This might end up being a long thread. I started it over on the "Break Room" under the heading "Hit and Miss Steam Engine???"
http://www.homemodelenginemachinist.com/index.php?topic=5150.0
Then drew up mechanical details and posted them in the download section.
http://www.homemodelenginemachinist.com/index.php?action=tpmod;dl
And today I started whittling out parts.
http://www.homemodelenginemachinist.com/index.php?topic=5150.0
Then drew up mechanical details and posted them in the download section.
http://www.homemodelenginemachinist.com/index.php?action=tpmod;dl
And today I started whittling out parts.
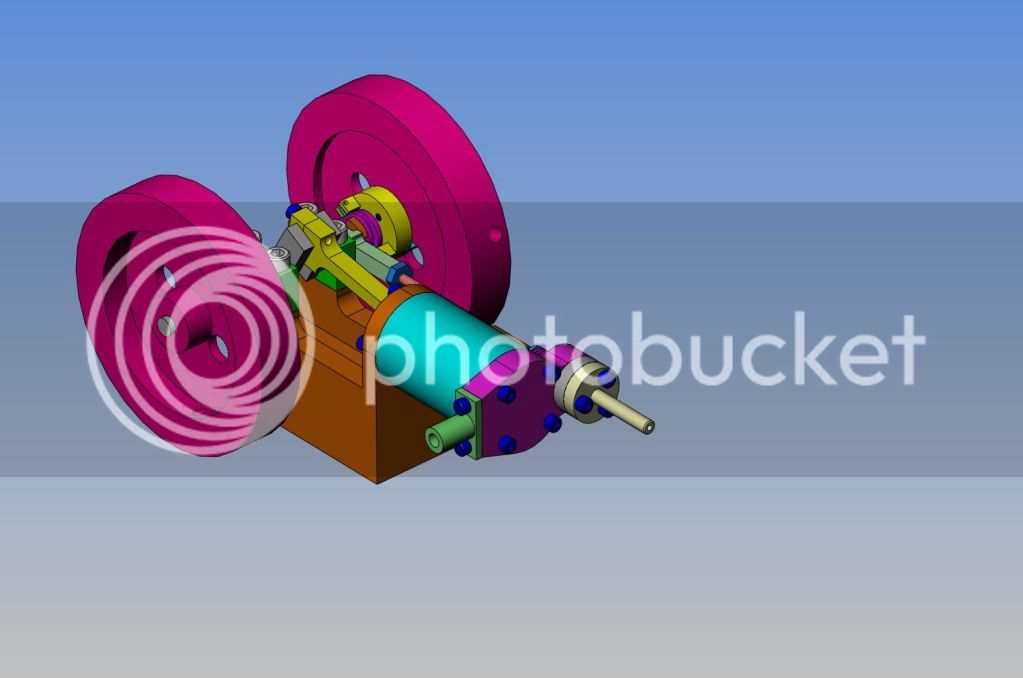