Yesterday evening I posted that I had one more fixture to build yet. This shows the simple fixture that I had to make, a piece of 1 1/4" shaft to fit thru the water-jacket, with a flange on one end to allow the four bolts to go thru the flange into the tapped holes in the end of the waterjacket. This let me set it up in my rotary table with chuck attached, and every 2 degrees of rotation I moved the mill table to pass the area I wanted to be rounded under the milling cutter. This of course was a lot of "back and forth", so I set the table stops on the front of the mill table to confine movement to the area I wanted milled.
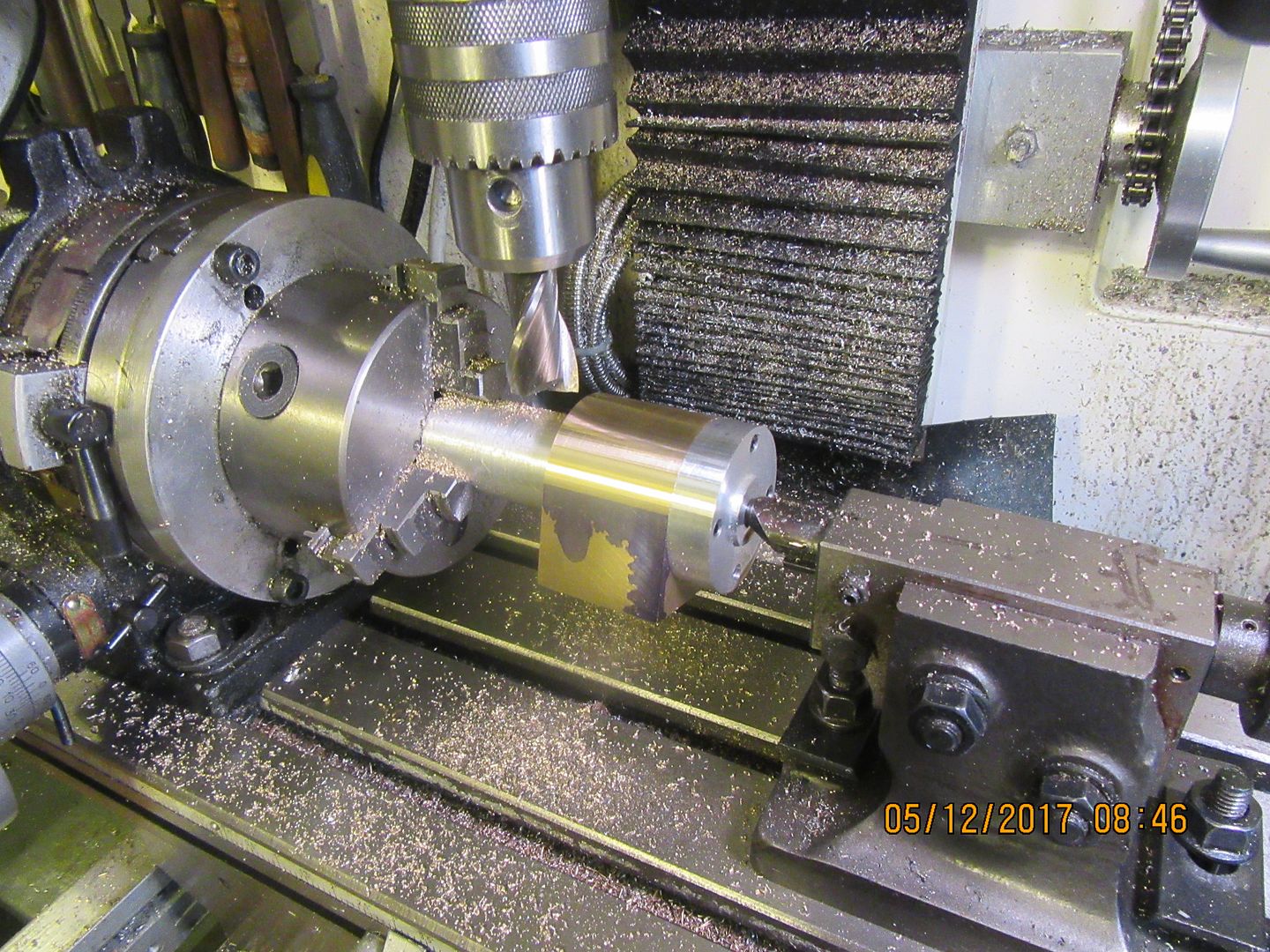