- Joined
- Jan 17, 2009
- Messages
- 887
- Reaction score
- 81
For those of you who don't know what a sine bar look like hers mine:
The bar is made to a very accurate length between the rollers and you just pack one end up to give the desired angle, that you calculate using the sine function.
Finished off the base by drilling the holes, the outer holes were countersunk flat bottom to take the bolting pads and the centre hole for countersunk for the cap screws.
Then turned up the pads.
And the bearings.
I like to push the reamer through with a centre with a drive carrier, that way it floats and you cut a true size.
This is how it all assembles together.
Then stuck the lot together with JB weld gave it 24 hrs to cure then cleaned them up.
Now they look good:- a big thanks to Jason and Ramon for sharing the method its one I will use again in future.
One more bit made the drive half shaft. I was going to make it from 12mm bar, but didn't have any so used 15mm and turned it down to 12mm with an 8mm step for the fly wheel threaded M8
Stew
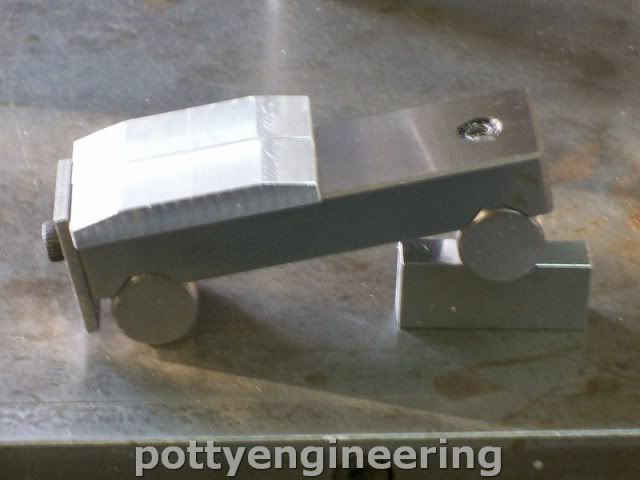
The bar is made to a very accurate length between the rollers and you just pack one end up to give the desired angle, that you calculate using the sine function.
Finished off the base by drilling the holes, the outer holes were countersunk flat bottom to take the bolting pads and the centre hole for countersunk for the cap screws.
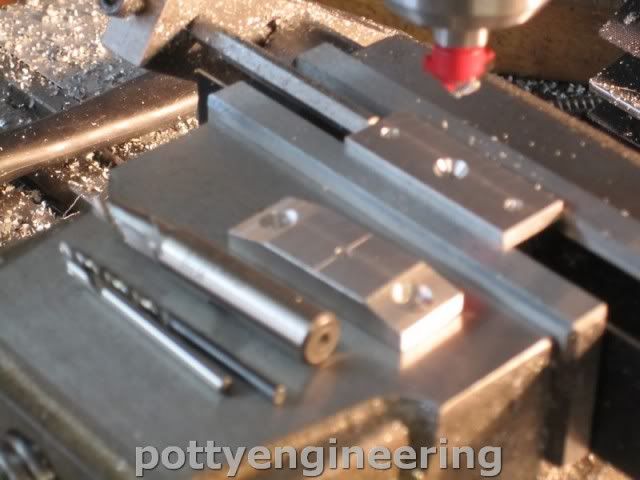
Then turned up the pads.
And the bearings.
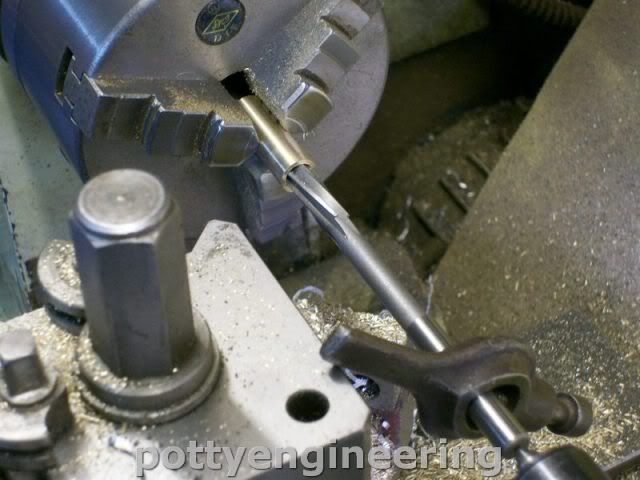
I like to push the reamer through with a centre with a drive carrier, that way it floats and you cut a true size.
This is how it all assembles together.
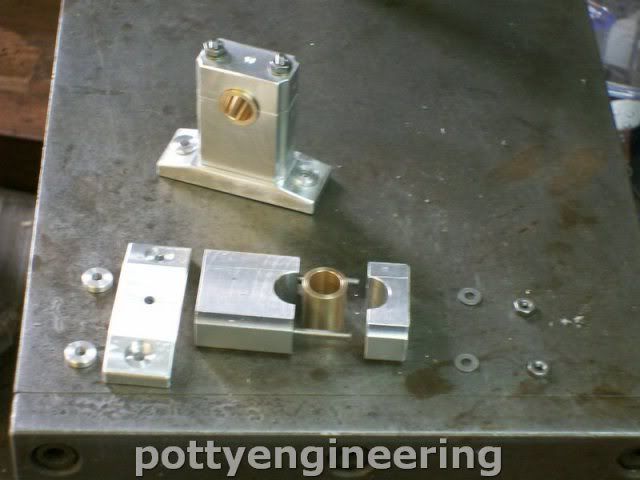
Then stuck the lot together with JB weld gave it 24 hrs to cure then cleaned them up.
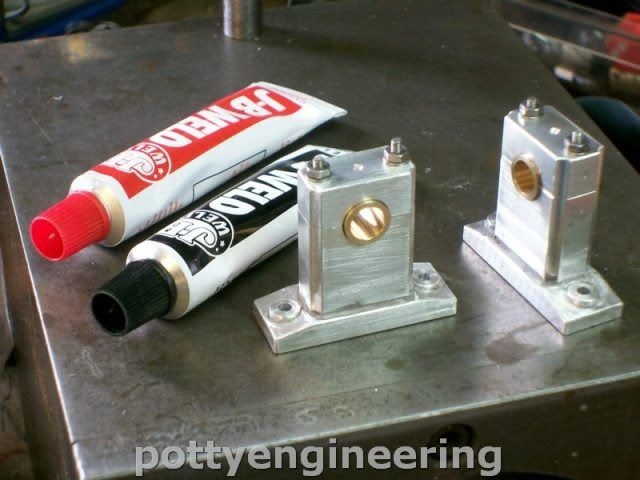
Now they look good:- a big thanks to Jason and Ramon for sharing the method its one I will use again in future.
One more bit made the drive half shaft. I was going to make it from 12mm bar, but didn't have any so used 15mm and turned it down to 12mm with an 8mm step for the fly wheel threaded M8
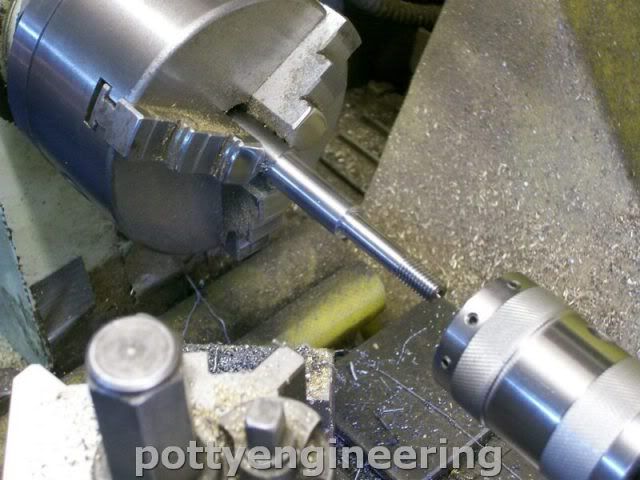
Stew