vascon2196
Well-Known Member
- Joined
- Oct 2, 2009
- Messages
- 1,026
- Reaction score
- 312
Here are pictures of the flywheel casting from Martin Model and Casting. I never machined anything this large before so hopefully I didn't screw it up. I turned the outside diamter to clean, faced it, drilled & bored to 0.625". I don't like how it cleaned up nice on one end of the flywheel and it kept cutting further down towards the center. I have the runout within .002 to .003 thousandths and don't want to risk taking any more material off.
I suppose I could mask the outer face and paint the spokes and it won't be as noticable. I'm just not happy with how the face came out.
Chris
I suppose I could mask the outer face and paint the spokes and it won't be as noticable. I'm just not happy with how the face came out.
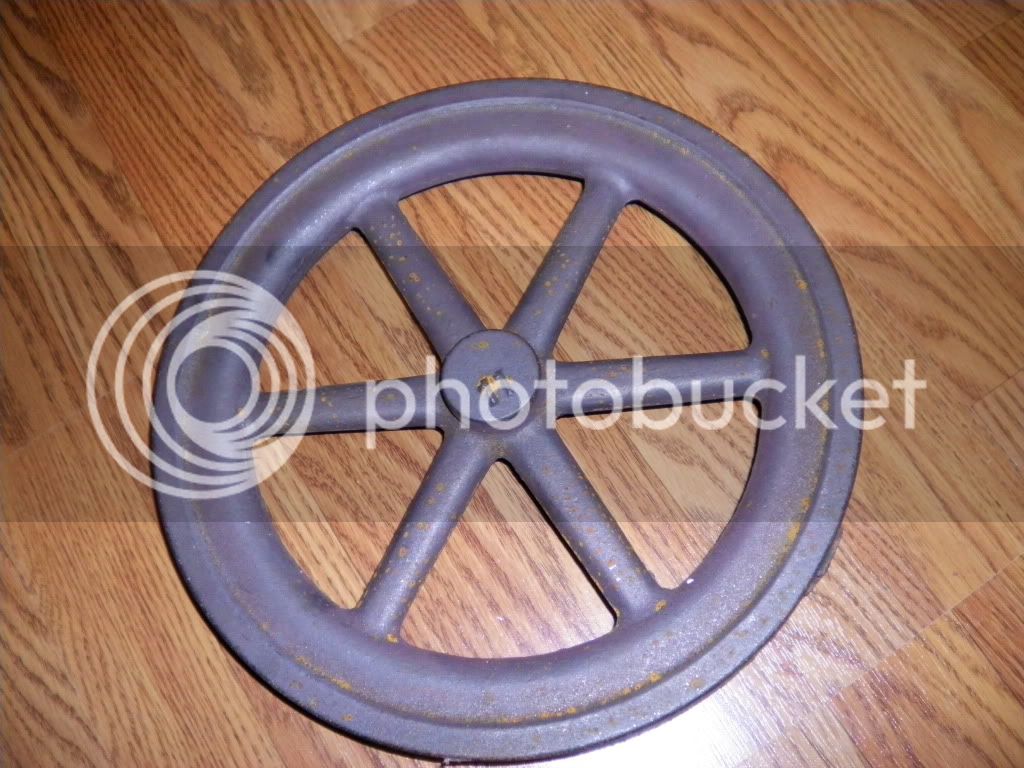
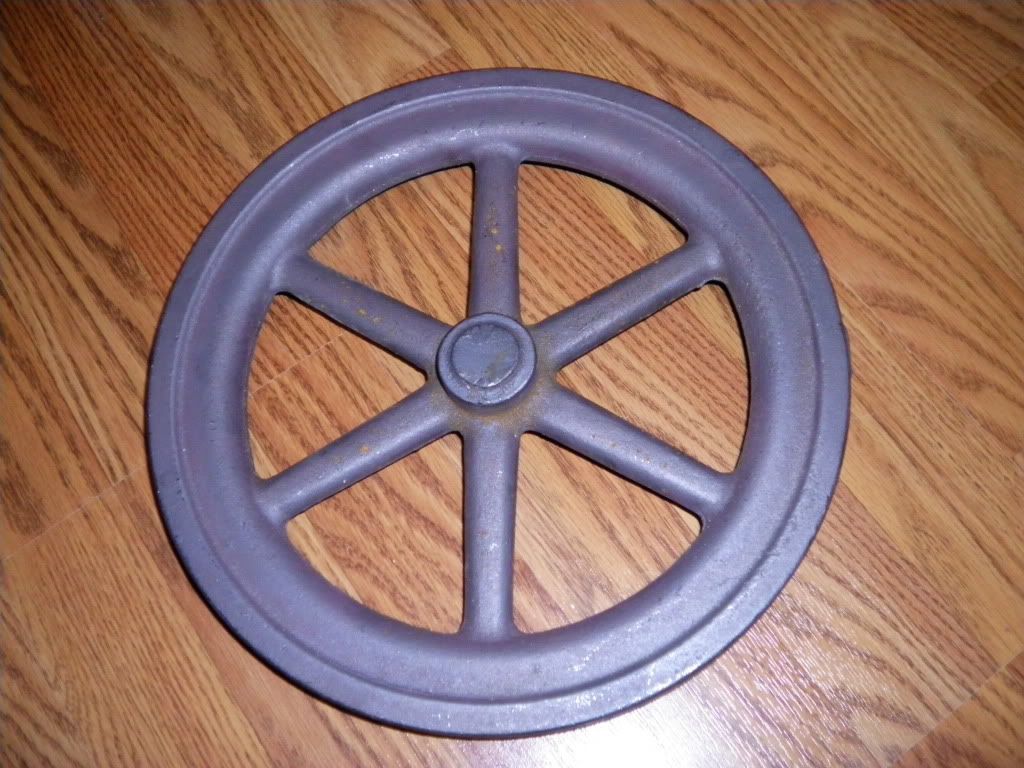
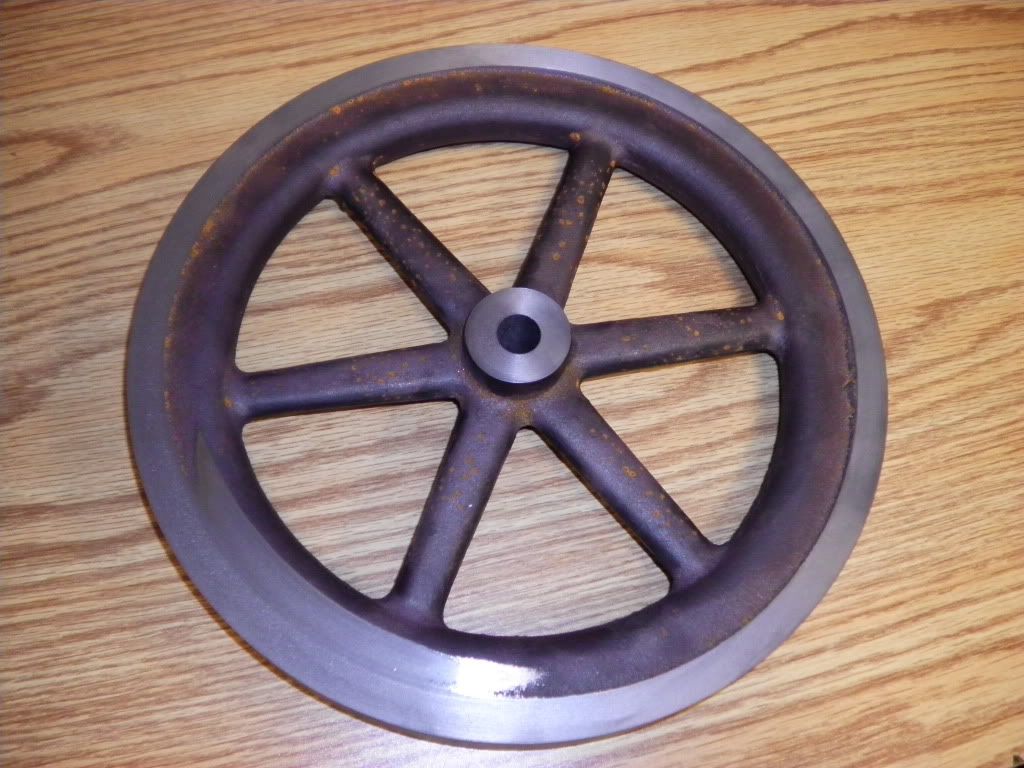
Chris