Alls well that ends well----The gear is in place, and looking good. I have to disassemble it yet and shorten those 4 screws up to be flush with the face of the hub because of clearance issues, but I'm happy with it.
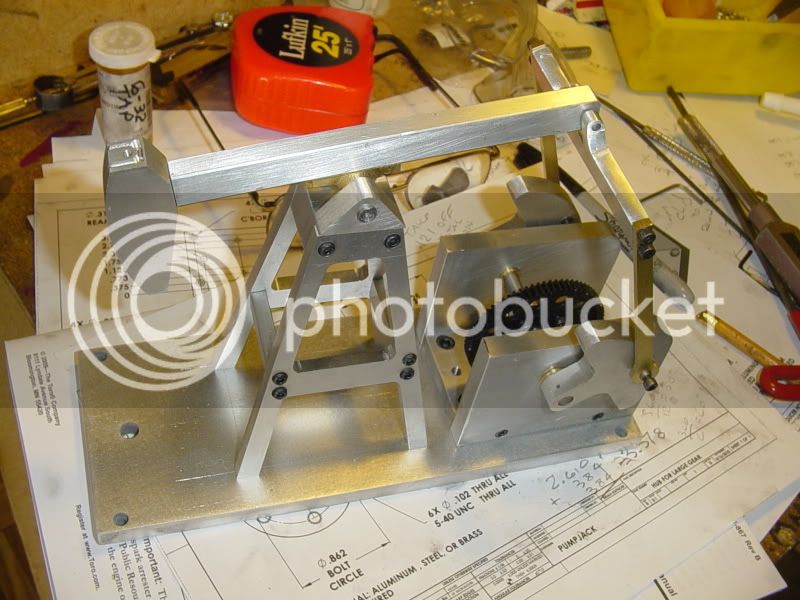
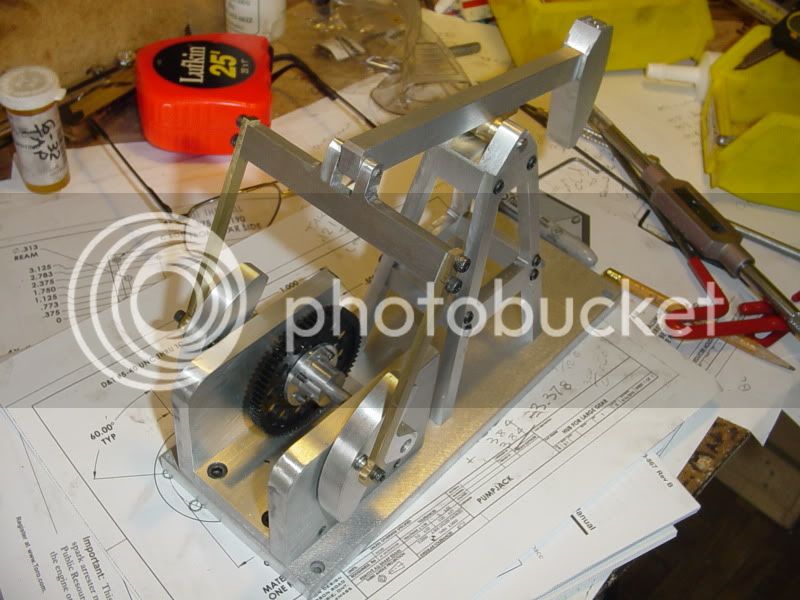
SAM in LA said:Brian,
Looks like your making good progress.
It is considered normal to talk to yourself.
The time to be careful is when you argue with yourself and lose. :big: :big:
SAM
T70MkIII said:Very nice build as always, Brian. What will be next?
Enter your email address to join: