Generatorgus
Senior Member
- Joined
- Feb 25, 2010
- Messages
- 362
- Reaction score
- 166
:-\Having completed the most difficult part of this build, so far, the rockers arms, now I can play with making the intake valve push rod and lifter mechanism.
The lifter has a roller actuated by the cam and a slot which guides it via the side shaft.
First, milling the slot .
The roller mounting hole drilled and tapped, then the decorative tapers cut in the sides.
The push rod hole also drilled and tapped, the part was cut off from the brass bar, then shaped and cleaned up a bit.
A pair of cam rollers cut from SS bar stock.
Then three almost identical shoulder screws made from ¼ SS hex. One for the lifter and two for the rockers.
Then a little push rod cut and treaded for the lifter.
After a little tweaking this is starting to look like it might just work.
And yeah, the exhaust valve adjuster is not quite centered on the valve(just another day's lesson in the life of this amature), something else that may be addressed later on in the game.
A few more small chores and I have to start brainstorming the carb, another fairly complex part coming to test me.
GUS
The lifter has a roller actuated by the cam and a slot which guides it via the side shaft.
First, milling the slot .
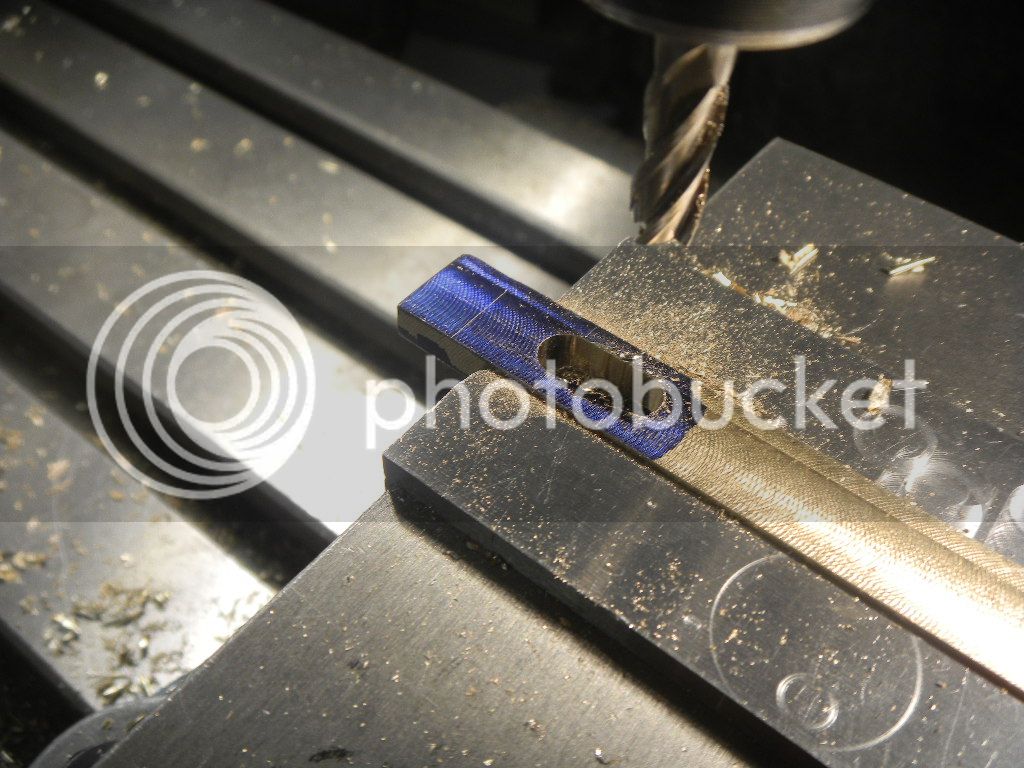
The roller mounting hole drilled and tapped, then the decorative tapers cut in the sides.
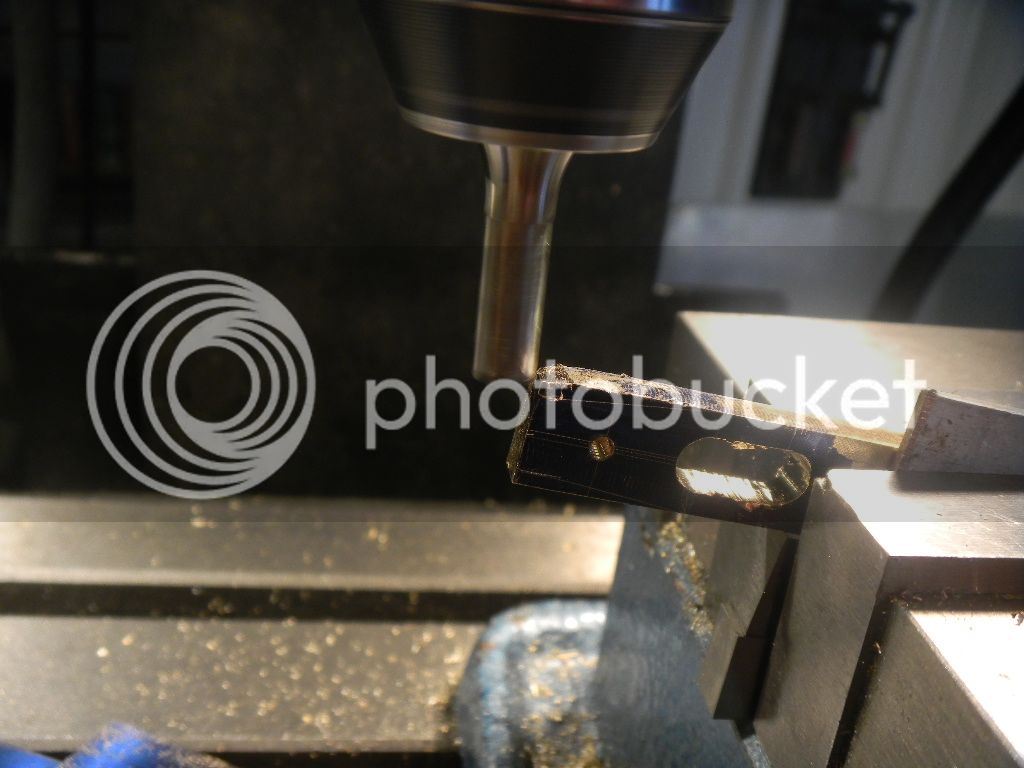
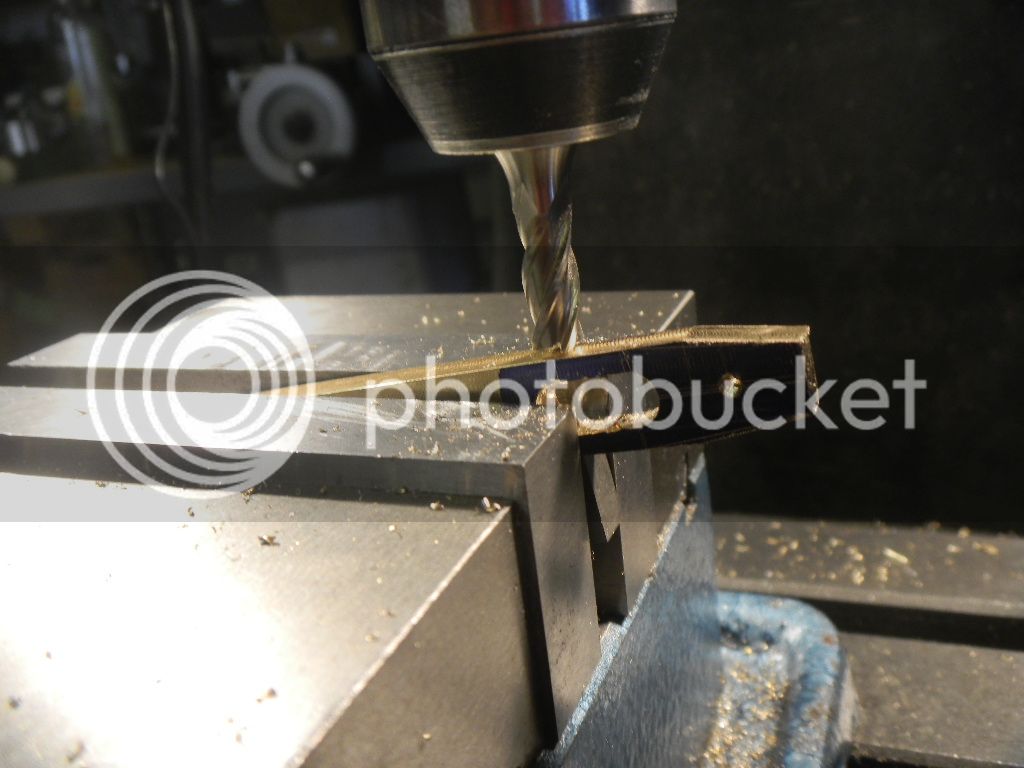
The push rod hole also drilled and tapped, the part was cut off from the brass bar, then shaped and cleaned up a bit.

A pair of cam rollers cut from SS bar stock.
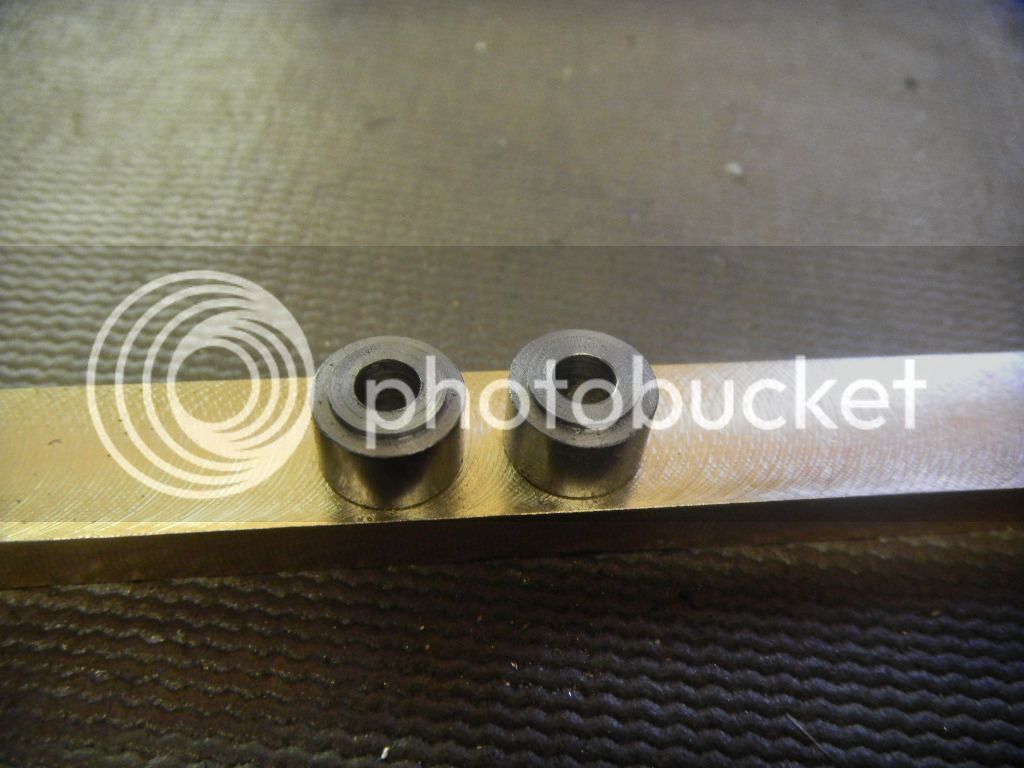
Then three almost identical shoulder screws made from ¼ SS hex. One for the lifter and two for the rockers.
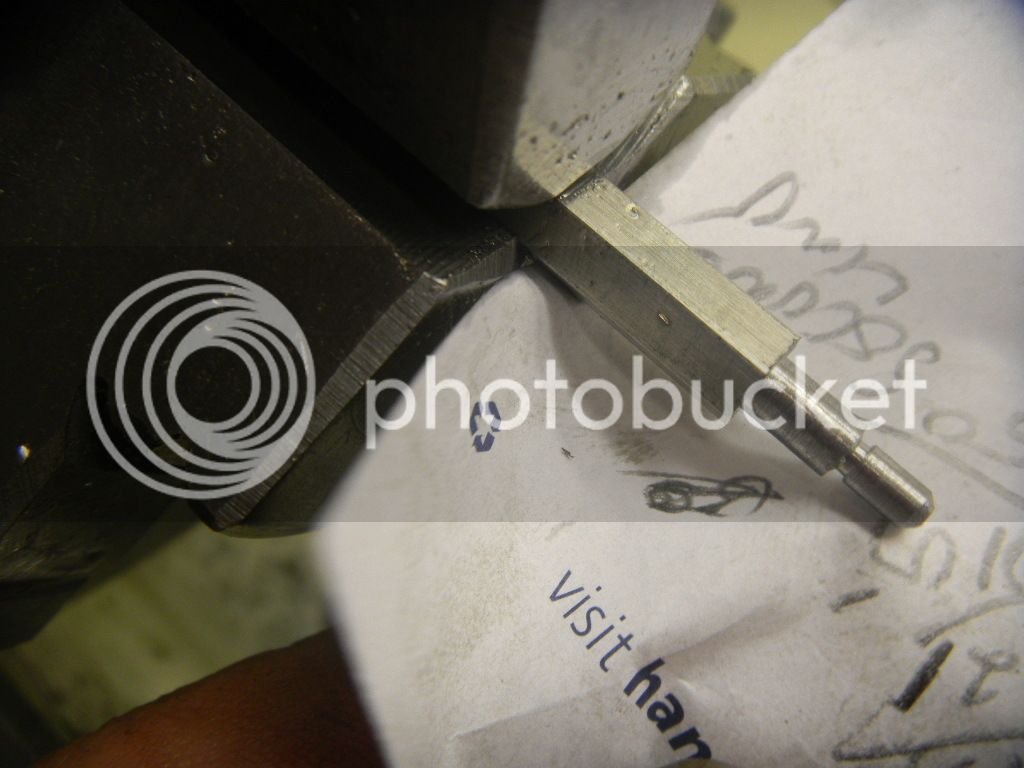
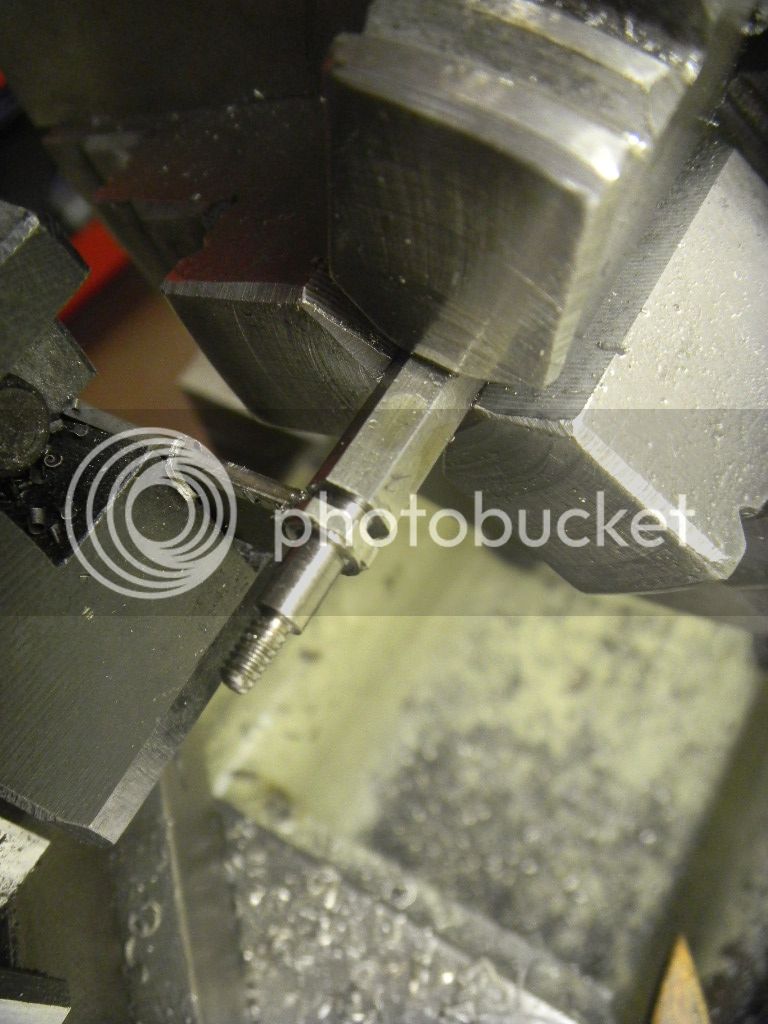
Then a little push rod cut and treaded for the lifter.
After a little tweaking this is starting to look like it might just work.
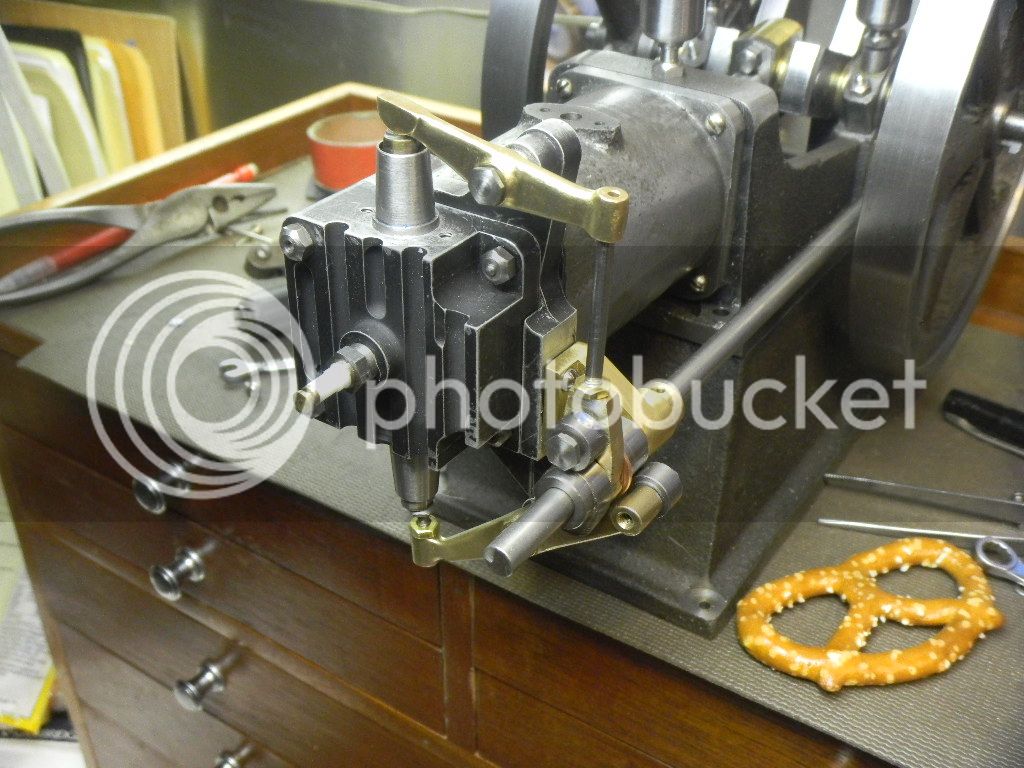
And yeah, the exhaust valve adjuster is not quite centered on the valve(just another day's lesson in the life of this amature), something else that may be addressed later on in the game.
A few more small chores and I have to start brainstorming the carb, another fairly complex part coming to test me.

GUS