I really wasn't sure how to make this part. It could have been done any number of ways, but the lathe removes material so much faster than the mill that I decided to take a lathe approach. I started with a 6" square piece of 1/2" aluminum plate, scribed a circle on it larger than the largest dimension I would need from the center to the extreme outside edge of the finished part, roughed it out on the bandsaw, then used the old sticky tape trick to true it perfectly round. I then reversed the jaws in my lathe, gripped the plate, and used my home brewed trepanning tool to chew most of the unwanted material out of the center, then used a left hand carbide in the toolholder to finish the bottom of the excavation nicely and turn the O.D. of the spigot to a nice 1.181" diameter. I then drilled out the center in progressive steps up to 31/32" and finished up with a boring tool to get the exact bearing diameter. Tomorrow I will remove the outer rim with my bandsaw and finish the profile of the plate.
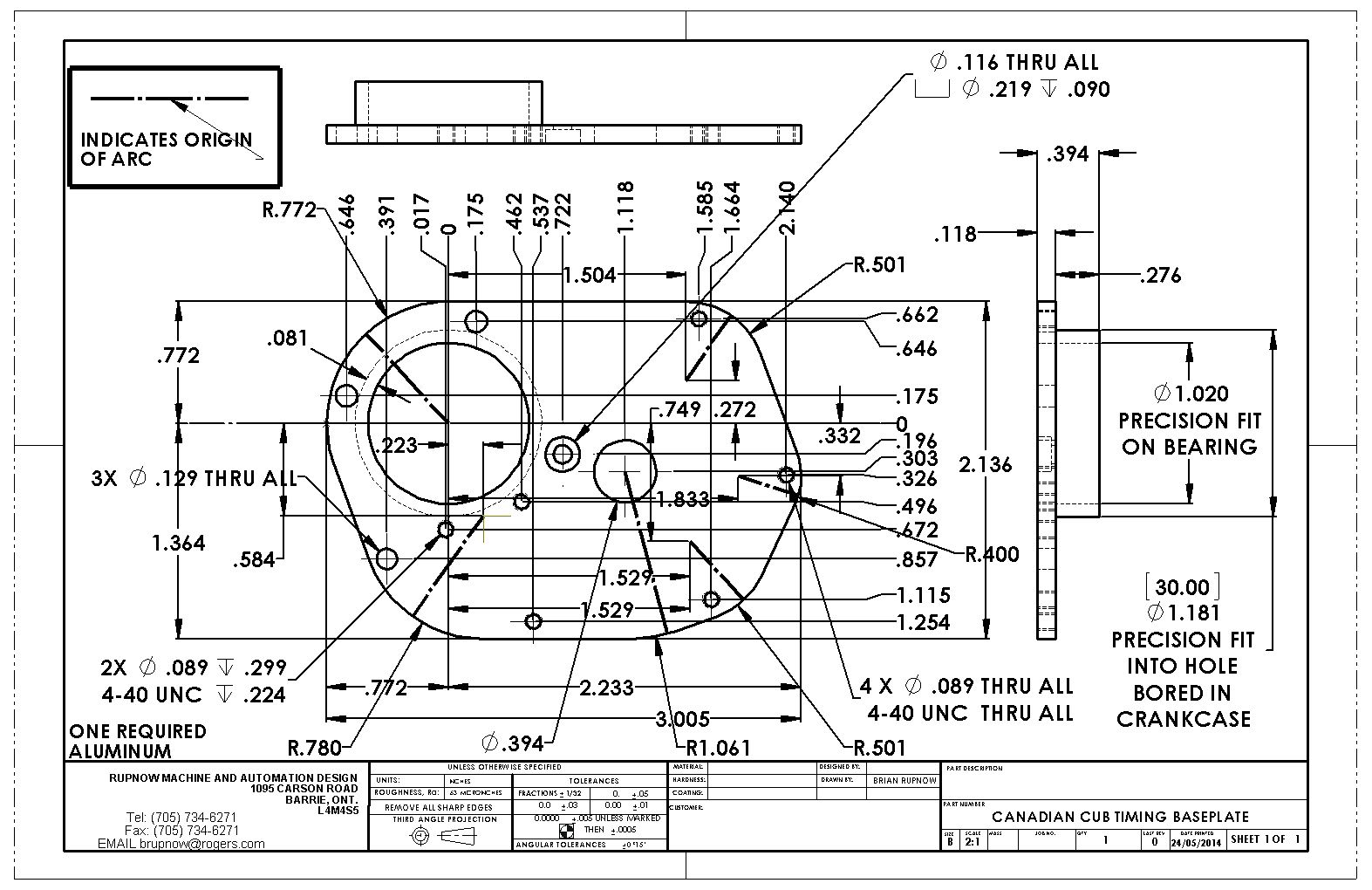
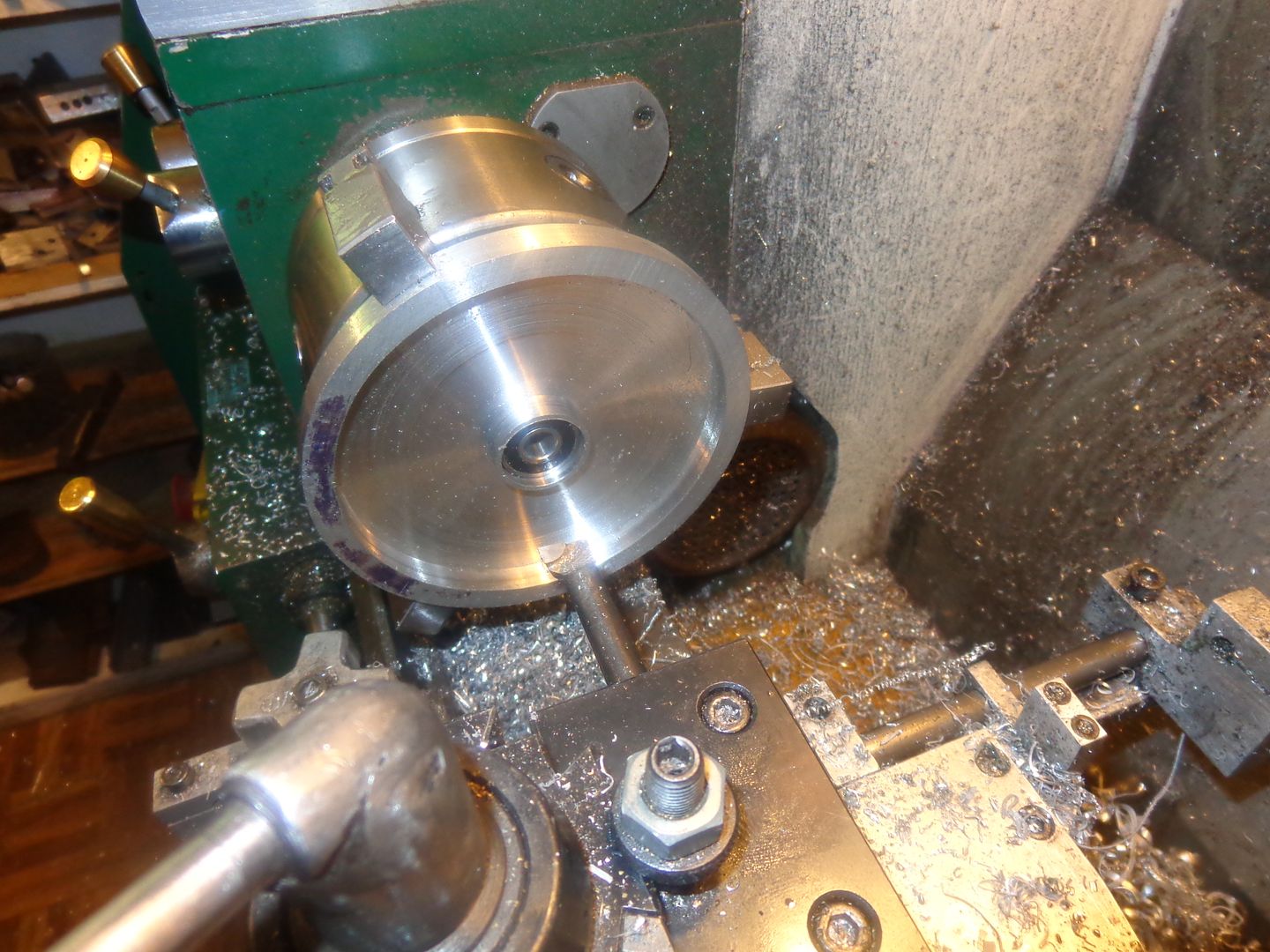