And I do mean different. I want to machine something---but--Something I haven't seen or done before. This is destined to become a water-jacketed engine, 1" bore x 1.125" stroke. I have been casting around for something new to build, and I thought this up last night while fighting off my insomnia. A couple of hours spent on the CAD system this evening just to see if it could be done, and yes, it can. There will probably be many redesigns and changes along the way, but basically this is the overall framework I will stick to.
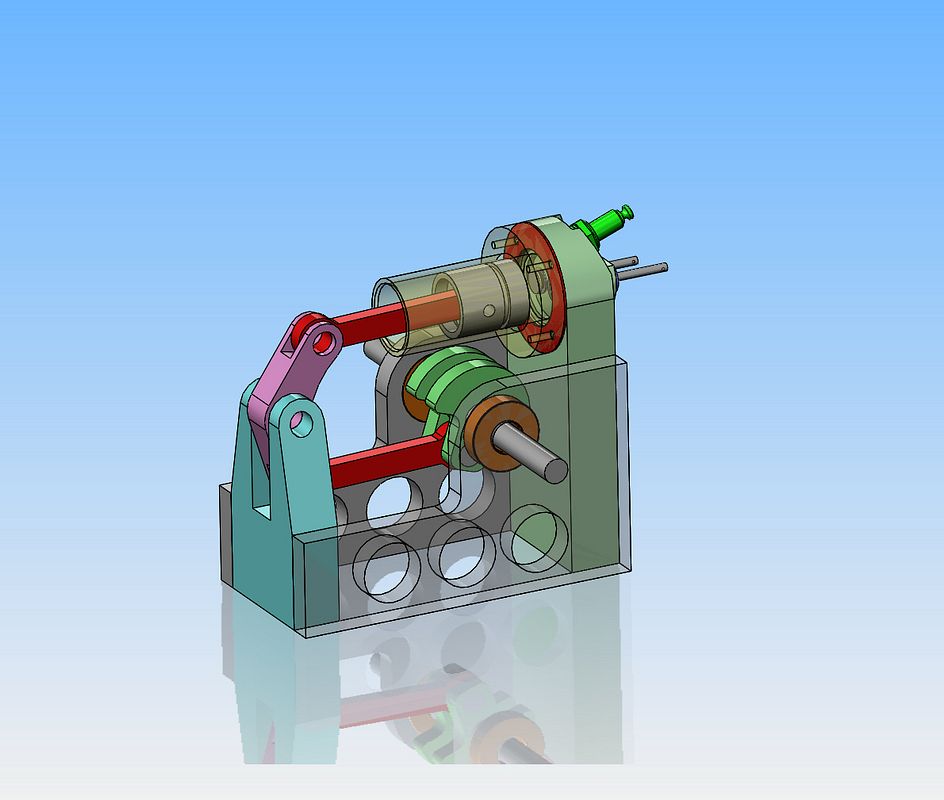