Philjoe5
Well-Known Member
- Joined
- Jul 12, 2007
- Messages
- 1,727
- Reaction score
- 321
Thanks Jim.
The valve cage assemblies are completely machined and will be "tweaked" once they're installed in the cylinder head. Stainless (303) valves, bronze valve cages, brass spring retainer and jam nut. Two required, and one spare. The springs I've used presently are what I had on hand.
I'll use the Rupnow method of adjusting spring tension by rotating the engine and watching intake valve movement. That's still in the future.
The next step will be to machine the ports in the cylinder head.
Thanks for looking in. Comments always appreciated
Cheers,
Phil
The valve cage assemblies are completely machined and will be "tweaked" once they're installed in the cylinder head. Stainless (303) valves, bronze valve cages, brass spring retainer and jam nut. Two required, and one spare. The springs I've used presently are what I had on hand.
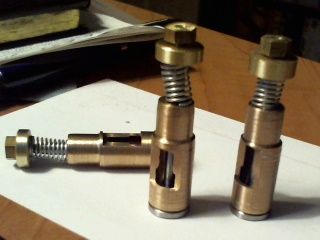
I'll use the Rupnow method of adjusting spring tension by rotating the engine and watching intake valve movement. That's still in the future.
The next step will be to machine the ports in the cylinder head.
Thanks for looking in. Comments always appreciated
Cheers,
Phil