toolznthings
Project of the Month Winner
Hi All,
Kind of doing this backwards. I just finished the vertical engine design by Mike Pileski published in Steam & Stirling Book # 3. I find it easier to document and finish and then post the results. Other than some material changes and some construction changes very little was modified. The engine is a 1.500 bore x 1.500 stroke and mine will run on air. Overall height is approximately eleven inches high.
So here goes .... I'll start with the cylinder.
Turned the 3" diameter from 3 1/4" diameter 12L14 and faced one end. Center drilled and rough drilled. Bored and chamfered then polished the 1.500 bore. Parted off the stock leaving some grind stock on the overall finished length.
Next operation is at the surface grinder. I set up on the face that was done with the bore in the first operation and ground the opposite side first. This will insure that I will be perpendicular to the bore. Turned cylinder over and finished the overall length.
More build to come ......
Kind of doing this backwards. I just finished the vertical engine design by Mike Pileski published in Steam & Stirling Book # 3. I find it easier to document and finish and then post the results. Other than some material changes and some construction changes very little was modified. The engine is a 1.500 bore x 1.500 stroke and mine will run on air. Overall height is approximately eleven inches high.
So here goes .... I'll start with the cylinder.
Turned the 3" diameter from 3 1/4" diameter 12L14 and faced one end. Center drilled and rough drilled. Bored and chamfered then polished the 1.500 bore. Parted off the stock leaving some grind stock on the overall finished length.
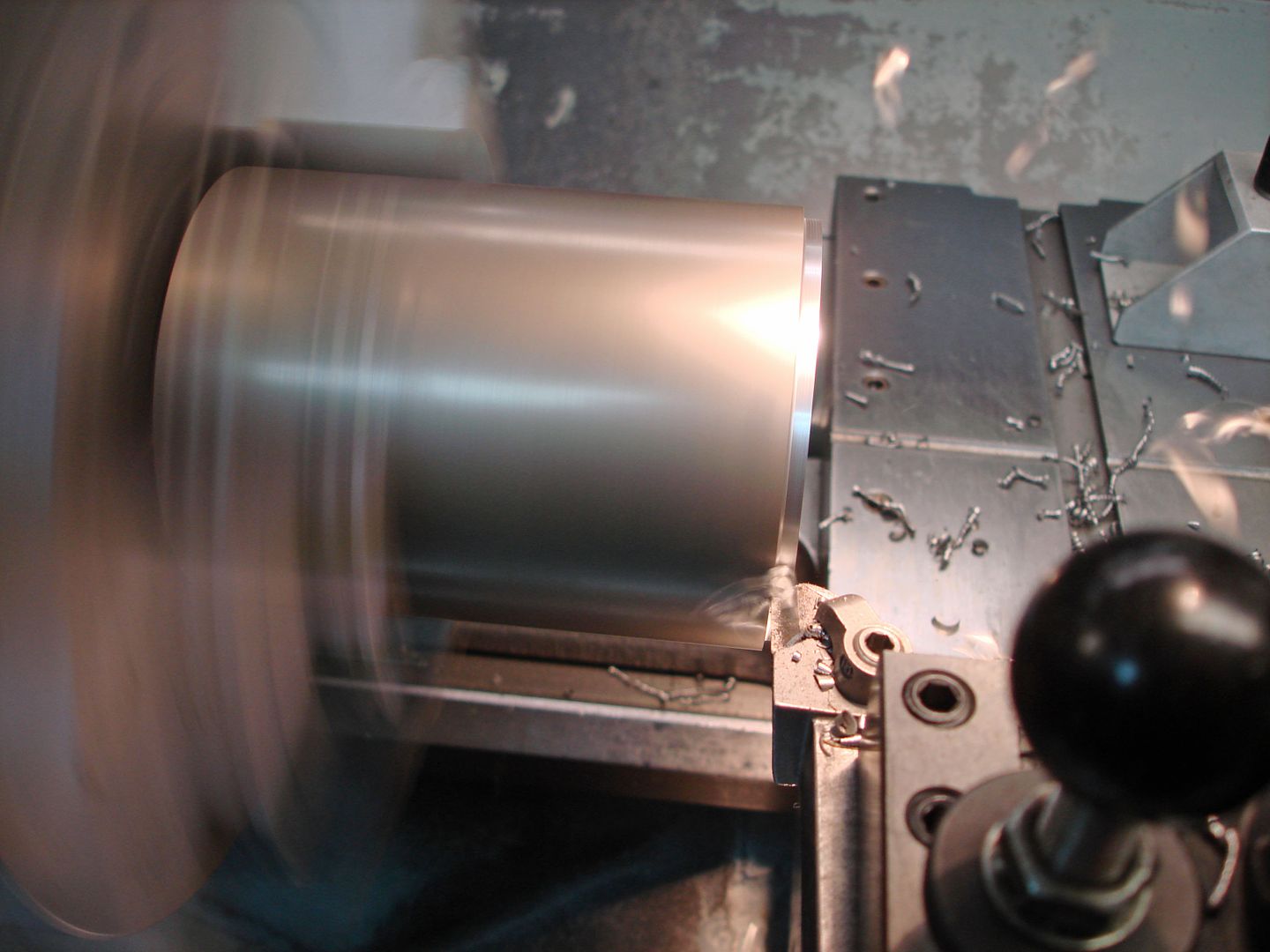
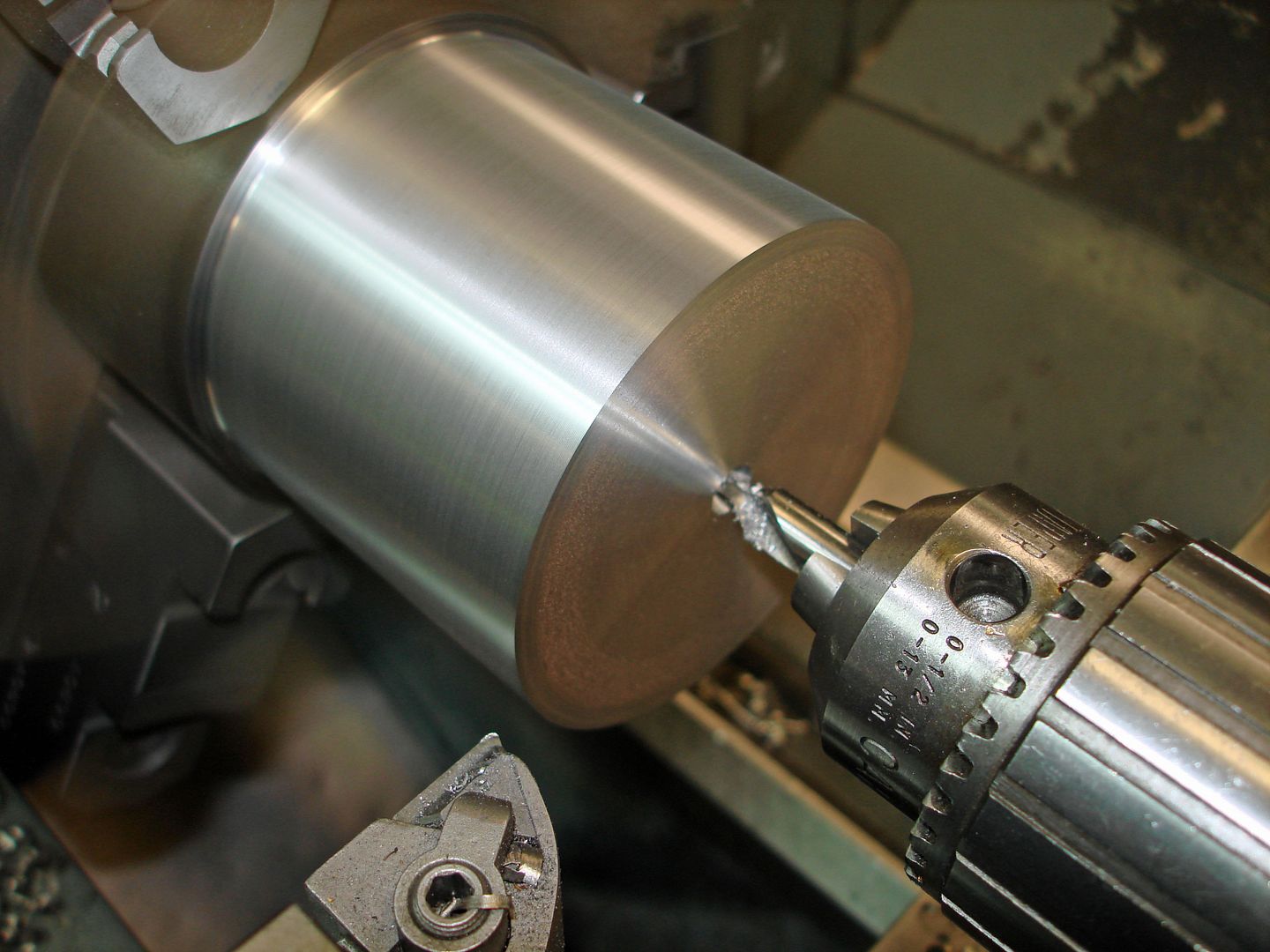
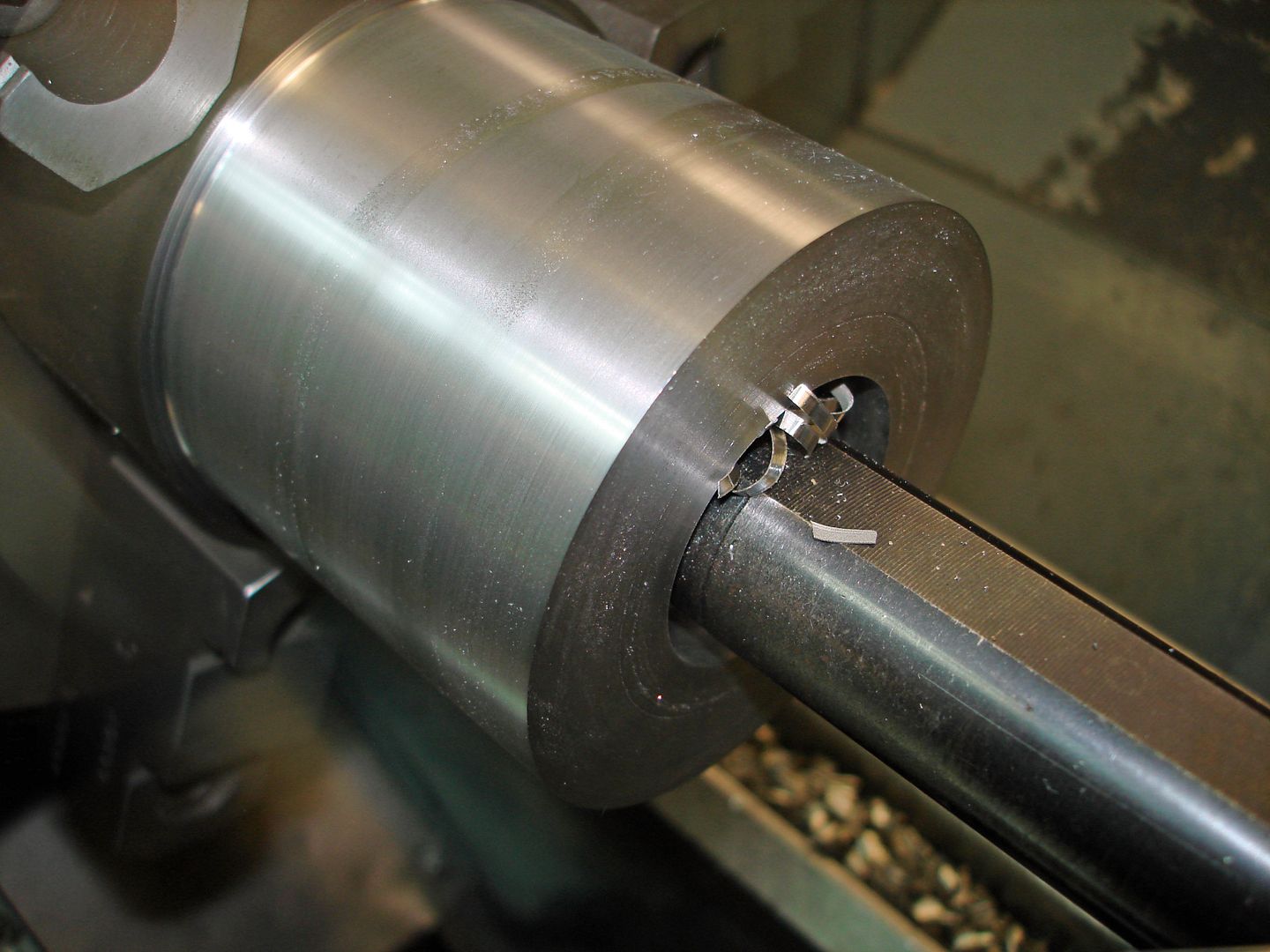
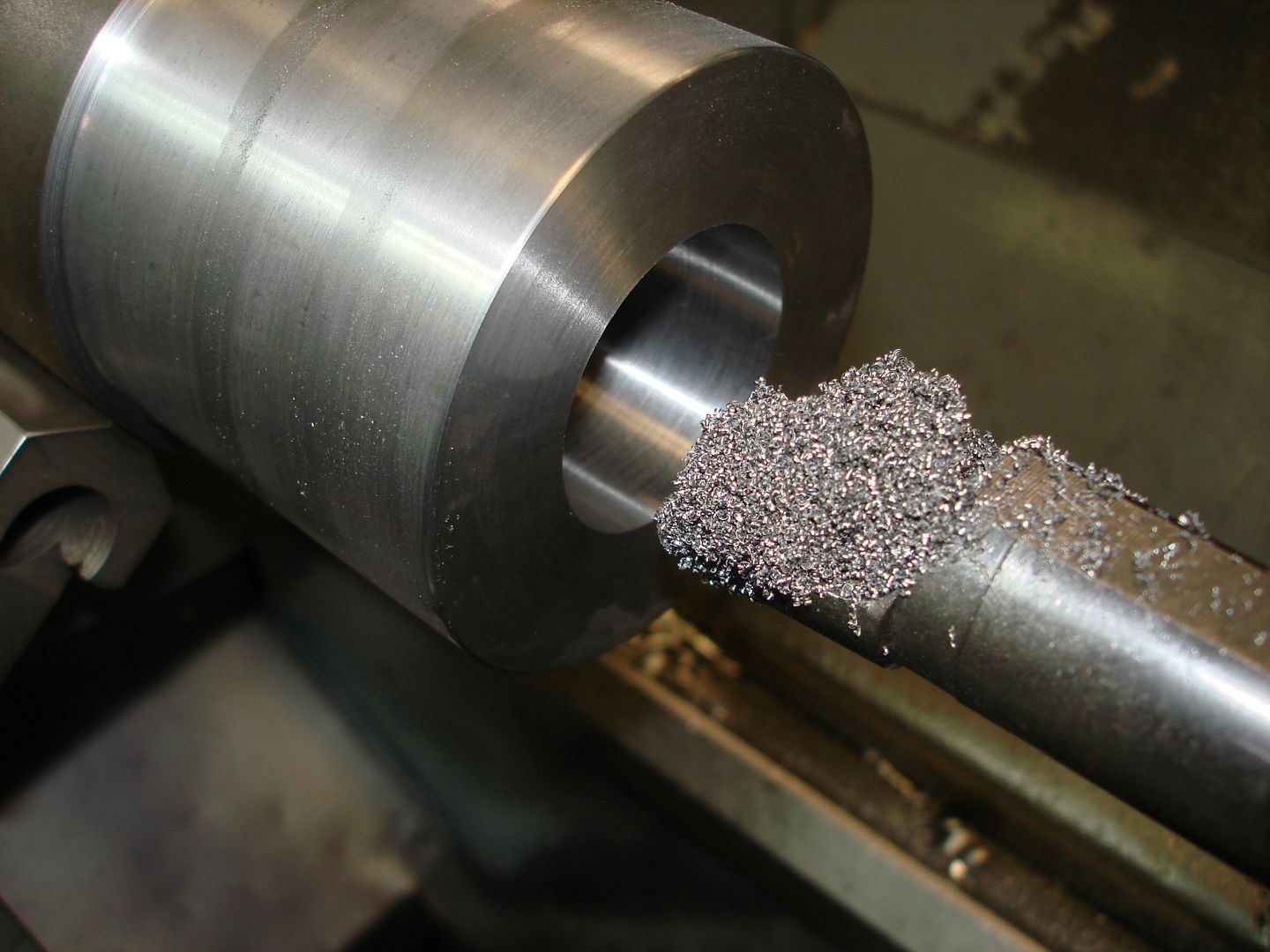
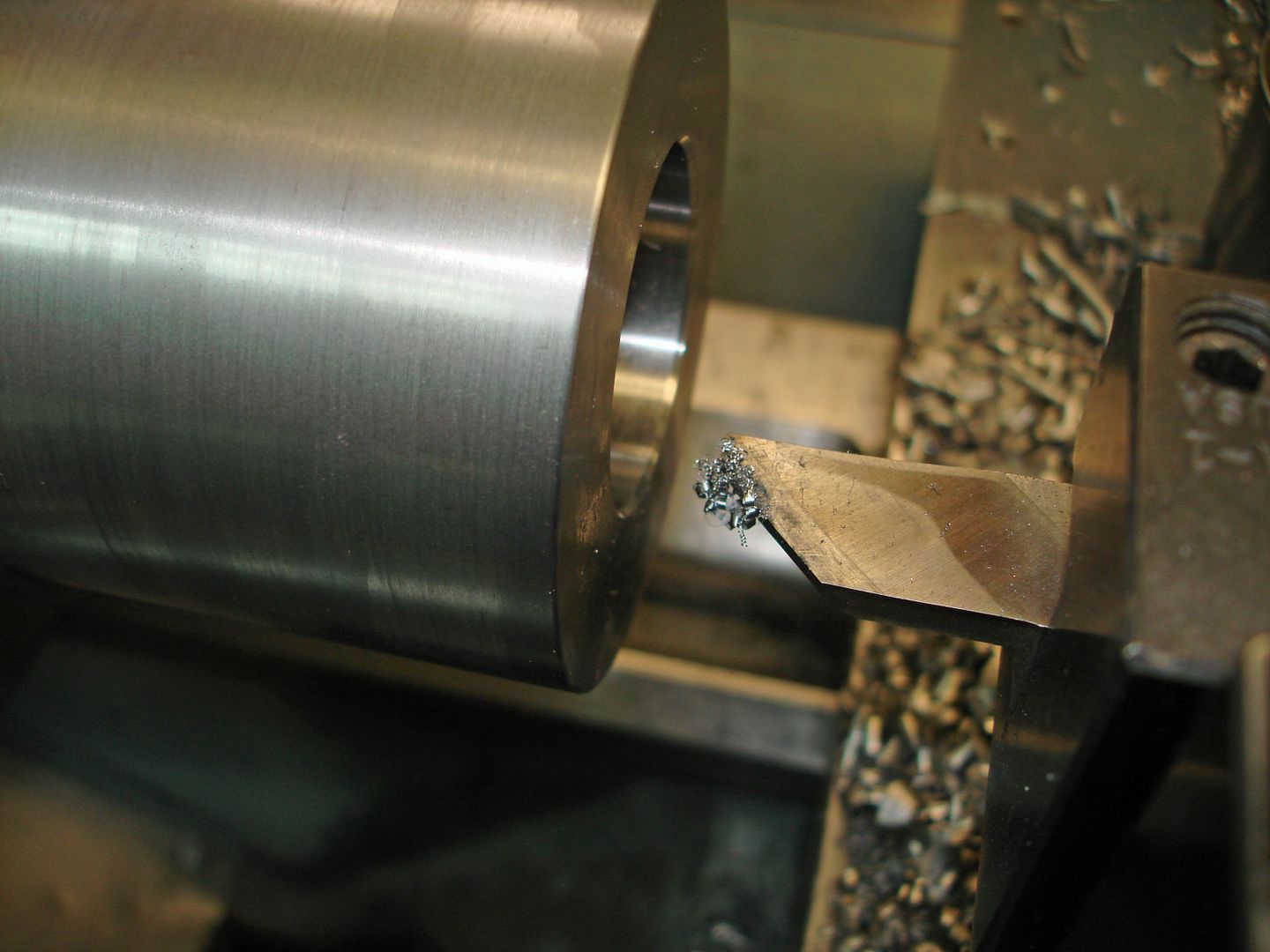
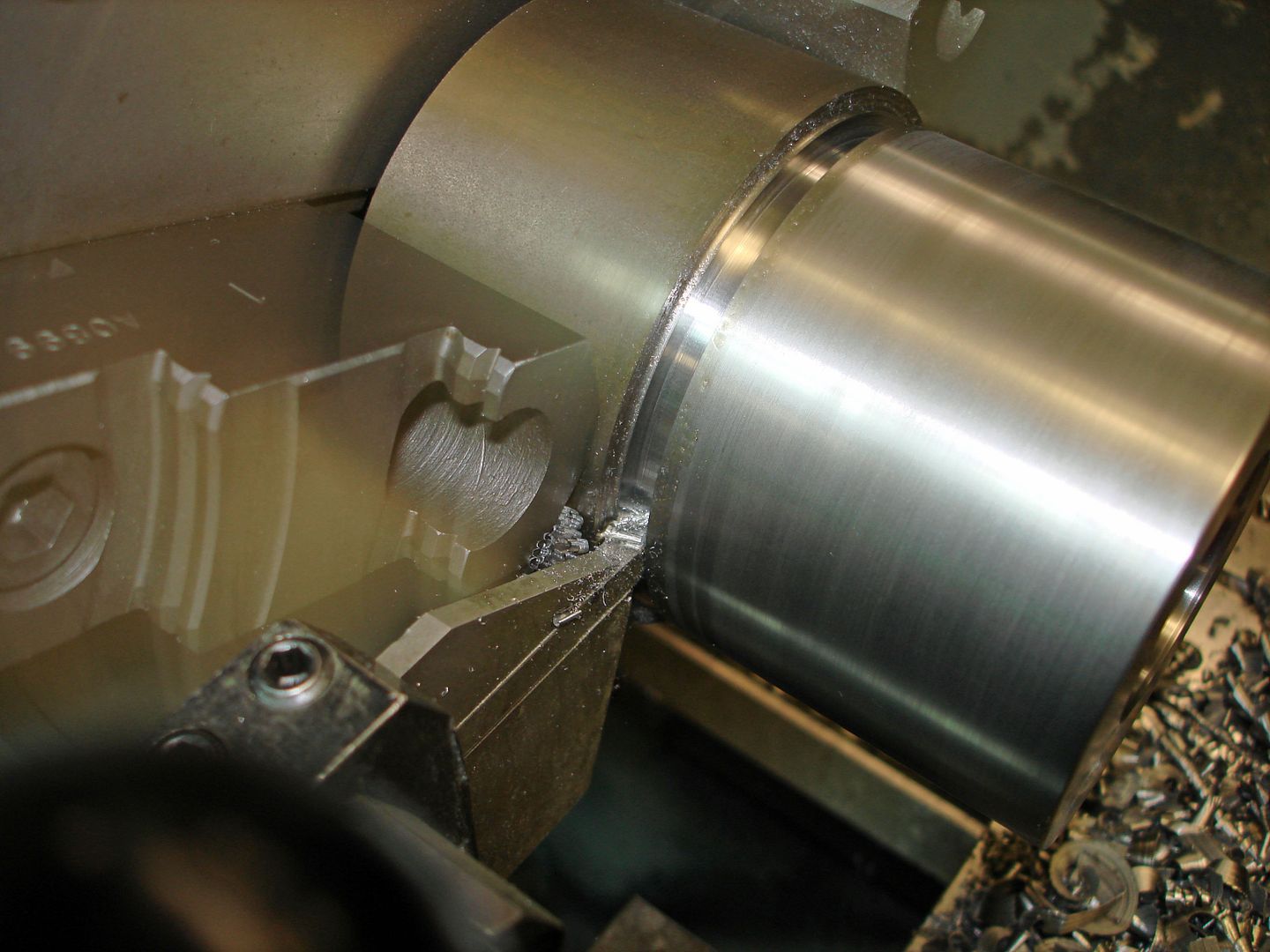
Next operation is at the surface grinder. I set up on the face that was done with the bore in the first operation and ground the opposite side first. This will insure that I will be perpendicular to the bore. Turned cylinder over and finished the overall length.
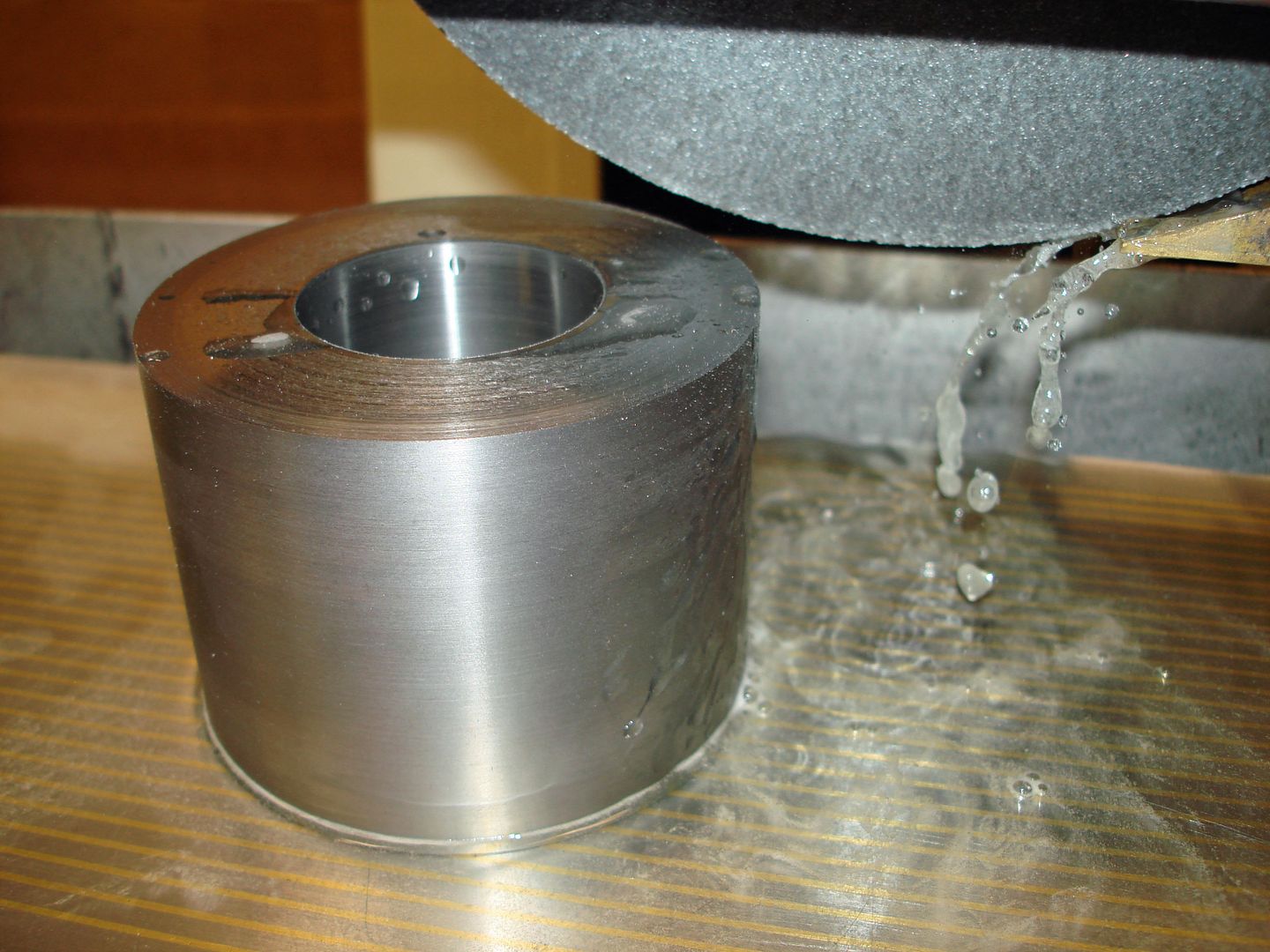
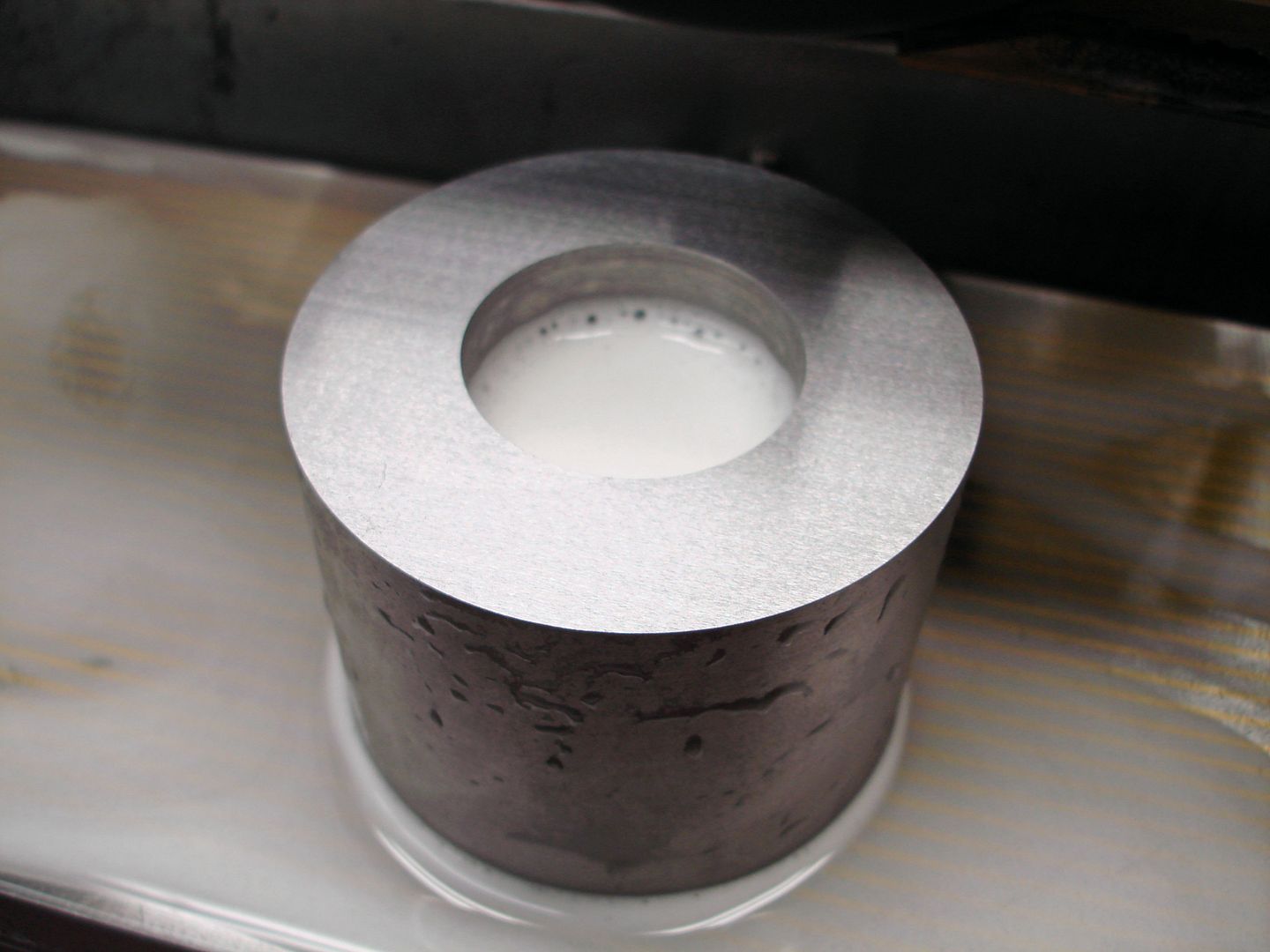
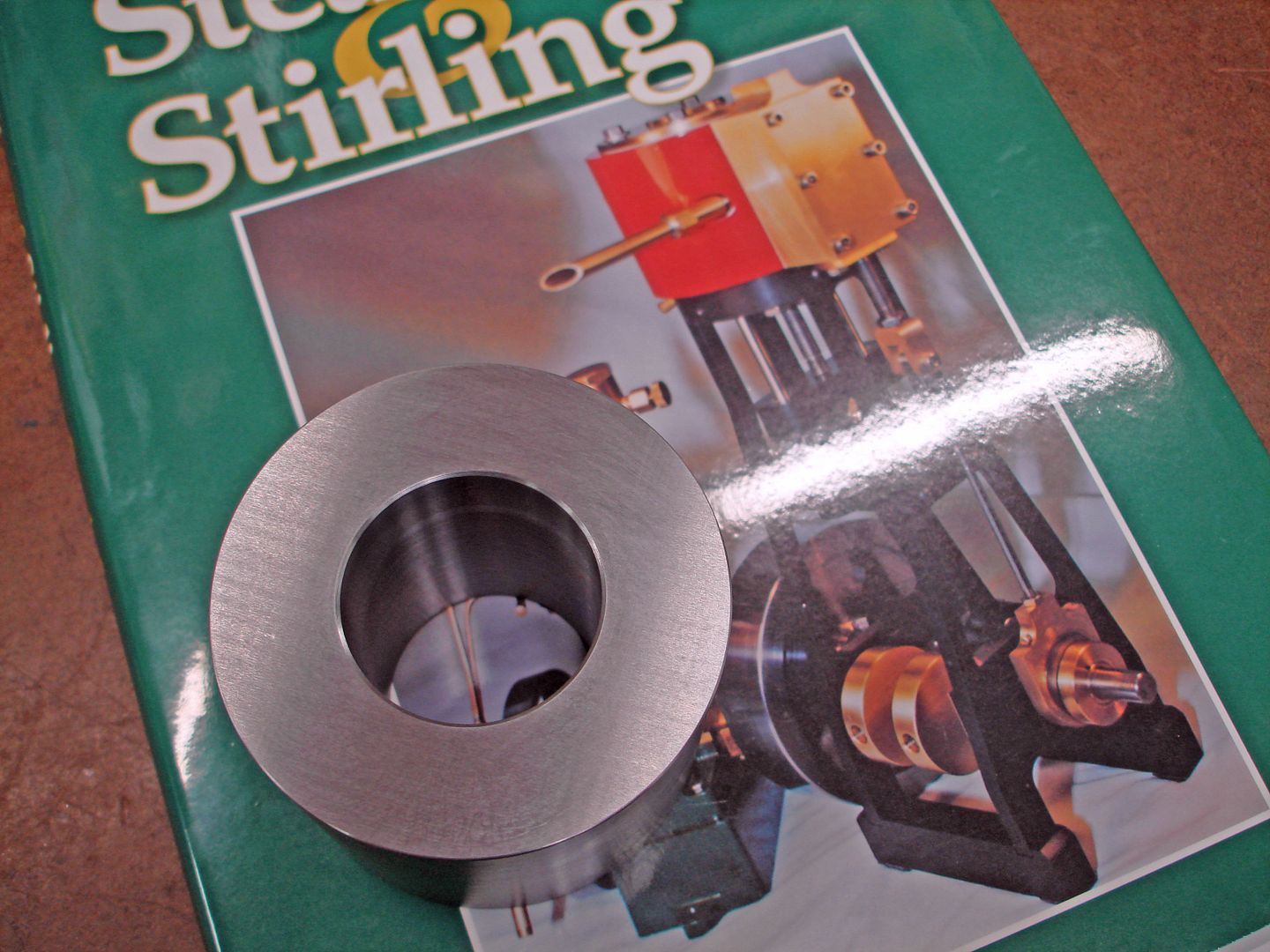
More build to come ......