BobWarfield
Well-Known Member
- Joined
- Dec 27, 2007
- Messages
- 1,151
- Reaction score
- 1
I was taking another gander at the magnificent photos on John Bentley's (The Engine Man) site when I decided to have a go at modeling a similar steam engine. Bentley's engine is loosely based on Stuart Turner's No. 1, so I thought i"d call this design exercise "Bob's No. 1" as well. It's amazing how much time you can spend on one of these and how neat they turn out. I got this far after about 2 hours:
Here are some more views:
As you can see, I've got an interference problem with the con rod at present. I'll have to redesign the standard to clear it. Good thing I could see that in the CAD model, LOL!
This much took me about 2 hours. I'm not sure when I'll finish it. I was feeling kind of inspired and it had been a while since I fired up Rhino3D. I've got a lot else to deal with at the moment, but it was a fun couple of hours. I reckon I'm probably a good 12-16 hours of work from really finishing.
If I do get the drawings finished, they'll make a nice CNC project for me.
Hope you enjoyed!
Cheers,
BW
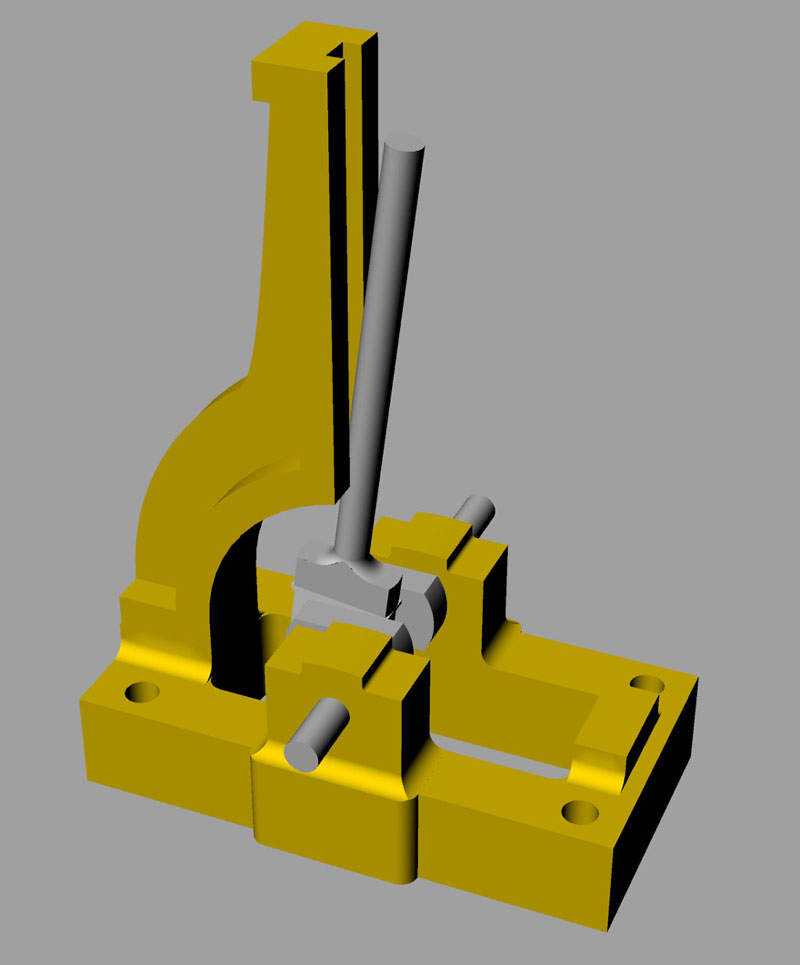
Here are some more views:
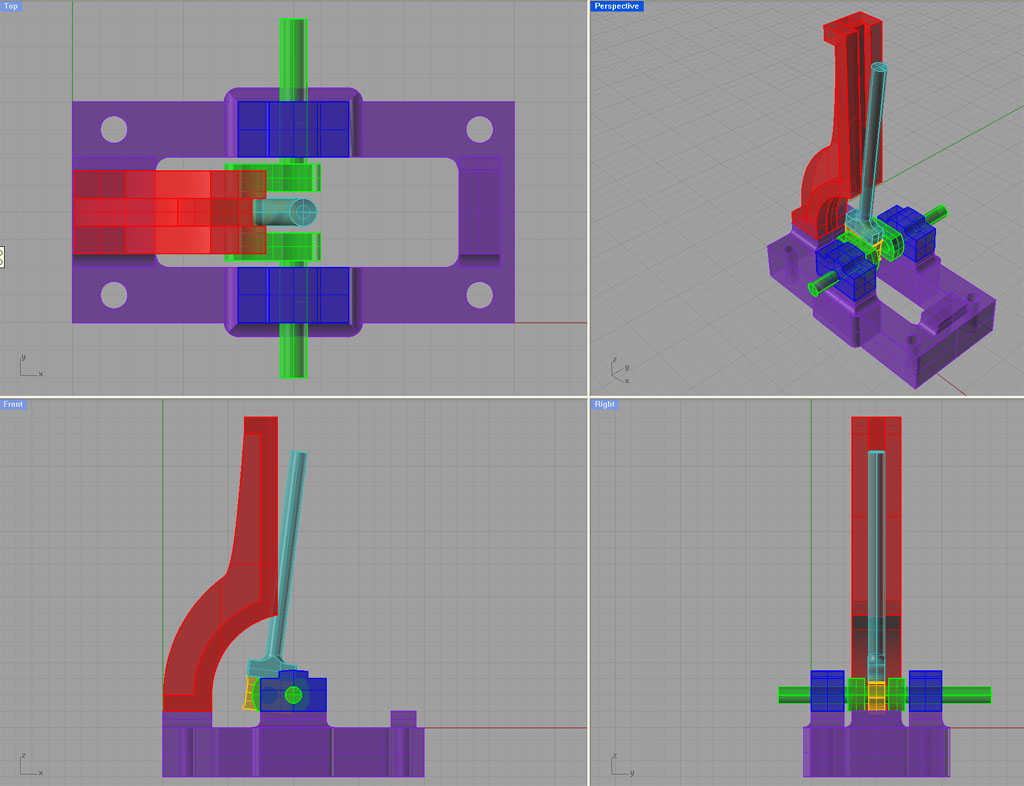
As you can see, I've got an interference problem with the con rod at present. I'll have to redesign the standard to clear it. Good thing I could see that in the CAD model, LOL!
This much took me about 2 hours. I'm not sure when I'll finish it. I was feeling kind of inspired and it had been a while since I fired up Rhino3D. I've got a lot else to deal with at the moment, but it was a fun couple of hours. I reckon I'm probably a good 12-16 hours of work from really finishing.
If I do get the drawings finished, they'll make a nice CNC project for me.
Hope you enjoyed!
Cheers,
BW