I learned long ago to never trust the centers that my computer or I calculate for meshing spur gears.--(Yes, there was life before computers---I used to do it all with trigonometry.) Now each time I make a gear train, even a simple one with only two gears, I use the measurements that will be used in machining the final part in which the gears will be fitted, to drill and ream holes in a scrap and then mount the gears and see how well they mesh. I must have lived right this week, because they mesh just fine!!! I also discovered a bonus today.(sitting at the left hand side of the picture.) While rooting around in my cast iron short ends looking for something to carve a gear from, I spied one piece that looked a bit larger than all the rest. I don't know what project it is left over from, but it is 1.6" diameter x 2" long. The cylinder for the Canadian Cub is 1.575" maximum diameter at the flange, x 1.705" long. If I can get lucky enough to have this piece clean up and leave me 1.575" at either end, I will have a free cylinder. Dang, I love it when that happens!!!
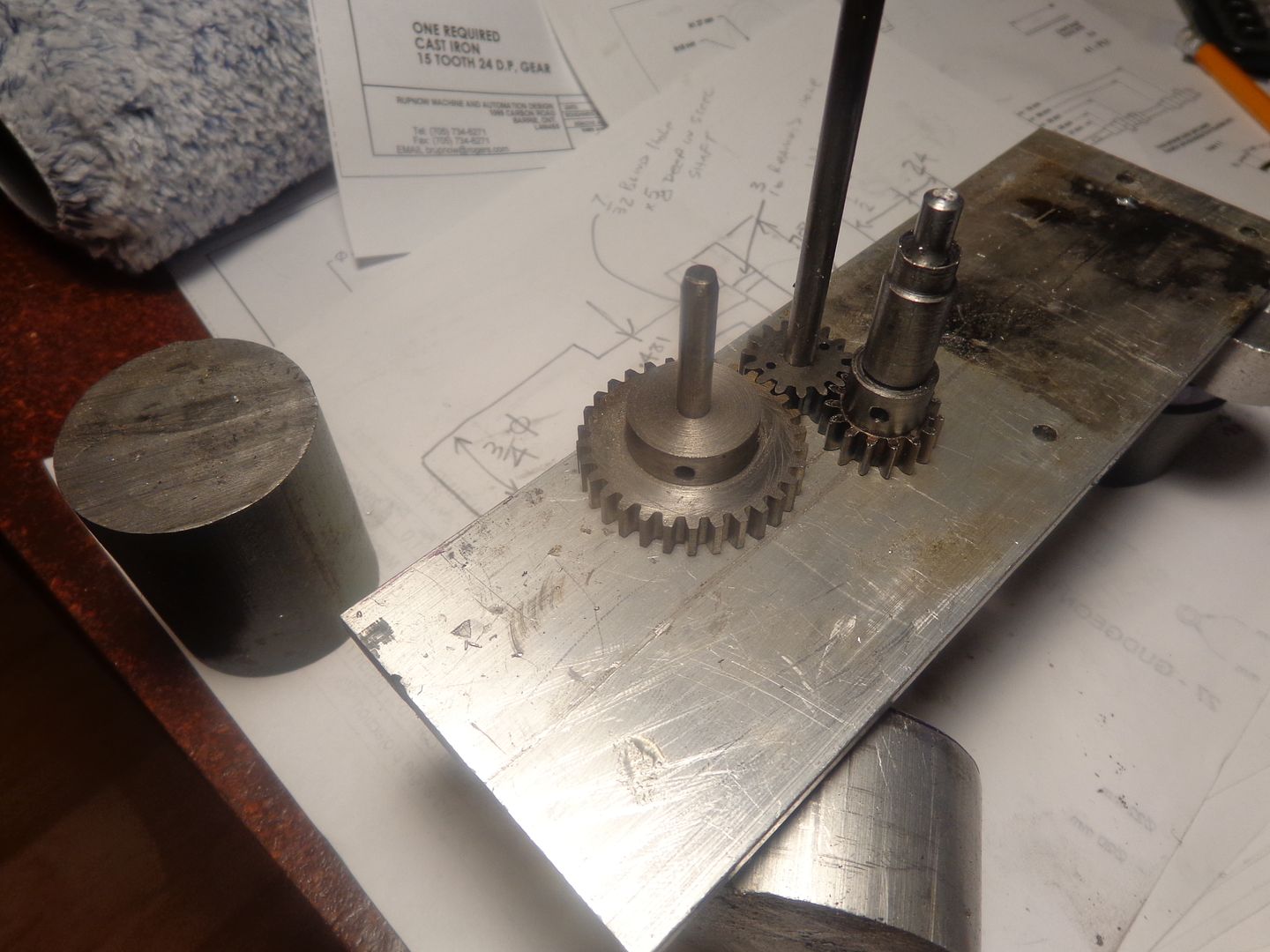