And this is what it looked like before I set up to turn the ends. The 1/4" bolt has a nut and washer on the far side, and is tightened down to keep the slot in the center from collapsing when I turn between centers.
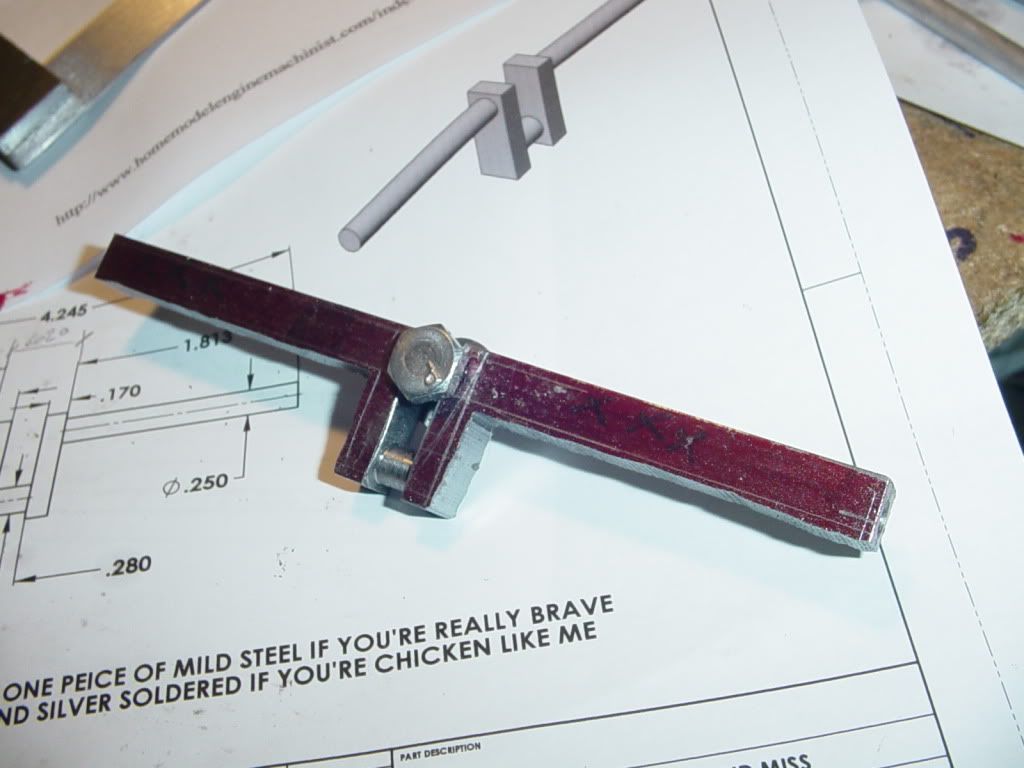
kustomkb said:Nice work Brian!
Back with a bang eh?
putputman said:Hey Brian, been there - done that!!
That's where your skills & talent kick in. The recovery plan.
I sure as hell with some of the people running this country had some of your skills.
Whoops, maybe I started something. :wall:
Enter your email address to join: