- Joined
- Jun 4, 2008
- Messages
- 3,285
- Reaction score
- 630
After remaking the two bad pins and grooving the brake bar, I found the SS springs needed for the brake system at McMaster-Carr, so ordered them. Now, it's time for brake shoes. I had read that Dave Sciavi has used aluminum for loco brake shoes, so I'm trying that first. The shoes require three setups, two on CNC and the final on the Bridgeport. Here's my experiment after op 1:
While the profiling is straightforward, train wheel treads are beveled 3 degrees. I approximated this by cutting tiny "ledges" at .025" separation. I had neglected to realize that this gives the larger radius at the top (i.e, top is inner side), so that the top needs the relief for the wheel flange, and as well the cheek cut needs to be 1/8" deeper. In any case, both the angle and radius of the face are good fits to my drivers, so fixing this one and making 3 more is straightforward.
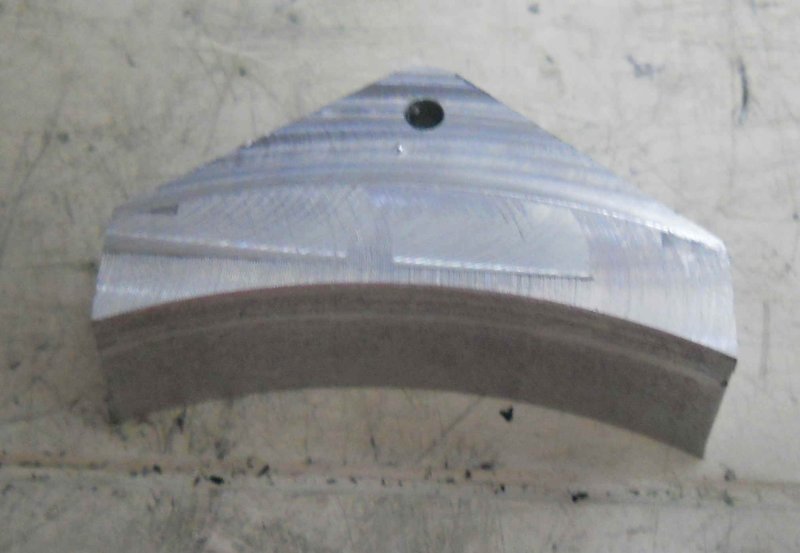
While the profiling is straightforward, train wheel treads are beveled 3 degrees. I approximated this by cutting tiny "ledges" at .025" separation. I had neglected to realize that this gives the larger radius at the top (i.e, top is inner side), so that the top needs the relief for the wheel flange, and as well the cheek cut needs to be 1/8" deeper. In any case, both the angle and radius of the face are good fits to my drivers, so fixing this one and making 3 more is straightforward.