- Joined
- Jun 4, 2008
- Messages
- 3,285
- Reaction score
- 630
Did a few things preparatory to trying another steam up.
I had borrowed a blower for the stack from another club member, but I need to have my own. So found this Dayton exhaust blower on eBay for under $40 shipped:
To have it sit securely on the stack I turned down a scrap aluminum coaster to have a spigot that fit the stack, then bored out the center to 1.5":
Then wired to a 3-prong plug/wire from an extra PC power cable, and it seems to move a decent amount of air.
Another needed tool was a rod to clean flues. For the brush portion I bought a 3/4 inch "fixture brush" in the plumbing section at Lowes for $3, then used the bench grinder to grind the bristles down to a "not too tight" fit to the flues. After cutting the handle off, I made a steel ferrule and welded the brush shaft to it. Other end of the ferrule was tapped to screw onto the SS rod. Finally turned a simple handle from aluminum and used Loctite to fix it to the rod:
The rod is 3/16" diameter and flexible enough to do all the flues except the bottom center one from the smokebox. That flue will need to be cleaned from the firebox end.
The other mod was to use a T fitting for the pressure gauge plus a ball valve. The valve when open vents the boiler when filling with water. It can also be used to vent steam at the end of the day, possible for steam cleaning the loco itself.
I had borrowed a blower for the stack from another club member, but I need to have my own. So found this Dayton exhaust blower on eBay for under $40 shipped:
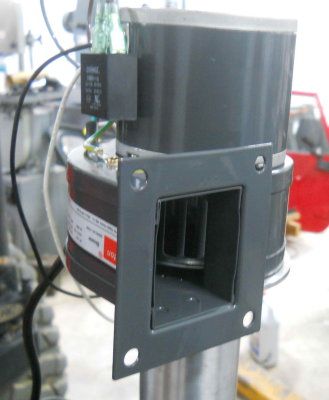
To have it sit securely on the stack I turned down a scrap aluminum coaster to have a spigot that fit the stack, then bored out the center to 1.5":
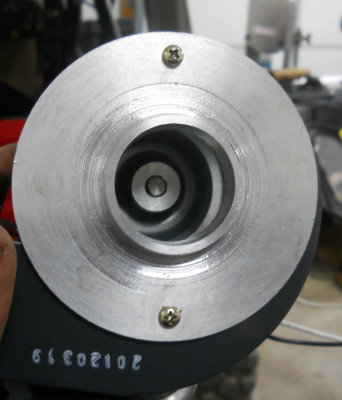
Then wired to a 3-prong plug/wire from an extra PC power cable, and it seems to move a decent amount of air.
Another needed tool was a rod to clean flues. For the brush portion I bought a 3/4 inch "fixture brush" in the plumbing section at Lowes for $3, then used the bench grinder to grind the bristles down to a "not too tight" fit to the flues. After cutting the handle off, I made a steel ferrule and welded the brush shaft to it. Other end of the ferrule was tapped to screw onto the SS rod. Finally turned a simple handle from aluminum and used Loctite to fix it to the rod:

The rod is 3/16" diameter and flexible enough to do all the flues except the bottom center one from the smokebox. That flue will need to be cleaned from the firebox end.
The other mod was to use a T fitting for the pressure gauge plus a ball valve. The valve when open vents the boiler when filling with water. It can also be used to vent steam at the end of the day, possible for steam cleaning the loco itself.
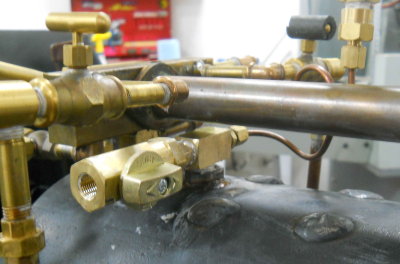