Generatorgus
Senior Member
- Joined
- Feb 25, 2010
- Messages
- 362
- Reaction score
- 166
I bought these castings at the Blue Mountain Engine Show, here in Eastern PA, last summer.
I didnt know what they were at the time but at $25 I figured I couldnt even buy a flywheel casting for that much.
The cylinder casting is pretty rough looking with some sand breakouts and air pockets, giving me the impression that these were cast from an original casting set, but the base, sub base and flywheels looked pretty good.
I posted them here and got a positive ID as a Wyvern, along with some links to pictures and to Hemingway Kits, the English maker of these kits.
I still needed the rest of the casting and a set of plans.
The plans kind of fell in my lap when I told an acquaintance I had the major castings for a Wyvern. He said his dad had one of these kits and he had an extra set of prints.
That problem solved I was still short the bits and pieces castings, most important being the head and carb body. I got the name of an American producer of the Wyvern and I thought I could get the missing parts from him but after a number of unanswered calls and then finding out that he no longer makes the kits, that idea dissolved. I also considered buying the parts from Hemingway, but they only listed the entire the entire casting set. I never took the time to try to contact them.
The castings sat on the shelf for most of the last year and some months as I was still trying to get my Briesh Little Brother running and I still had my half scale Henry Ford engine sitting on the work bench ALSO in not running condition.
I promised myself I wasnt going to start messing around with another engine until I got those projects finished and RUNNING.
Even though I kept trying different fixes for the not running Little Brother, I kept hitting standstills as tried to figure out what fix I should try next.
During one of the standstills and wanting to run some machinery, I brought the Wyvern castings out and made a base plate and milled the bottom of the base and mounted it on the base plate I also milled the sub base at that time.
Still, no particular plan as what to do about the missing parts.
After many hours of and a lot of failed attempts, Im proud to say that both of my non running projects are now runners.
Ive actually been working on this model for more than a few weeks now and fully intended to start posting this build a while ago, but work and a few problems with my computer caused me to postpone.
I named this the Wyvernish build because Ive finally decided to attempt to make all of the missing parts. I have no idea how this is going to work out and I have some of my own ideas Id like to inject into the project.
It will not be built faithful to the plans, hence Wyvernish.
I'm going to keep working these posts as well as the engine until I catch up to real time.
GUS
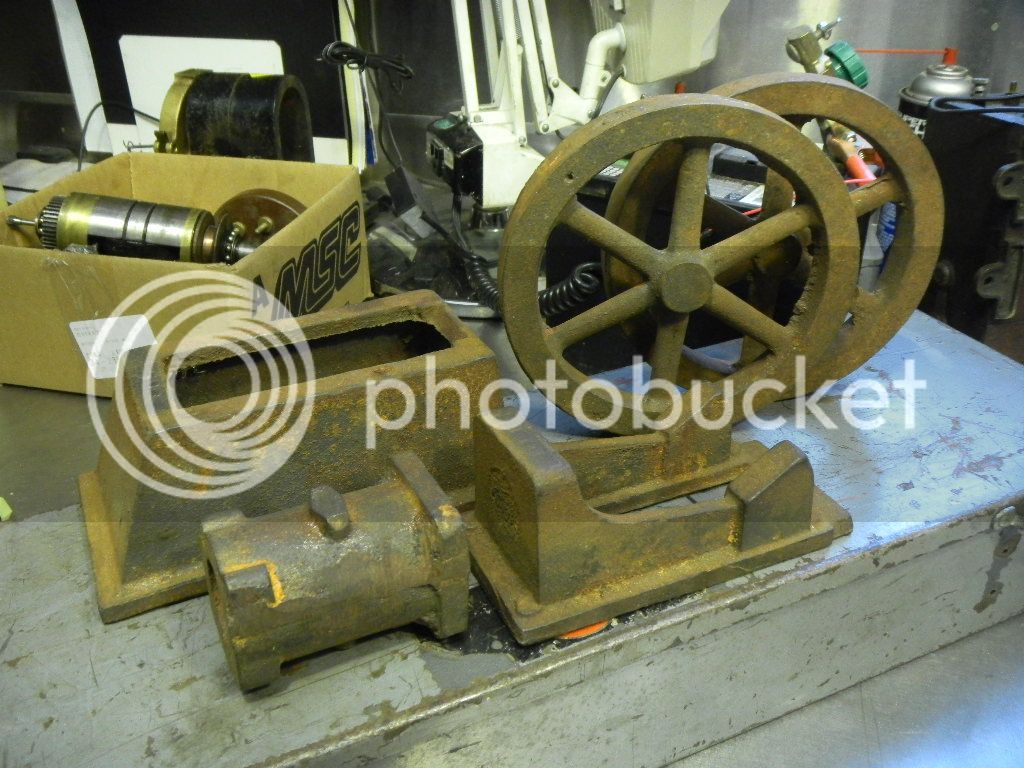
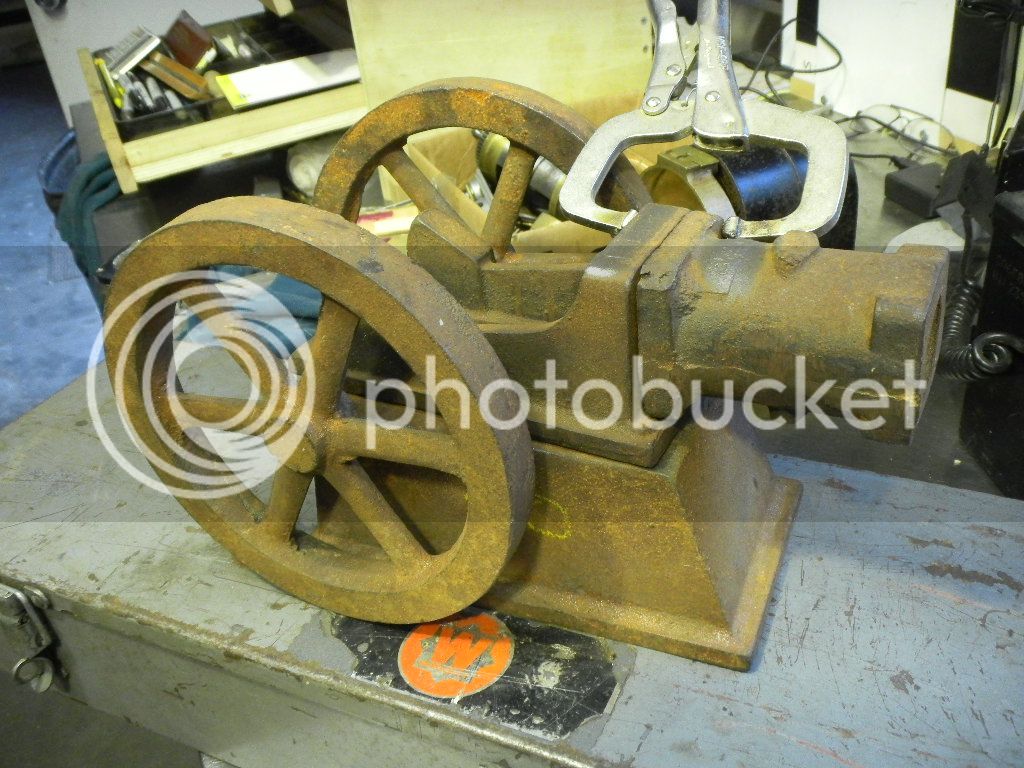
I didnt know what they were at the time but at $25 I figured I couldnt even buy a flywheel casting for that much.
The cylinder casting is pretty rough looking with some sand breakouts and air pockets, giving me the impression that these were cast from an original casting set, but the base, sub base and flywheels looked pretty good.
I posted them here and got a positive ID as a Wyvern, along with some links to pictures and to Hemingway Kits, the English maker of these kits.
I still needed the rest of the casting and a set of plans.
The plans kind of fell in my lap when I told an acquaintance I had the major castings for a Wyvern. He said his dad had one of these kits and he had an extra set of prints.
That problem solved I was still short the bits and pieces castings, most important being the head and carb body. I got the name of an American producer of the Wyvern and I thought I could get the missing parts from him but after a number of unanswered calls and then finding out that he no longer makes the kits, that idea dissolved. I also considered buying the parts from Hemingway, but they only listed the entire the entire casting set. I never took the time to try to contact them.
The castings sat on the shelf for most of the last year and some months as I was still trying to get my Briesh Little Brother running and I still had my half scale Henry Ford engine sitting on the work bench ALSO in not running condition.
I promised myself I wasnt going to start messing around with another engine until I got those projects finished and RUNNING.
Even though I kept trying different fixes for the not running Little Brother, I kept hitting standstills as tried to figure out what fix I should try next.
During one of the standstills and wanting to run some machinery, I brought the Wyvern castings out and made a base plate and milled the bottom of the base and mounted it on the base plate I also milled the sub base at that time.
Still, no particular plan as what to do about the missing parts.
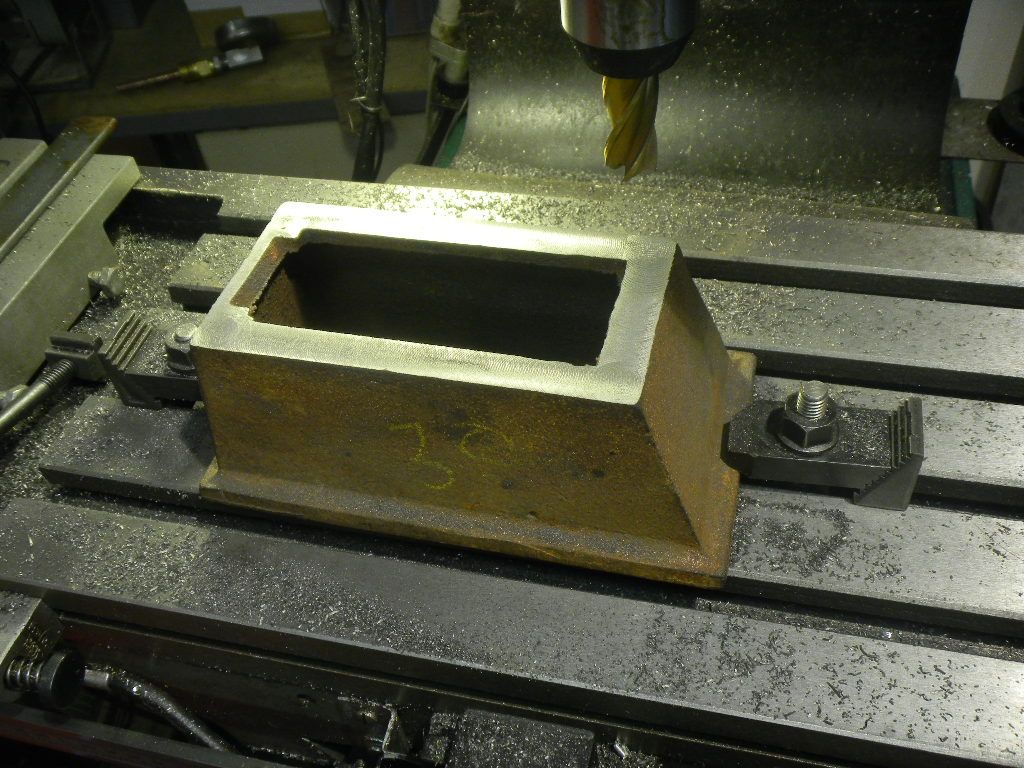
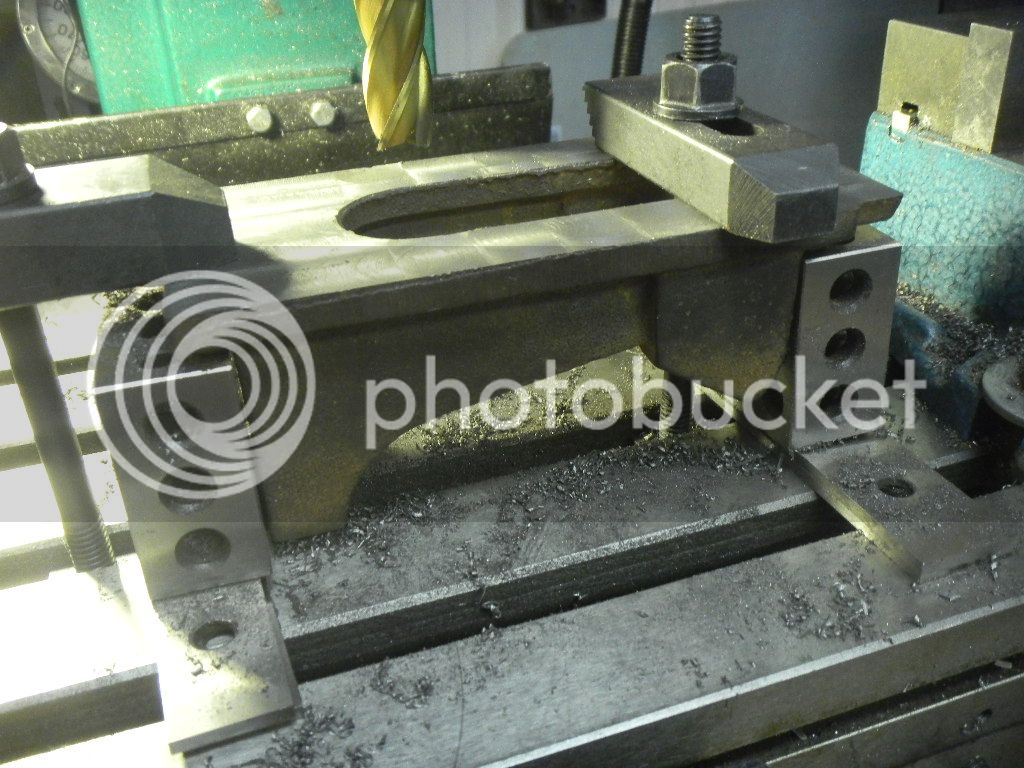
After many hours of and a lot of failed attempts, Im proud to say that both of my non running projects are now runners.
Ive actually been working on this model for more than a few weeks now and fully intended to start posting this build a while ago, but work and a few problems with my computer caused me to postpone.
I named this the Wyvernish build because Ive finally decided to attempt to make all of the missing parts. I have no idea how this is going to work out and I have some of my own ideas Id like to inject into the project.
It will not be built faithful to the plans, hence Wyvernish.
I'm going to keep working these posts as well as the engine until I catch up to real time.
GUS