This is something I forgot to show in my detail drawing.--A couple of grooves to hold lubricating oil, about 0.015 deep by 45 degrees on the cylinder. (in this picture I have parted the square end off and clamped the round part in the 3 jaw chuck.)
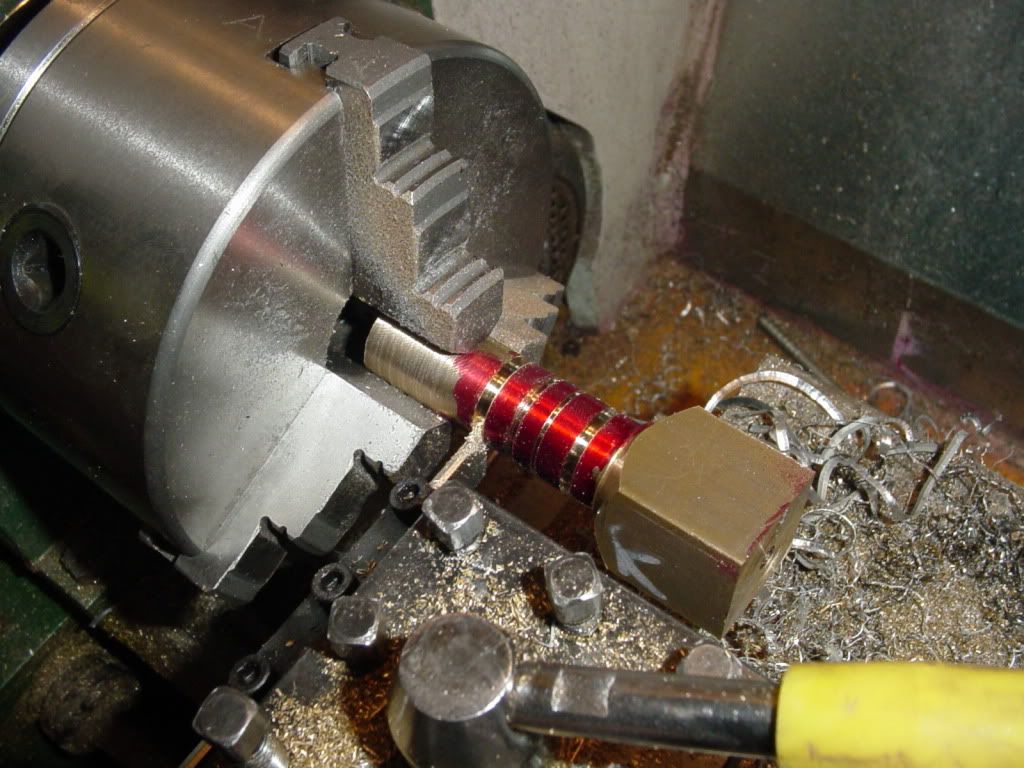
Brian Rupnow said:(You can't see it but there is a center gripped in the 3 jaw chuck.)
Zee--I wondered if anybody would pick up on that!!! Yes, when I centerdrilled the end which sets closest to the chuck I put a 0.125 hole in one corner and stuck a peice of 1/8" x 1.5" stl. rod in it. One of the chuck jaws riding against the side of the pin turned the part. That is my secret trick for avoiding having to change to and use my 4 jaw chuck.)zeeprogrammer said:Hi Brian,
Excuse my question...very little experience...but what is turning the part? Is there a pin or something on the end of the part that the chuck jaw is against?
Thanks.
kvom said:Did you deburr the edges of the crankcase? They look awfully sharp to me.
Brian Rupnow said:That is my secret trick for avoiding having to change to and use my 4 jaw chuck.)
Enter your email address to join: