- Joined
- Jun 4, 2008
- Messages
- 3,285
- Reaction score
- 630
After a 4-day weekend offroading the Jeep and 3 more days doing various maintenance work, I finally had an afternoon in the shop to get back to the engine.
First I finished all of the remaining drilling on the 4 headers (I will need to remake the 5th). Then I put one of them together completely along with the cylinder. Here's a looksee:
Originally I was going to leave the valve cover thicker than the plans, as I had made them from .25" thick brass plate. However, I needed to attach them with the shortest screws, so the options were to machine them thinner or cut the counterbores deeper. FWIW, I milled the counterbores with a 3/16" endmill; the plans show using a 1/8" endmill, but since the head of the screw is larger than that milling the bores is more complicated/tedious.
Some of the brass plungers were a bit too large to fit the holes, even though I measured them at .125" and the holes were reamed with a .126" reamer. Once they're machined they are a PITA to hold and polish down to size (I used a needlenose plier). So a recommended alternative would be to make the heads first and test for fit on the lathe before parting off and machining the heads.
Next step is to clean up the interiors of the cam housing and crankcase, plus part off the crankcase and make some pistons. Then it will be time for a trial assembly. I also need to start thinking of a mount design.
It doesn't sound that easy to me. The dimensions of the crankcase allow space for only 5, so a 9 cylinder model needs smaller cylinders or a larger crankcase. If you are good with cad/cam software then I suppose getting the correct dimensions would be doable.
If you made two 5-cylinder engines and connected them back to back with a common crankshaft then most of the dimensions would remain the same. However, I don't think that would be as attractive as the piston rods and cams would then be hidden from view. Unless the crankcases were made of lucite. ;D
First I finished all of the remaining drilling on the 4 headers (I will need to remake the 5th). Then I put one of them together completely along with the cylinder. Here's a looksee:
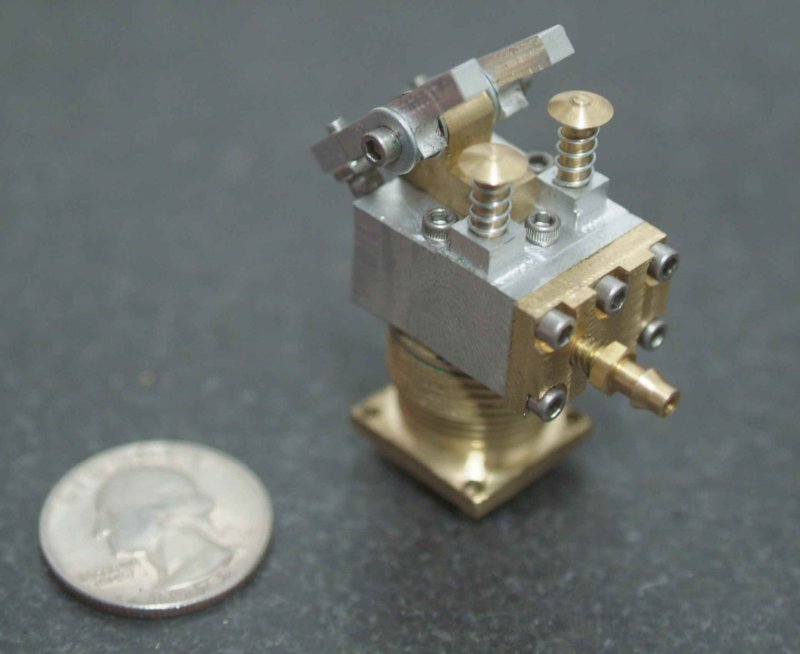
Originally I was going to leave the valve cover thicker than the plans, as I had made them from .25" thick brass plate. However, I needed to attach them with the shortest screws, so the options were to machine them thinner or cut the counterbores deeper. FWIW, I milled the counterbores with a 3/16" endmill; the plans show using a 1/8" endmill, but since the head of the screw is larger than that milling the bores is more complicated/tedious.
Some of the brass plungers were a bit too large to fit the holes, even though I measured them at .125" and the holes were reamed with a .126" reamer. Once they're machined they are a PITA to hold and polish down to size (I used a needlenose plier). So a recommended alternative would be to make the heads first and test for fit on the lathe before parting off and machining the heads.
Next step is to clean up the interiors of the cam housing and crankcase, plus part off the crankcase and make some pistons. Then it will be time for a trial assembly. I also need to start thinking of a mount design.
Now to put the cat amongst the pidgeons. Correct me if I'm wrong, but with the cam proflie being what it is, it looks to be an easy job to add another 4 cylinders and turn it into a 9. If you are making 5 cyclinders , not much extra time for another 4. Once I start will make a 5 and a 9. Geoff
It doesn't sound that easy to me. The dimensions of the crankcase allow space for only 5, so a 9 cylinder model needs smaller cylinders or a larger crankcase. If you are good with cad/cam software then I suppose getting the correct dimensions would be doable.
How about 10 cylinders...
If you made two 5-cylinder engines and connected them back to back with a common crankshaft then most of the dimensions would remain the same. However, I don't think that would be as attractive as the piston rods and cams would then be hidden from view. Unless the crankcases were made of lucite. ;D