This is a pulley I just designed for it. Of course I want the pulley to be as small as possible in diameter to give a favourable ratio between it and the pumpjack pulley---BUT-- there is a caveat in doing that. If you make the pulley too small in diameter, it won't have enough contact area with the drive belt, and consequently won't have enough friction surface to drive the pumpjack.---It will just slip and spin. I'm going to take a stab at it and make a pulley as shown. Mainly because it "Looks about right" scale wise, and the fact that I have some 1" round brass and aluminum in my scrap bin.--Not much science here, but it should work.
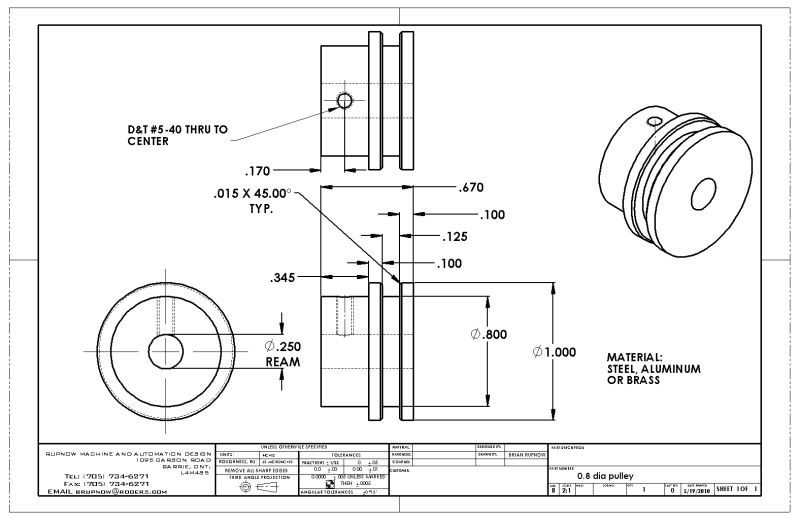