- Joined
- Jun 4, 2008
- Messages
- 3,285
- Reaction score
- 630
I decided to make the hose barbs myself using some .25" brass round. Nothing too complicated other than some tedious tool changes on the lathe. Outer barb diameter is 3/16", with the inner diameter 1/8" and the air passage 1/16". I then drilled the mounting holes in the manifold cover, reamed oversize, and fixed the barbs with red loctite. The inlet barb I just cut from a store-bought connector and loctited to the body of the manifold.
With the loctite cured overnight, I assembled to the mount and crankcase.
Then it was time to connect some platic tubing.
I gave the moving parts a dose of oil and hooked up the air. Unfortunately things went less well from there. It turns out that the inside seal between the manifold cover and body isn't airtight, and all the air is exiting there rather than going to the cylinders. So my plan is to make a gasket from oiled kraft paper, as shown on a recent thread.
As I was disassembling the manifold from the engine, I noticed that it wasn't screwed tight. So now it seems that the mounting screws are several threads too long, meaning that the cover was not cinched down tightly to the body. Rather than cut the screws down, I'm still going to make the gasket first.
While everything was assembled, I did a few minutes run-in with the electric drill, and the mechanism doses seem to be turning with less force. I may attach it to the mill spindle and let it turn at low speed for a longer period while the gasket making gets underway.
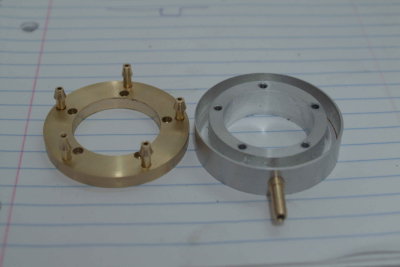
With the loctite cured overnight, I assembled to the mount and crankcase.
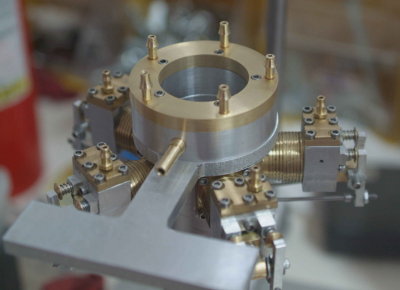
Then it was time to connect some platic tubing.
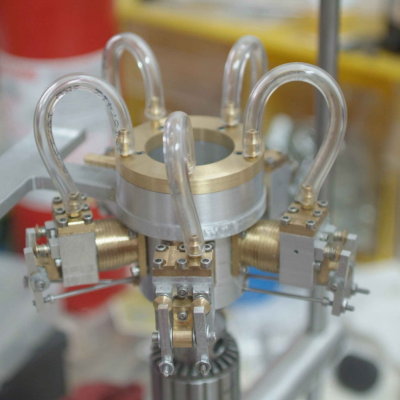
I gave the moving parts a dose of oil and hooked up the air. Unfortunately things went less well from there. It turns out that the inside seal between the manifold cover and body isn't airtight, and all the air is exiting there rather than going to the cylinders. So my plan is to make a gasket from oiled kraft paper, as shown on a recent thread.
As I was disassembling the manifold from the engine, I noticed that it wasn't screwed tight. So now it seems that the mounting screws are several threads too long, meaning that the cover was not cinched down tightly to the body. Rather than cut the screws down, I'm still going to make the gasket first.
While everything was assembled, I did a few minutes run-in with the electric drill, and the mechanism doses seem to be turning with less force. I may attach it to the mill spindle and let it turn at low speed for a longer period while the gasket making gets underway.