I had a very exhausting morning.--Oh, that's a horrible pun--I made the exhaust pipe and flange this morning. I should be making valves, but I need a break from machining things. The temperature outside is almost 60 degrees F and the glacier in my front yard is almost gone. I think I deserve a coffee from Tim Hortons, maybe even risk a big sugary donut. If I still had my hot-rod this would be the day for its first spring ride. Maybe a good dose of sugar and a drive around town will restore my creativity and I'll do the valves later today. ---Brian
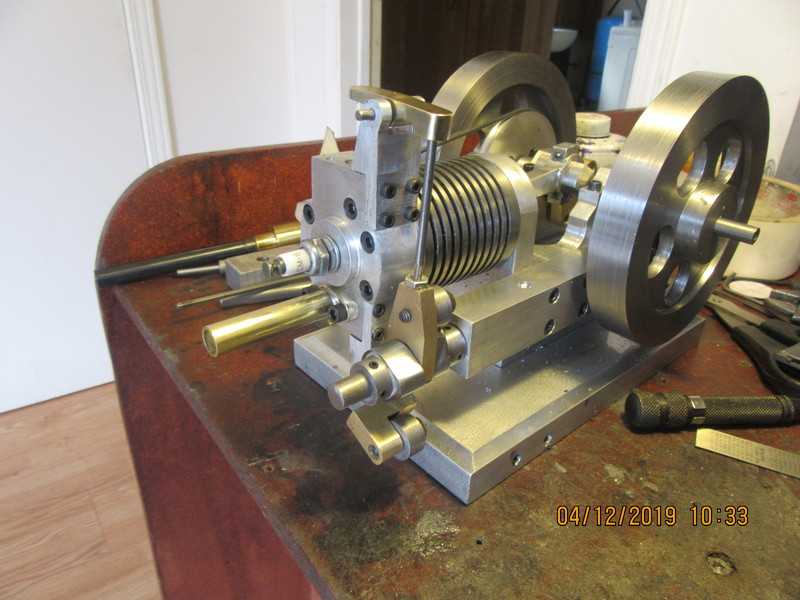