Since the valve rod pin is shown above I certainly can't pretend it isn't done and go to bed at a reasonable hour, now can I? Nothing to do but carry on.
The parent stock for the valve rod is still in the three jaw, so let's make the pin from a little further on down the same.
Roughed out to final diameter on the pin and head, left long for parting off and cleaning.
Off to the vise to cross drill. As above, the edge finder, my micrometer and a few buttons on the calculator let me find center on the rod.
Might as well skip the math and just use the valve rod to ensure adequate clearance on the hole. Elmer calls for a #70 drill here, but the closest I come with the mini carbides is #74 @ .0225. Still plenty of room for a strand of copper wire, so I'm off to the races.
I learned my lesson above and returned it to the 3-jaw after cross drilling. Note the reference Sharpie mark on the stock. It's tougher to see, but there is also one on the jaw face, made at about the same time. That's close enough for parting off.
Note here that I have also shortened and dressed the end outside the hole. Yes, the lathe was spinning for this shot, but I did back the tool off a few thou to avoid rubbing.
Here I have reversed it in a collet to dress the head. Must have been close on this diameter as well, as it cleared the reamed hole in the valve rod and was a light finger-press fit in the 1/16 collet.
Everything needs a bit of a bath, but here it is, installed with enough room for a thin washer.
Yeah, that's the packing nut screwed into the valve chest. What's another few minutes, since we are on a roll?
The parent stock for the valve rod is still in the three jaw, so let's make the pin from a little further on down the same.
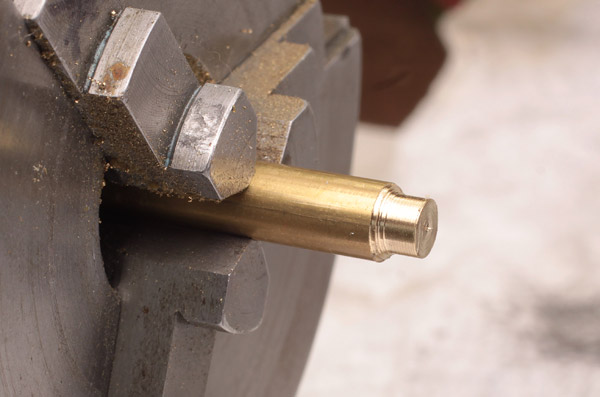
Roughed out to final diameter on the pin and head, left long for parting off and cleaning.
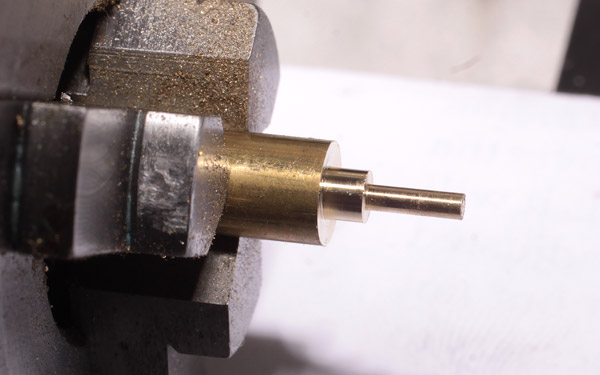
Off to the vise to cross drill. As above, the edge finder, my micrometer and a few buttons on the calculator let me find center on the rod.
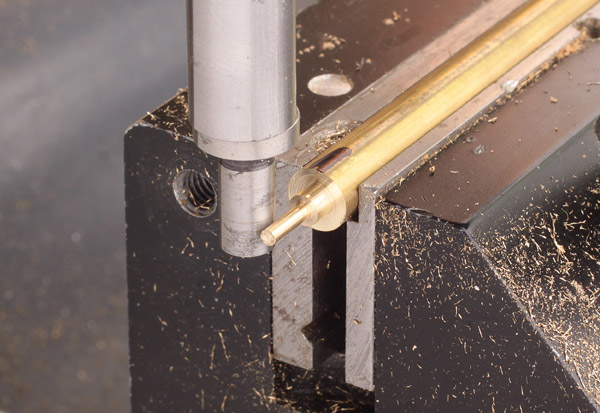
Might as well skip the math and just use the valve rod to ensure adequate clearance on the hole. Elmer calls for a #70 drill here, but the closest I come with the mini carbides is #74 @ .0225. Still plenty of room for a strand of copper wire, so I'm off to the races.
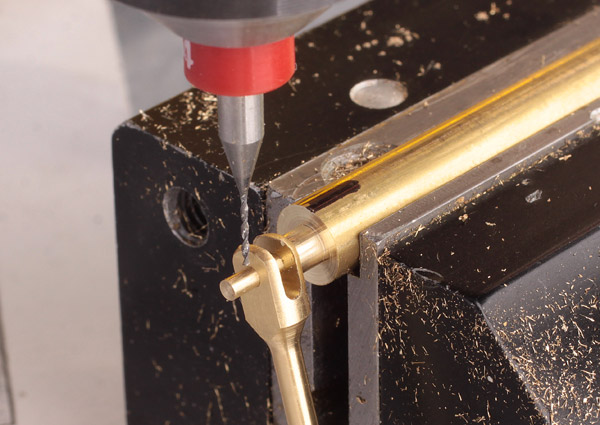
I learned my lesson above and returned it to the 3-jaw after cross drilling. Note the reference Sharpie mark on the stock. It's tougher to see, but there is also one on the jaw face, made at about the same time. That's close enough for parting off.
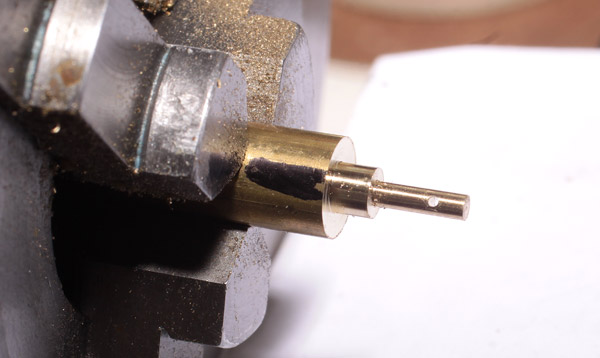
Note here that I have also shortened and dressed the end outside the hole. Yes, the lathe was spinning for this shot, but I did back the tool off a few thou to avoid rubbing.
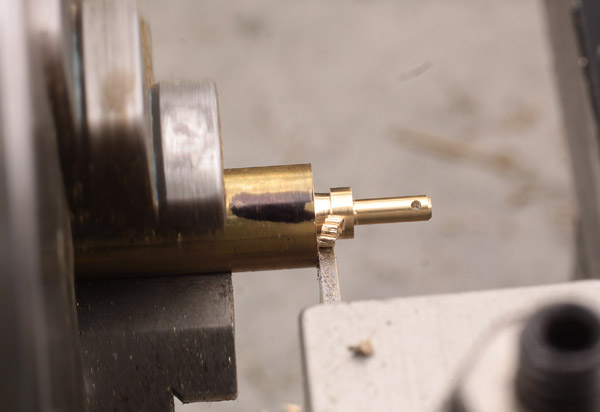
Here I have reversed it in a collet to dress the head. Must have been close on this diameter as well, as it cleared the reamed hole in the valve rod and was a light finger-press fit in the 1/16 collet.
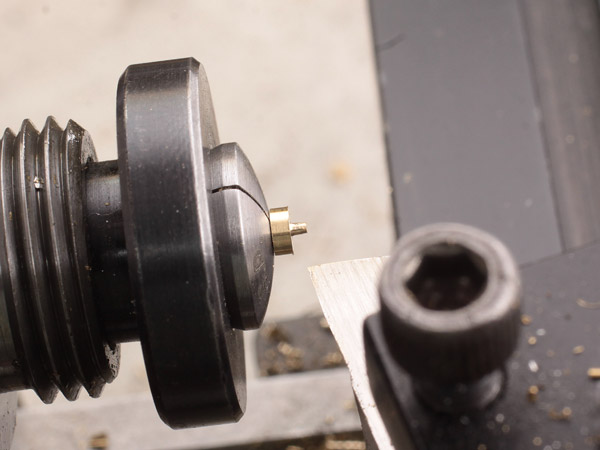
Everything needs a bit of a bath, but here it is, installed with enough room for a thin washer.
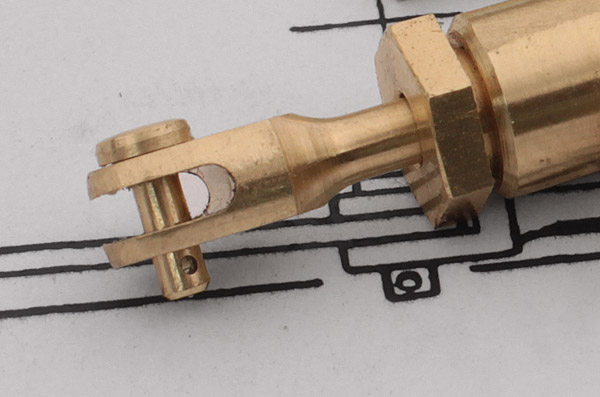
Yeah, that's the packing nut screwed into the valve chest. What's another few minutes, since we are on a roll?