- Joined
- Jan 17, 2009
- Messages
- 887
- Reaction score
- 81
Got the stream chest finished off, today.
Drilling the holes for the sealing gland.
Next up the little top hat to take the graphite cord.
Turned the OD and reamed through 3mm parted off flipped it round then used a slot drill to cut the flat bottom hole.
Then turned up the spool valve from some silver steel bar,
Drill and tap and acuratly turn the gap and over all length as these are important to the valve timing.
Camera went flat at this stage, and couldn't be arsed to get the spare out of the house.
Finished of the rest of the bits for the gland, this is how they all fit togethere
Then onto the valve cross head bar, made this from a bit of 1/4 square bar, so in the four jaw self centring chuck, rough out the steps.
Then with a thin tool and with the compound slewed over 5 deg turn the taper bits.
Over onto the mill and find the midle of the bar and drill though 3mm index to the outside bits and drill these through 3mm as well.
Then with an end mill thin the end bits out.
Time for an hows it looking.
Stew
Drilling the holes for the sealing gland.
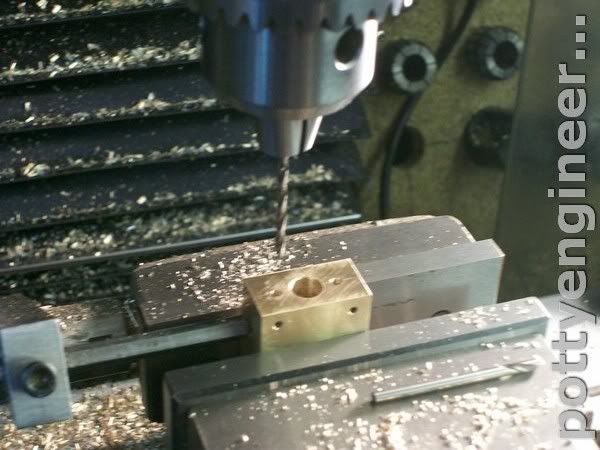
Next up the little top hat to take the graphite cord.
Turned the OD and reamed through 3mm parted off flipped it round then used a slot drill to cut the flat bottom hole.
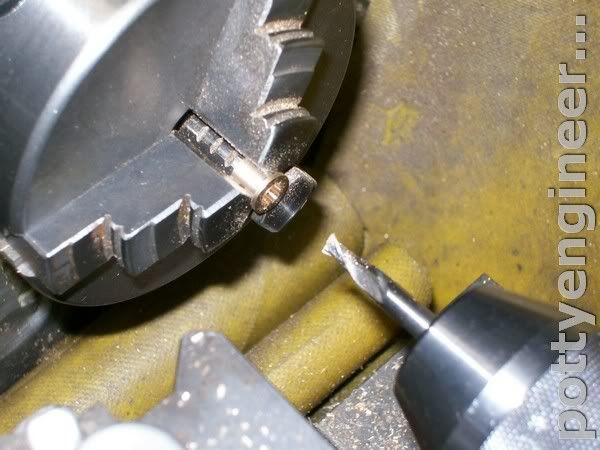
Then turned up the spool valve from some silver steel bar,
Drill and tap and acuratly turn the gap and over all length as these are important to the valve timing.
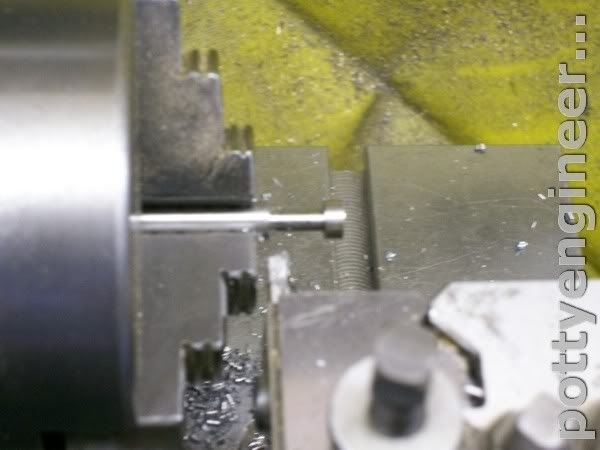
Camera went flat at this stage, and couldn't be arsed to get the spare out of the house.
Finished of the rest of the bits for the gland, this is how they all fit togethere
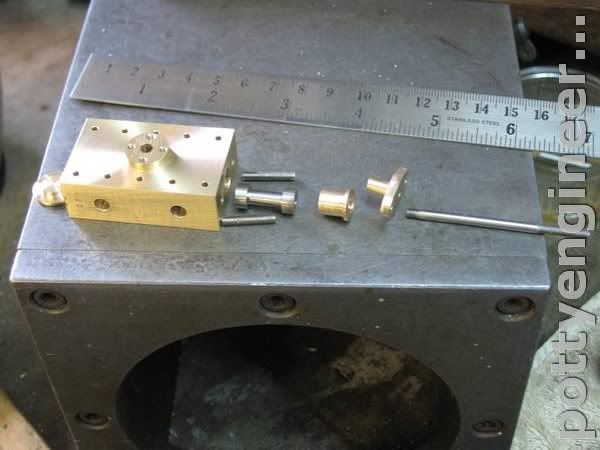
Then onto the valve cross head bar, made this from a bit of 1/4 square bar, so in the four jaw self centring chuck, rough out the steps.
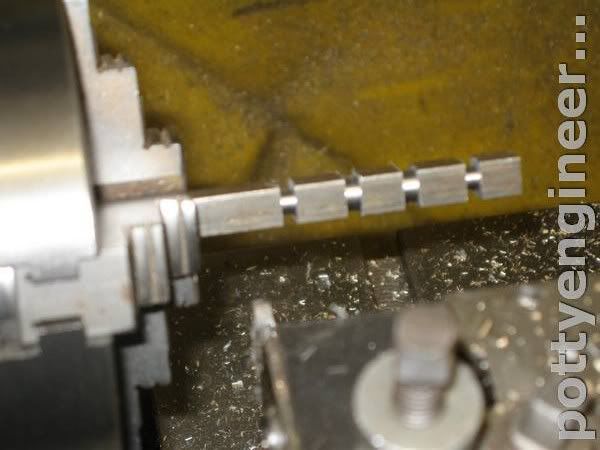
Then with a thin tool and with the compound slewed over 5 deg turn the taper bits.
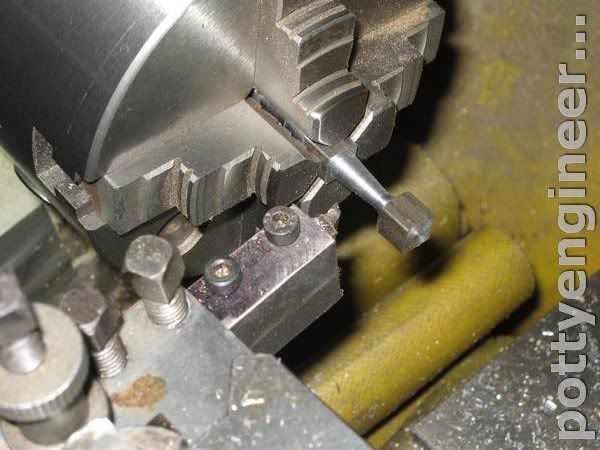
Over onto the mill and find the midle of the bar and drill though 3mm index to the outside bits and drill these through 3mm as well.
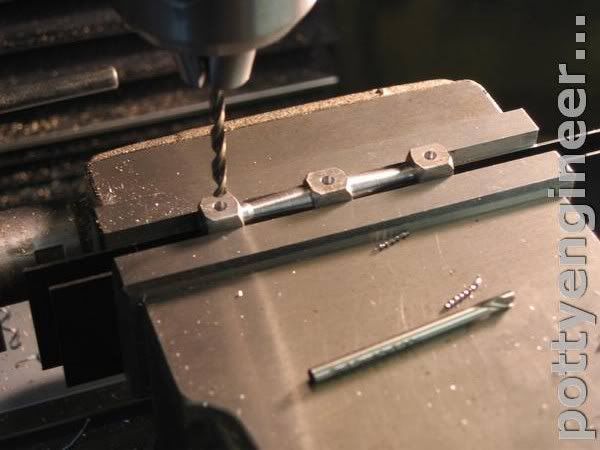
Then with an end mill thin the end bits out.
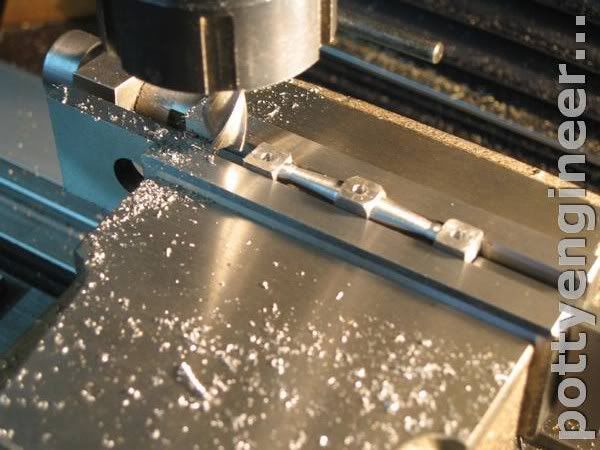
Time for an hows it looking.
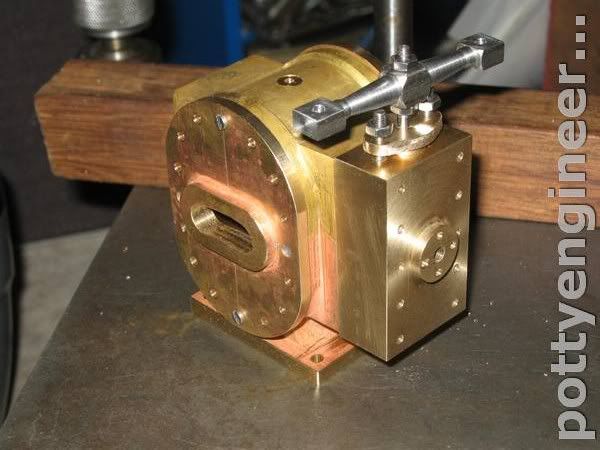
Stew