Then I saw all the outer lines in the bandsaw and trim "close to the line". Then set it up in the mill and mill "To the line". Then to do the inner cuts---scratch head for a minute, then drill and tap a piece of 1/2" x 3/4" flatbar on the same hole centers as I used to bolt the two frames together---then use longer bolts to bolt the tower pieces (still together) to the flatbar so I can hold it all in the mill vice. Put in a 1/4" milling cutter and start connecting the holes---Just have to be carefull and not cut the wrong thing and have everything fly apart.
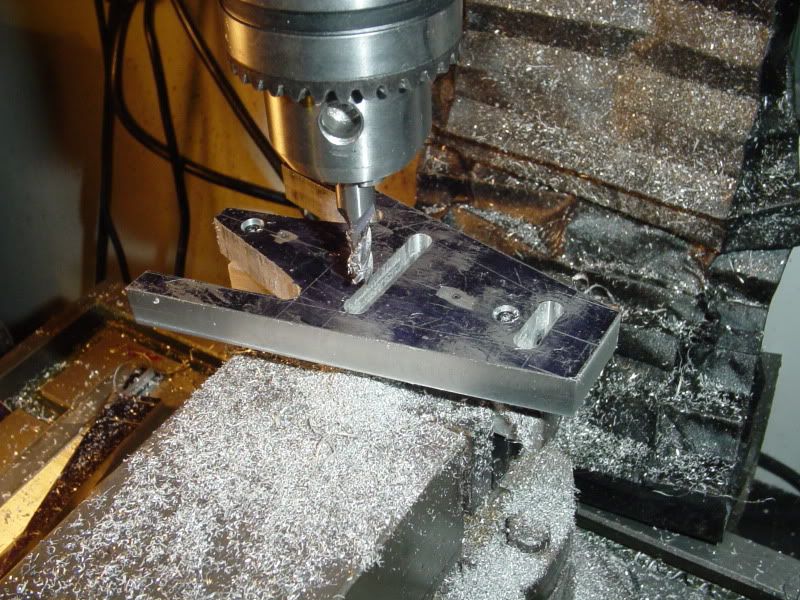
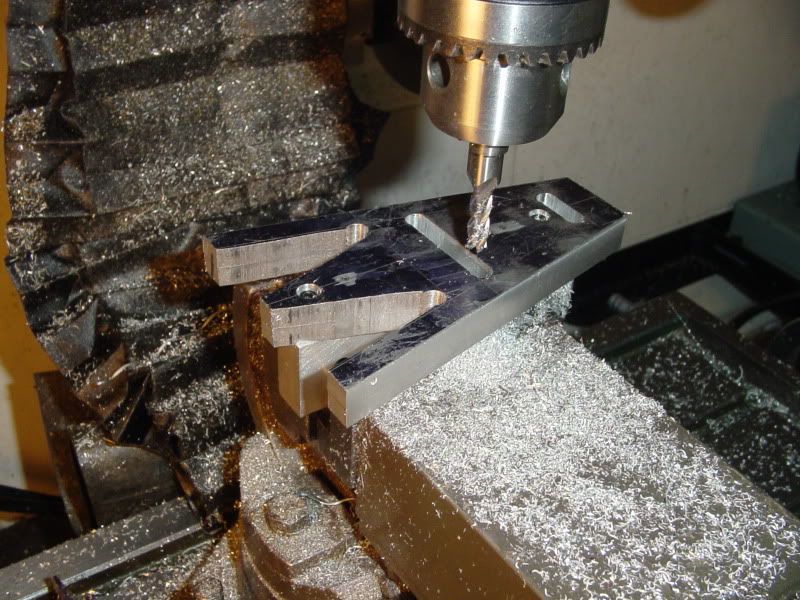