arnoldb
Well-Known Member
- Joined
- Apr 8, 2009
- Messages
- 1,792
- Reaction score
- 12
One of the items on my "to build" list is tailstock die holders. 99% of the time when I need to use a threading die, it is in the lathe, so it is worthwhile making life easier ;D
I decided to go the route of making a separate holder for each of my frequently-used dies; this will save a lot of effort changing dies, and being a lazy person by nature, some work up front is in order. This means I need to make holders for 2, 3, 4, 5, 6 and 10mm dies; these I use the most. My 3 to 6mm dies all use exactly the same holder, so there will be 4 identical ones, and then the other 2 for the 2 and 10mm dies
I have about 5 meters of 32mm hot rolled steel - very nasty stuff to machine, but it's on hand and should do.
First up, I cut 2x460mm sections off the length of HRS; these are the longest I can easily machine in my lathe:
These were then center-marked at one end, and I used my electric hand drill to drill center holes for tailstock support.
I very rarely use power feed on my lathe, as it's a pain to set up, but I wasn't about to manually turn both these down to get rid of the scale, so I set up the Myford's fine-feed gears, and let it do it's own thing:
The first owner of the lathe broke one of the teeth off the internal jaws of the 3-jaw chuck, and this stock is at maximum clamping range for it; not wanting more broken teeth, I used the external jaws.
A close-up of the cut - in action... When I descale, I try and get rid of all the scale and rust in a single pass, with a deepish undercut; it's kinder to the HSS toolbit. In this case, I'm taking a 0.5mm (0.02") cut:
Some cleaned up bar - the short bits are from the original chuck end; I cleaned the bars as far as possible, then sawed off the "unclean" ends with a cleaned bit left on each, and just chucked those on the cleaned ends and took the scale off:
Having lots of cleaned stock, and a VERY dirty lathe contaminated with scale & rust, I spent 2 hours to thoroughly clean & service the lathe, then made the first die holder. It's not finished, as all the holding screw holes still need to be done, as well as some knurling on the raised bit I left for that purpose. For now, I'll use the die holders on a piece of 12mm silver steel just clamped in my tailstock chuck, as the tailstock is very well aligned. Later on, I'll make a dedicated tailstock adapter - if needed:
Hopefully the knurling wheels I ordered will arrive this week - (I need to make a knurling tool as well :
) - need to finish these tools so I can get on with the IDRIS!
Regards, Arnold
I decided to go the route of making a separate holder for each of my frequently-used dies; this will save a lot of effort changing dies, and being a lazy person by nature, some work up front is in order. This means I need to make holders for 2, 3, 4, 5, 6 and 10mm dies; these I use the most. My 3 to 6mm dies all use exactly the same holder, so there will be 4 identical ones, and then the other 2 for the 2 and 10mm dies
I have about 5 meters of 32mm hot rolled steel - very nasty stuff to machine, but it's on hand and should do.
First up, I cut 2x460mm sections off the length of HRS; these are the longest I can easily machine in my lathe:
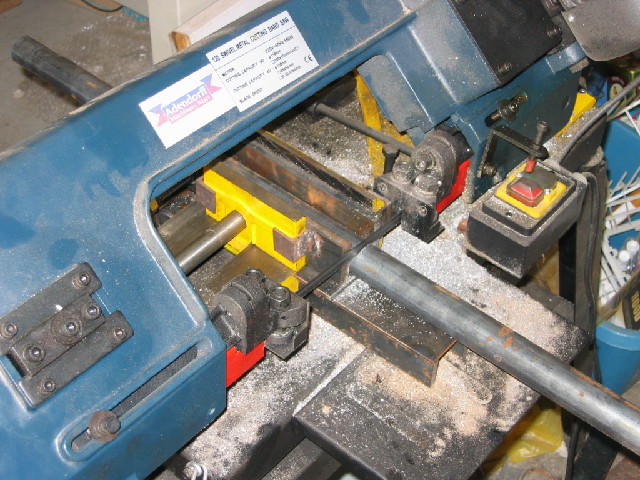
These were then center-marked at one end, and I used my electric hand drill to drill center holes for tailstock support.
I very rarely use power feed on my lathe, as it's a pain to set up, but I wasn't about to manually turn both these down to get rid of the scale, so I set up the Myford's fine-feed gears, and let it do it's own thing:
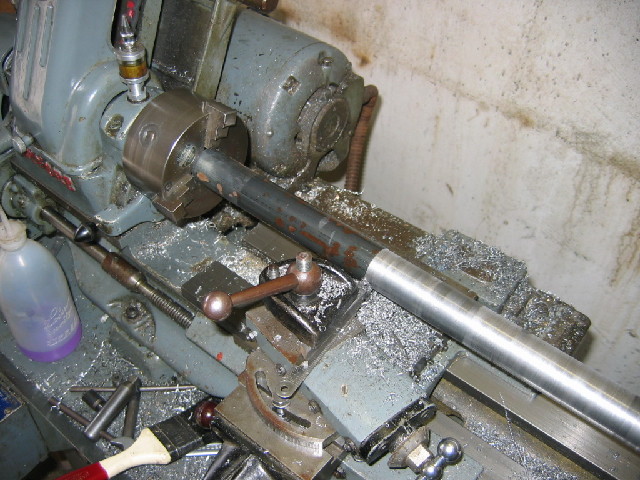
The first owner of the lathe broke one of the teeth off the internal jaws of the 3-jaw chuck, and this stock is at maximum clamping range for it; not wanting more broken teeth, I used the external jaws.
A close-up of the cut - in action... When I descale, I try and get rid of all the scale and rust in a single pass, with a deepish undercut; it's kinder to the HSS toolbit. In this case, I'm taking a 0.5mm (0.02") cut:
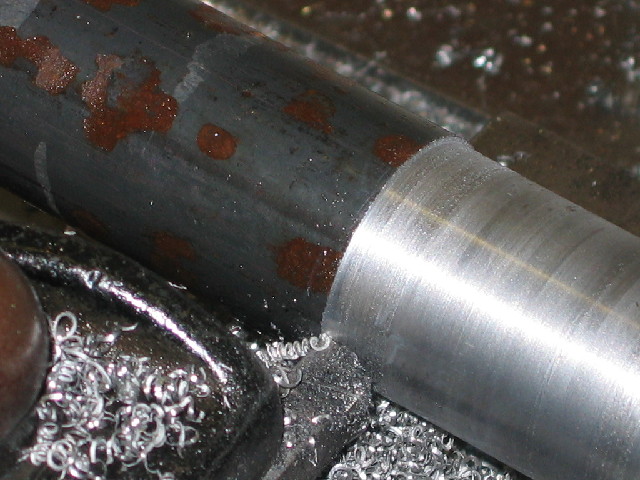
Some cleaned up bar - the short bits are from the original chuck end; I cleaned the bars as far as possible, then sawed off the "unclean" ends with a cleaned bit left on each, and just chucked those on the cleaned ends and took the scale off:
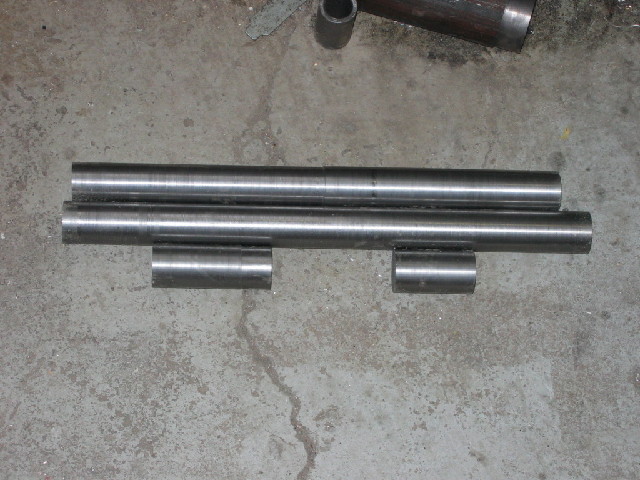
Having lots of cleaned stock, and a VERY dirty lathe contaminated with scale & rust, I spent 2 hours to thoroughly clean & service the lathe, then made the first die holder. It's not finished, as all the holding screw holes still need to be done, as well as some knurling on the raised bit I left for that purpose. For now, I'll use the die holders on a piece of 12mm silver steel just clamped in my tailstock chuck, as the tailstock is very well aligned. Later on, I'll make a dedicated tailstock adapter - if needed:
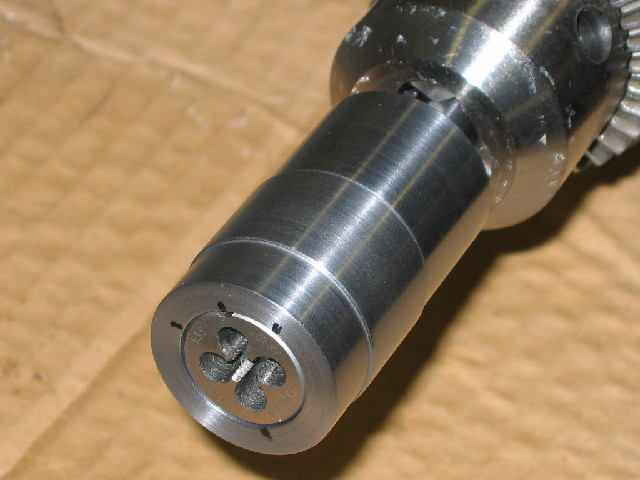
Hopefully the knurling wheels I ordered will arrive this week - (I need to make a knurling tool as well :
Regards, Arnold