- Joined
- Feb 17, 2008
- Messages
- 2,326
- Reaction score
- 440
The rest of the assembly is just gluing the parts together with epoxy. Use a fairly thin epoxy so the excess can squish out between the insulator and body when assembling. I use ordinary 5 minute epoxy.
First the wire is glued into the insulator. Coat the wire with some epoxy and press into the insulator. Clean off any excess epoxy.
After the epoxy has cured on the wire, coat about half of the insulator at the small end with a fres h batch of epoxy. Insert the insulator into the body until the tip of the center electrode almost touches the ground electrode.
Clean off any excess epoxy. Use a feeler gauge or a small piece of 0.025 sheet metal between the electrode tip and the ground electrode to set the gap at about 0.025 inch. If you are gentle you can remove the feeler gauge. Allow the epoxy to cure.
Tweak the ground electrode to set the gap if it has changed and you have a finished spark plug.
First the wire is glued into the insulator. Coat the wire with some epoxy and press into the insulator. Clean off any excess epoxy.
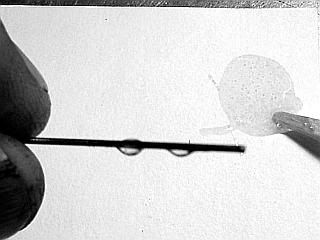
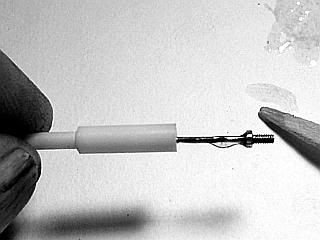
After the epoxy has cured on the wire, coat about half of the insulator at the small end with a fres h batch of epoxy. Insert the insulator into the body until the tip of the center electrode almost touches the ground electrode.
Clean off any excess epoxy. Use a feeler gauge or a small piece of 0.025 sheet metal between the electrode tip and the ground electrode to set the gap at about 0.025 inch. If you are gentle you can remove the feeler gauge. Allow the epoxy to cure.
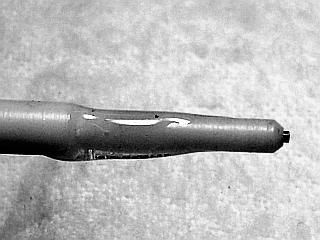
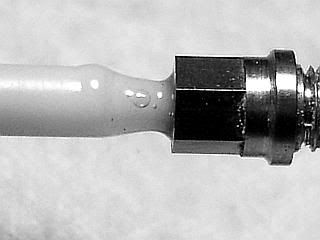
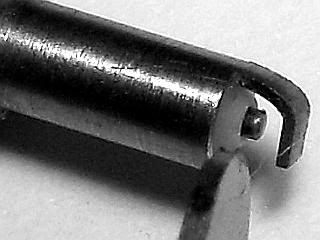
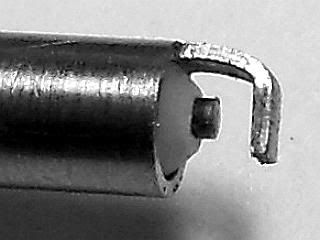
Tweak the ground electrode to set the gap if it has changed and you have a finished spark plug.
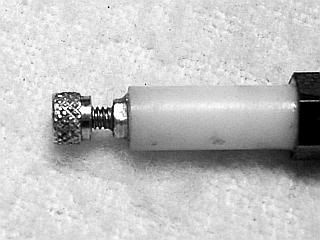
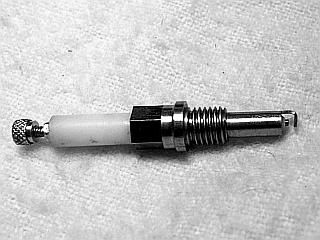