One valve down, and one to go. Both intake and exhaust are the same. The stem on these valves are almost ridiculously long, at 1.537", but once they are set into place in the cylinder head they look about right. The actual guided part of the valve in the valve cage is quite long. I turn these valves down to about 0.128" in 3 stages to keep from having a lot of deflection to deal with. The hardest part of the entire valve is to keep from turning the stem undersize. The last 0.003" or so, I work down to size (0.125") using 220 grit carborundum paper.
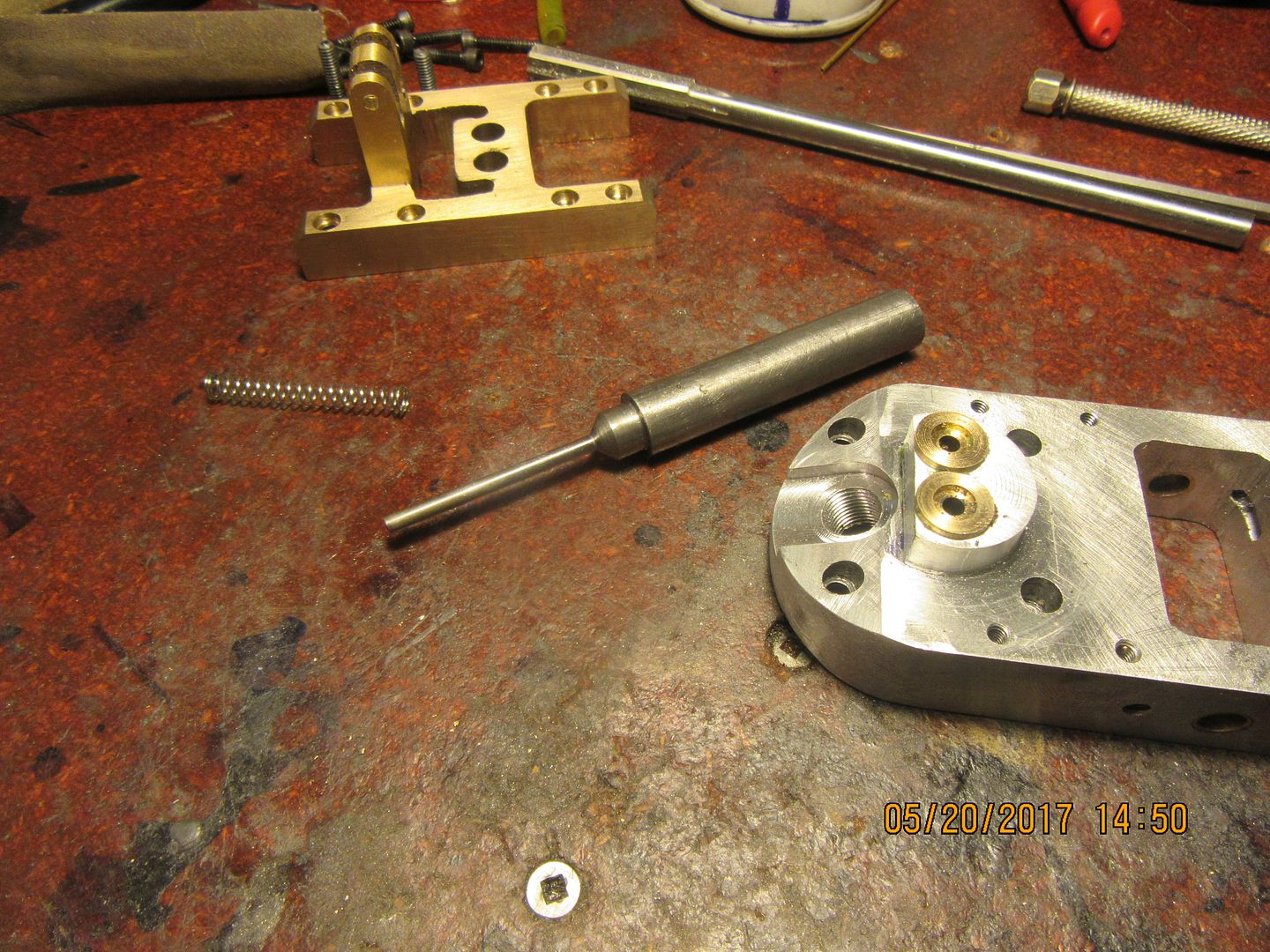