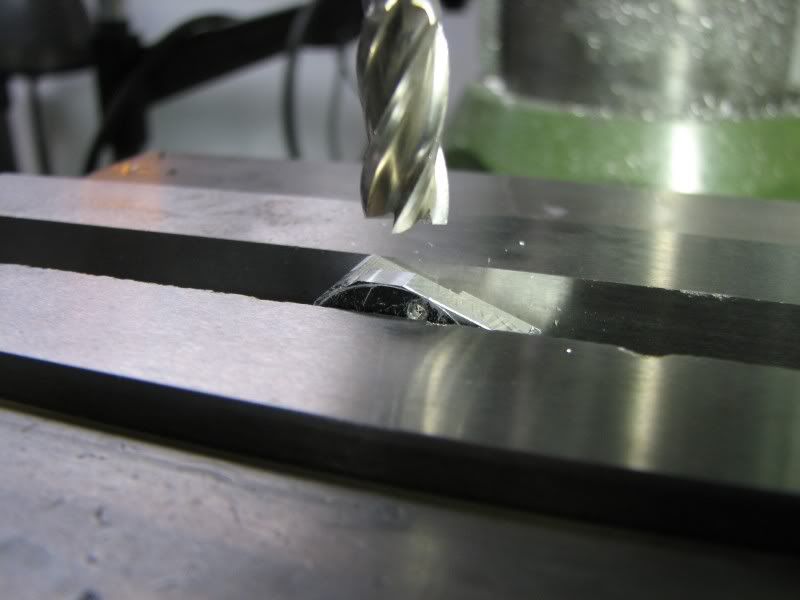