I know, I know---I said I wasn't going to do this. However, nobody else has jumped on it, and my phone's not ringing with work, so I am going to go ahead with it. In my estimation, the two trickiest pieces to machine are the "Tower Spacer" at the top of the tower, and the "Horsehead". I spent the lions share of today machining the "Tower Spacer" and believe me, if I could make it as fast as I designed it, I'd be a miracle worker!!! This is a fairly tricky piece with multiple set-ups, and its one of those pieces where you start with a goodly oversized chunk of aluminum to give you something to hang onto while you are working on it. I machined a piece of aluminum "to size" in two planes, and left it about 1 1/4" longer than the drawing called for. The pictures will explain this better than I can. First thing I did was drill and ream the 0.25" hole to size, then layed out the shape and set up my "Tilt a whirl" vice to let me machine all of the angles.
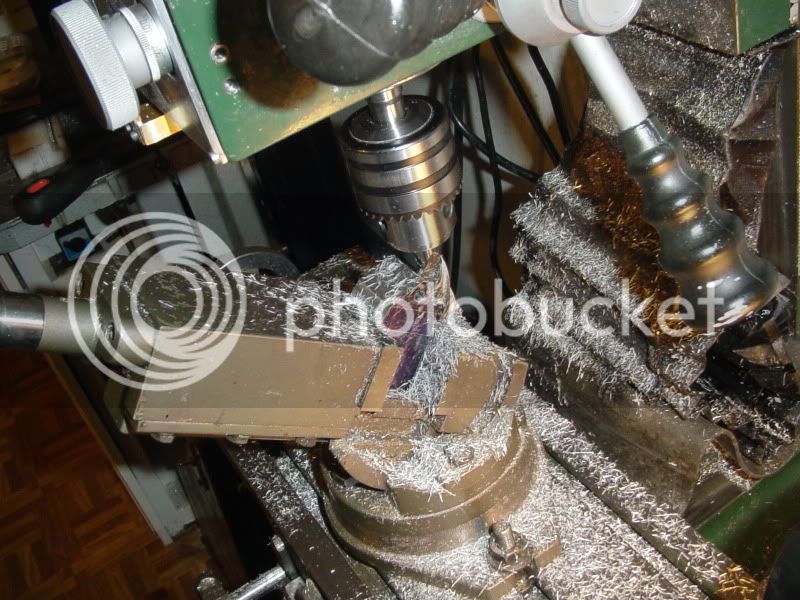