- Joined
- Feb 17, 2008
- Messages
- 2,326
- Reaction score
- 440
About 10 days ago I made the first run of a sort of replica version of a PMC IMP. A couple of photos of it on the test stand and a short video of it's second run were documented at:
http://www.homemodelenginemachinist.com/index.php?topic=4338.0
I promised a construction series on it and this is the start of that. There will be details left out, mostly because I forgot to put them in. If there is something specific that you would like more information on, just ask. I may not have the answer, but you can ask.
This whole thing started in early November 2008. As I often do, I was peeking around on the ModelEngineNews.org web site and happened across the PMC IMP. Here are a couple of links to information on the IMP from there. If you are interested, do a search on the site and there is more information.
http://modelenginenews.org/cardfile/pmcimp.html
http://modelenginenews.org/ed.2005.09.html#3
In addition, Ron had prepared CAD drawing by reverse engineering an IMP, and those drawings appear in the "members only" area of the site and are included in the DVD that he has prepared for members of the site. The drawings have a few minor omissions in them, but nothing that would prevent construction. After looking at them for a few days, I sketched up 3 versions of the IMP. On all the versions, Imperial screws were substituted tor the BA screws on the original.
Version 1 is fairly much as the IMP was originally constructed. It is a fair representation of the IMP, but there were quite a few variations of the IMP. As only a few were built, and they were hand built, it is probably fair to say that almost every one was a little bit different.
Version 2 of the IMP is mostly the same as Version 1, except the front and back plates for the crankcase are screwed on, beam mounts added, and the crankcase has a rounded bottom. In addition the cylinder and head are held on by 4 screws instead of 2.
Version 3 is the same as Version 2 except the exhaust and intake positions are reversed, so the engine more resembles the EmBee which the IMP design has as an ancestor.
The common parts of all three versions have been built at the same time. At this point, only Version 2 is complete and running. Versions 1 and 3 have a few parts to go, some being made over using some of the information learned from Version 2.
I am showing this as a "Work in Progress" as Versions 1 and 3 will be completed (I hope) during the life of this thread.
Here is a photo of Version 2. Followed by a photo or the original engine from ModelEngineNews.org so you can see some of the diffenences between Version 1 and version 2.
Gail in NM,USA
http://www.homemodelenginemachinist.com/index.php?topic=4338.0
I promised a construction series on it and this is the start of that. There will be details left out, mostly because I forgot to put them in. If there is something specific that you would like more information on, just ask. I may not have the answer, but you can ask.
This whole thing started in early November 2008. As I often do, I was peeking around on the ModelEngineNews.org web site and happened across the PMC IMP. Here are a couple of links to information on the IMP from there. If you are interested, do a search on the site and there is more information.
http://modelenginenews.org/cardfile/pmcimp.html
http://modelenginenews.org/ed.2005.09.html#3
In addition, Ron had prepared CAD drawing by reverse engineering an IMP, and those drawings appear in the "members only" area of the site and are included in the DVD that he has prepared for members of the site. The drawings have a few minor omissions in them, but nothing that would prevent construction. After looking at them for a few days, I sketched up 3 versions of the IMP. On all the versions, Imperial screws were substituted tor the BA screws on the original.
Version 1 is fairly much as the IMP was originally constructed. It is a fair representation of the IMP, but there were quite a few variations of the IMP. As only a few were built, and they were hand built, it is probably fair to say that almost every one was a little bit different.
Version 2 of the IMP is mostly the same as Version 1, except the front and back plates for the crankcase are screwed on, beam mounts added, and the crankcase has a rounded bottom. In addition the cylinder and head are held on by 4 screws instead of 2.
Version 3 is the same as Version 2 except the exhaust and intake positions are reversed, so the engine more resembles the EmBee which the IMP design has as an ancestor.
The common parts of all three versions have been built at the same time. At this point, only Version 2 is complete and running. Versions 1 and 3 have a few parts to go, some being made over using some of the information learned from Version 2.
I am showing this as a "Work in Progress" as Versions 1 and 3 will be completed (I hope) during the life of this thread.
Here is a photo of Version 2. Followed by a photo or the original engine from ModelEngineNews.org so you can see some of the diffenences between Version 1 and version 2.
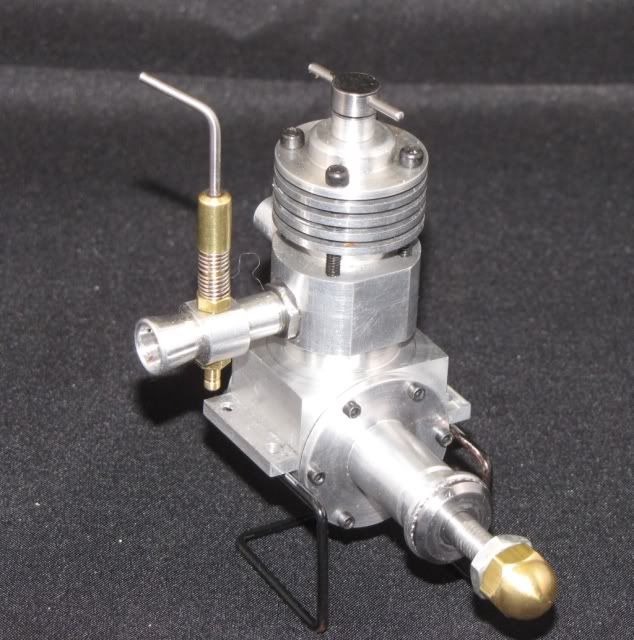
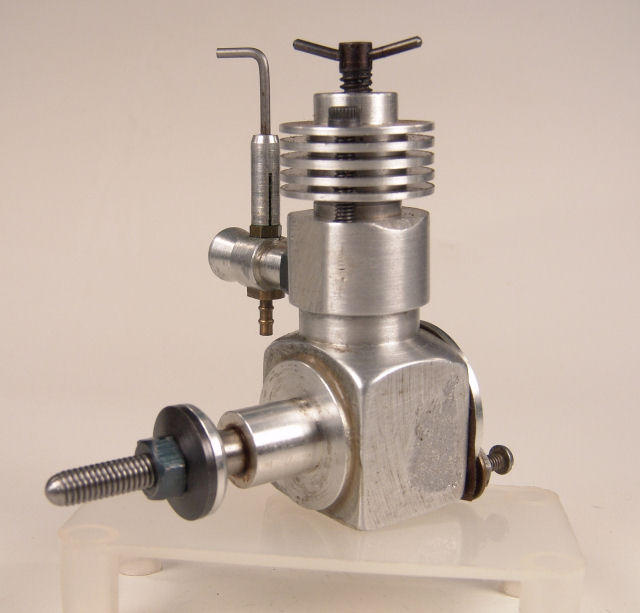
Gail in NM,USA