I have decided to build Elmers #33 mill engine--Kind of. I modelled it as per Elmers drawings yesterday, and although his version is very pretty, there are many things that can be simplified without compromising the way the engine works. My smallest fastener that I "stock" is #5-40 shcs., so the engine has been modified to accomodate them. I am working with a box full of scrap aluminum "shorts" from one of my fabricators, so the plans have been modified to suit the peices I have. My smallest end mill is 1/8" diameter, so again, the plans will be tweaked to work with that. Since I have to create detail drawings to work with, I will post them here as usual in case any of you chaps care to build it too. I hope you follow my build, and I hope we have fun.---brian
View attachment ASSEMBLY-33.PDF
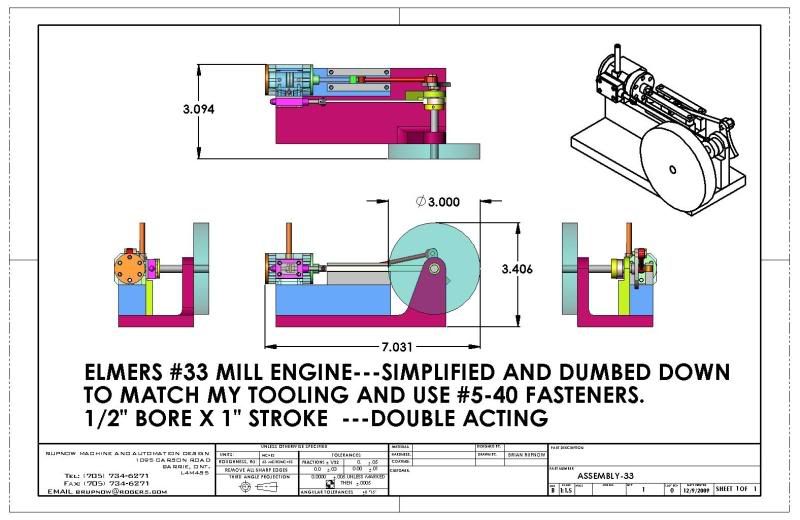
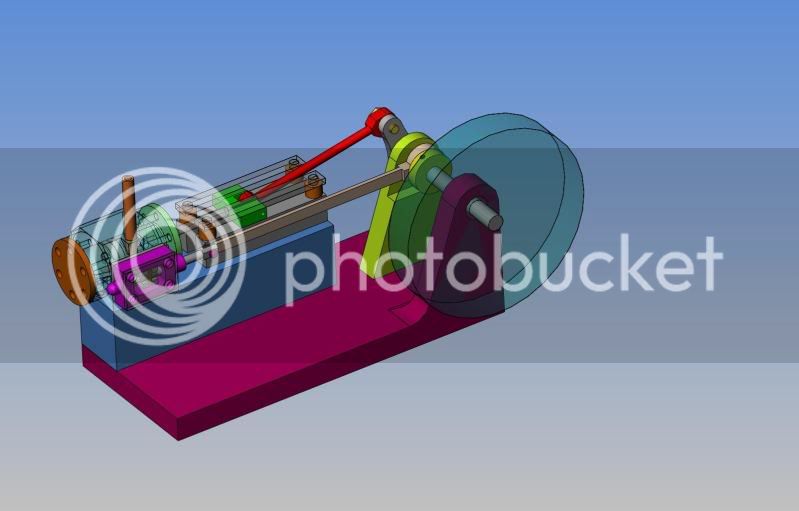
View attachment ASSEMBLY-33.PDF