- Joined
- Mar 3, 2008
- Messages
- 243
- Reaction score
- 20
Here is the first part of my build of the Moriya Stirling Engine, originally designed by Dr.James Senft. I changed a few things alone the way, the biggest was not to build it as a fan but to put on a flywheel instead. It will have a built-in propane burner and a modified Oak box when finished.
Warning! Newbe At Work
Some operations may cause you to scratch your head ;D
I managed to get most of the stock together before starting the project, partially because my in-house stock pile is finally gaining size and taking a proper shopping list to metal guy.
This is standard stuff, boring out the ColdEnd. The problem came about when I tried to cut the fins on the lathe. I did not have enough clearance between the 1 3/4 x 1 3/4 block and the grooving tool to work. I guess there is a lathe mod or trick for this, but I decided to do it on the mill.
Here I am cutting the fins on the mill. I wish now that I could have done this on the lathe, this way involves a lot of passes and rotations, but it turned out OK
More to come.
Warning! Newbe At Work
Some operations may cause you to scratch your head ;D
I managed to get most of the stock together before starting the project, partially because my in-house stock pile is finally gaining size and taking a proper shopping list to metal guy.
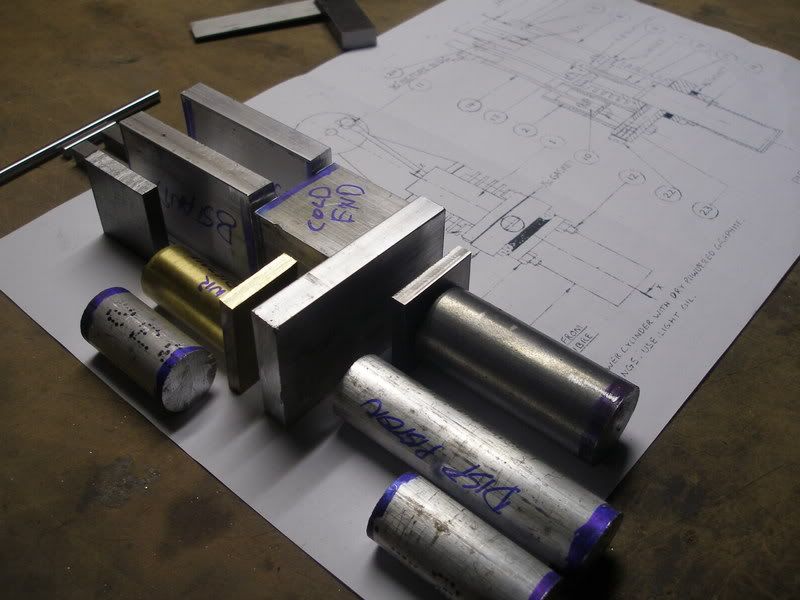
This is standard stuff, boring out the ColdEnd. The problem came about when I tried to cut the fins on the lathe. I did not have enough clearance between the 1 3/4 x 1 3/4 block and the grooving tool to work. I guess there is a lathe mod or trick for this, but I decided to do it on the mill.
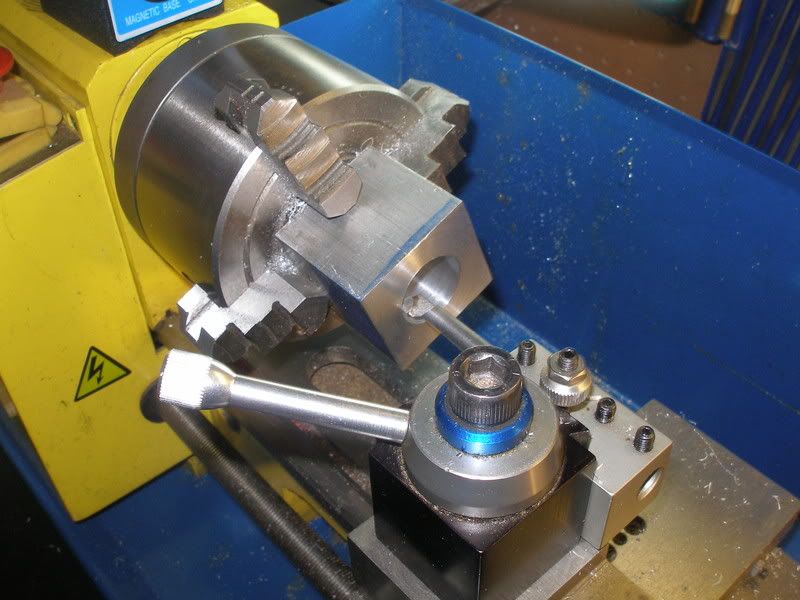
Here I am cutting the fins on the mill. I wish now that I could have done this on the lathe, this way involves a lot of passes and rotations, but it turned out OK
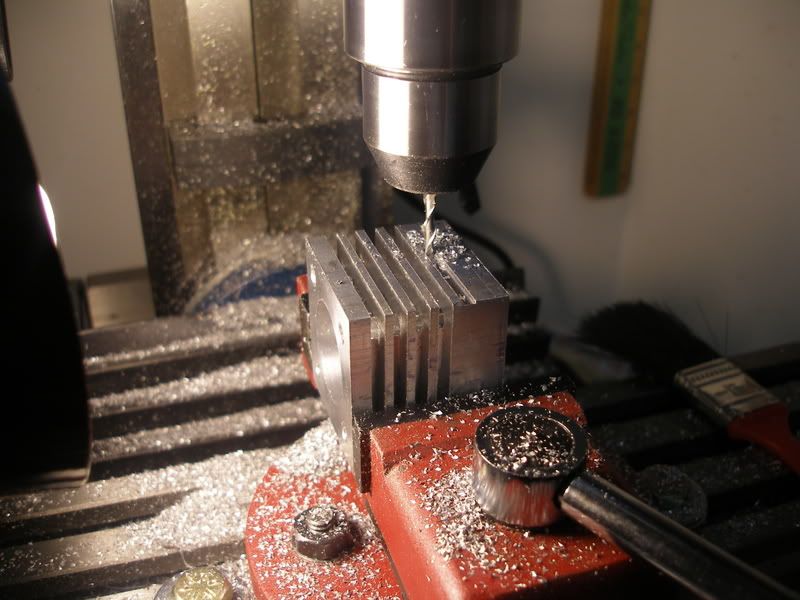
More to come.