I wanted to get a 5/8" reamer, I only need it to ream out the faceplate bore hole in the pattern so couldn't see going and buying one.
In the 6th book of the Gingery series they show you how to make cheap hand reamers.
I have some cold rolled 5/8 left and cut a piece to size, took my time measuring and cutting the angle.
Filed all the cutter makers off, then went to the honing stones. When through the 4 different stones I have, which is probably over kill since I am just going to cut soft wood with it.
Here it is, turn out pretty good.
Went over to my drill press and try to put the newly made 5/8" reamer into my 1/2" chuck. ???
Hmmm it seems I don't have anything to put this into to ream the hole I need. But I have a nicely finished 5/8" reamer
Guess the 5/8" drill bit will have to do.
List of things to buy - 5/8" chuck for drill press.
Oh well, it was fun making it.
John.
In the 6th book of the Gingery series they show you how to make cheap hand reamers.
I have some cold rolled 5/8 left and cut a piece to size, took my time measuring and cutting the angle.
Filed all the cutter makers off, then went to the honing stones. When through the 4 different stones I have, which is probably over kill since I am just going to cut soft wood with it.
Here it is, turn out pretty good.
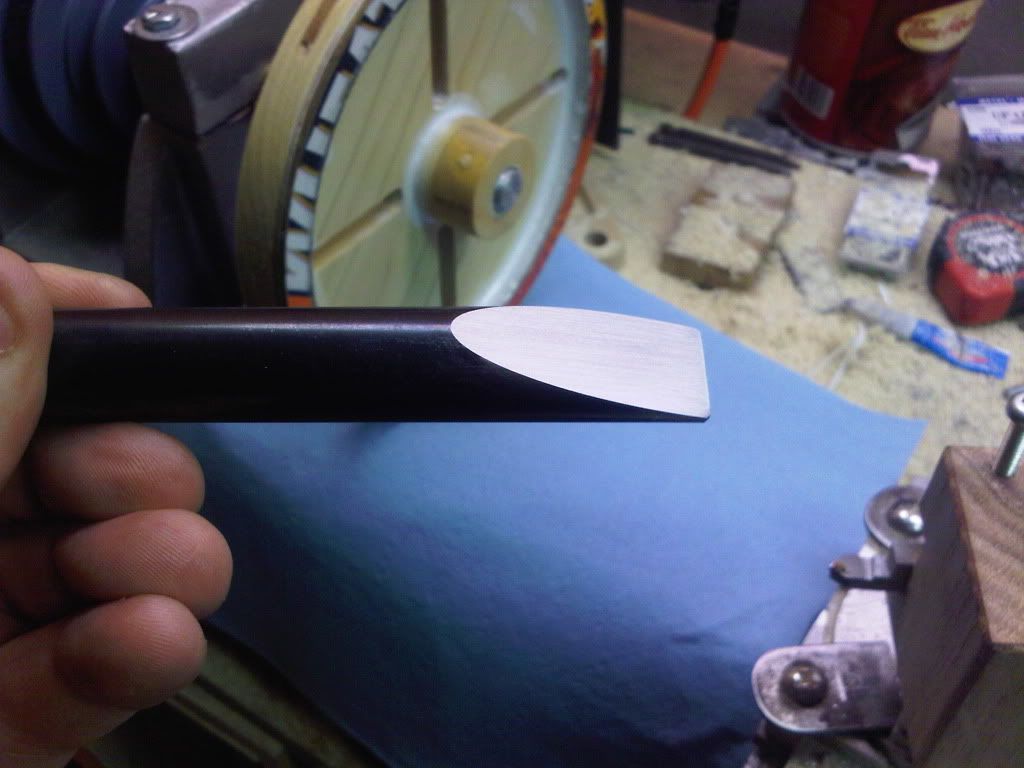
Went over to my drill press and try to put the newly made 5/8" reamer into my 1/2" chuck. ???
Hmmm it seems I don't have anything to put this into to ream the hole I need. But I have a nicely finished 5/8" reamer
Guess the 5/8" drill bit will have to do.
List of things to buy - 5/8" chuck for drill press.
Oh well, it was fun making it.
John.