hammers-n-nails
Well-Known Member
- Joined
- Mar 22, 2009
- Messages
- 206
- Reaction score
- 0
well boys here is the begining of our next project, the title says it all. this engine is going to be a copy of and engine that my dads uncle, my great uncle, has had for many years. im sorry i dont have a very good picture of the original ill try to remember to get one next time i go over there. some of the general specs for the model are overall length about 8feet, boiler shell 15'' diameter 30-35 sqft heating surface, rear wheels 32.5'' dia, cylinder size 4.5"diax5"stroke, approximate weight 3000-3500lbs, estimated top speed 1.2mph.
right now dads welding up the boiler and im working on the front axle and pedistal
heres the pics and comments
best pic i have of the original
the boiler mocked-up
the boiler partially assembled. we whent for a lapped seam boiler for astetic purposes, it will take a considerably longer time to build though
my progress on the pedistal, sorry i didnt get a pic of the pieces before i welded them together, on the end you cant see is a ball that will rest in a socket in the axle to allow it to pivot and tilt side-to-side, i cheated a little bit and used a 2" trailer towing ball. there isnt anything in the pic for scale but the overall length is about 8" and the disk at the bottom is 6 1/2" dia
im having a problem with it and that is that i would like to have a nice 1/4" or so radius where the gussets meet the center pipe, they are welded together obviously and i cant get the die grinder to give a smooth enough finish to satisfy me and the flap disk on the angle grinder cant reach most of it so i was wondering if any of you had any trick ways to accomplish this, i have a cylindrical flap drum for the die grinder but its 1"dia (the smallest i can find) is too big so that doesnt work. any ideas would be great.
the pedistall and front axle on the original
right now dads welding up the boiler and im working on the front axle and pedistal
heres the pics and comments
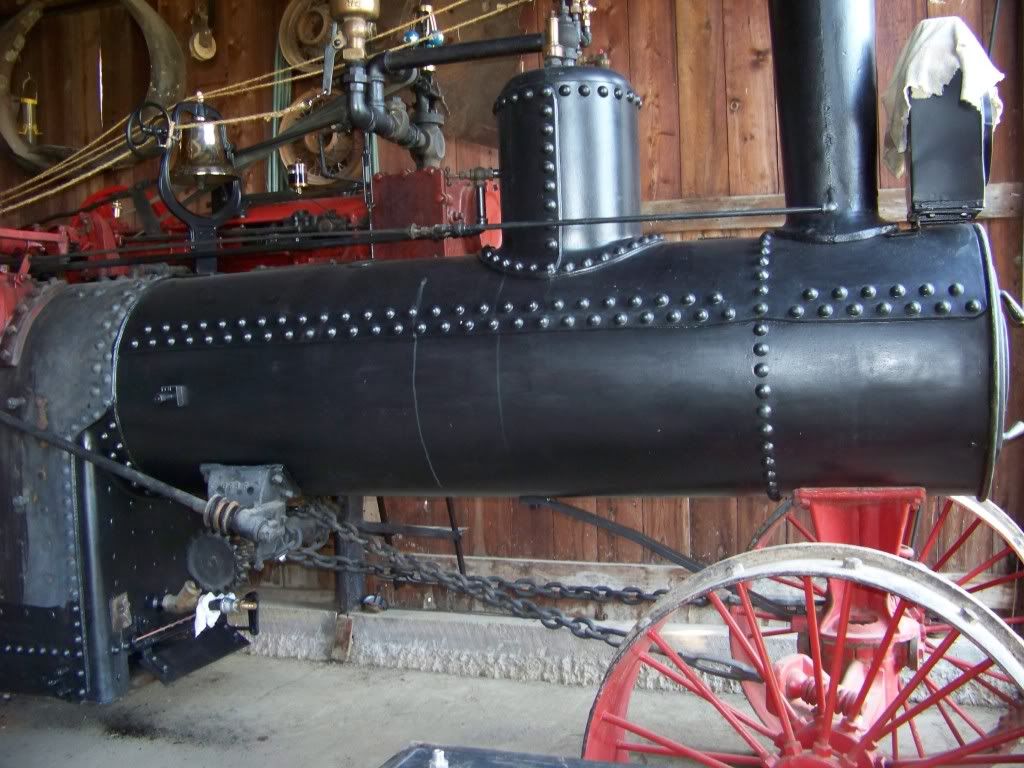
best pic i have of the original
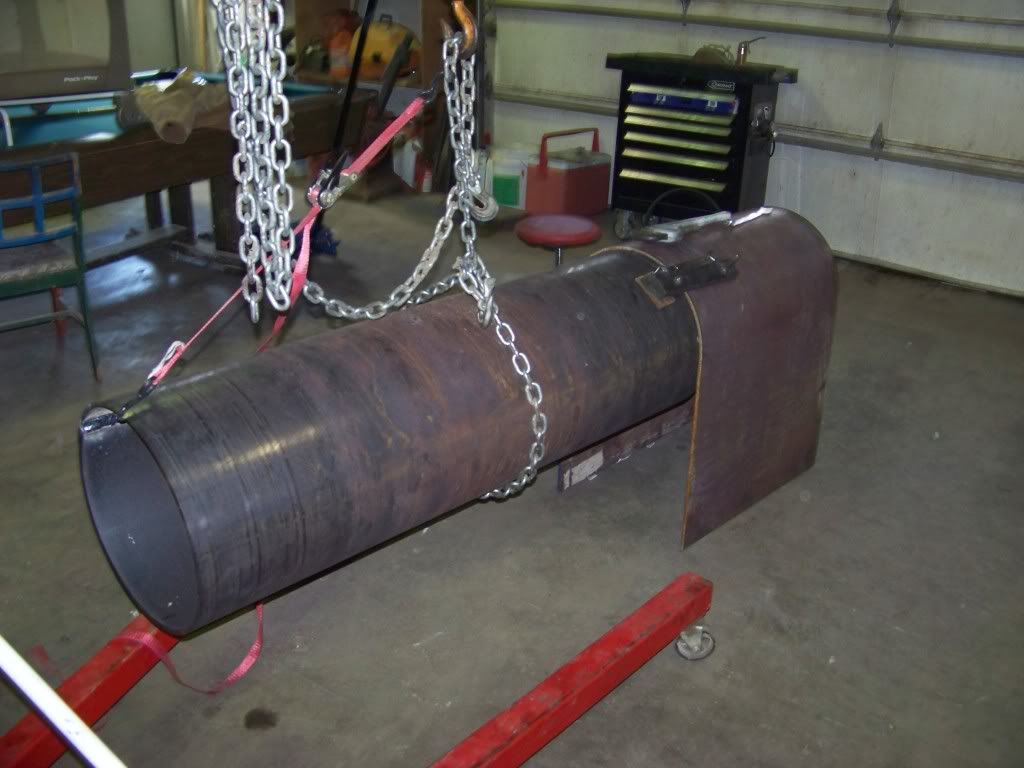
the boiler mocked-up
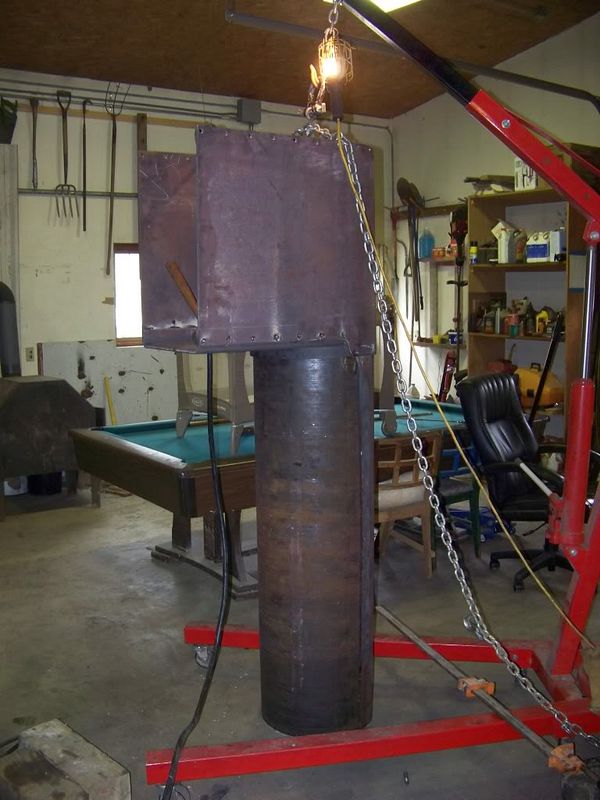
the boiler partially assembled. we whent for a lapped seam boiler for astetic purposes, it will take a considerably longer time to build though
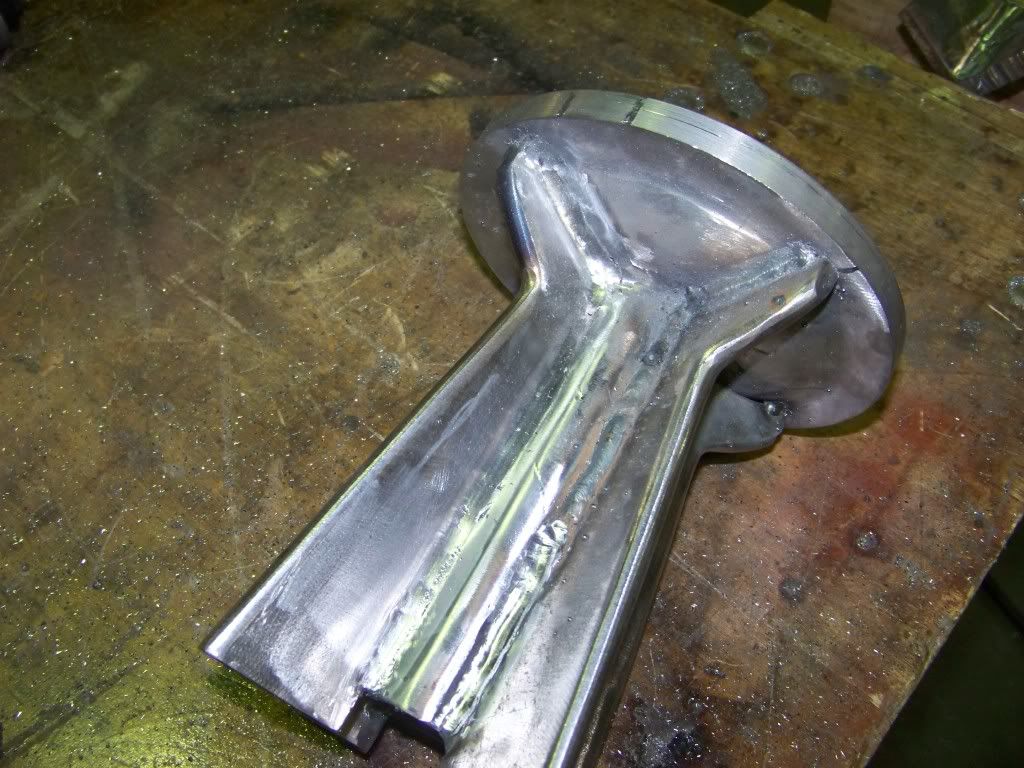
my progress on the pedistal, sorry i didnt get a pic of the pieces before i welded them together, on the end you cant see is a ball that will rest in a socket in the axle to allow it to pivot and tilt side-to-side, i cheated a little bit and used a 2" trailer towing ball. there isnt anything in the pic for scale but the overall length is about 8" and the disk at the bottom is 6 1/2" dia
im having a problem with it and that is that i would like to have a nice 1/4" or so radius where the gussets meet the center pipe, they are welded together obviously and i cant get the die grinder to give a smooth enough finish to satisfy me and the flap disk on the angle grinder cant reach most of it so i was wondering if any of you had any trick ways to accomplish this, i have a cylindrical flap drum for the die grinder but its 1"dia (the smallest i can find) is too big so that doesnt work. any ideas would be great.
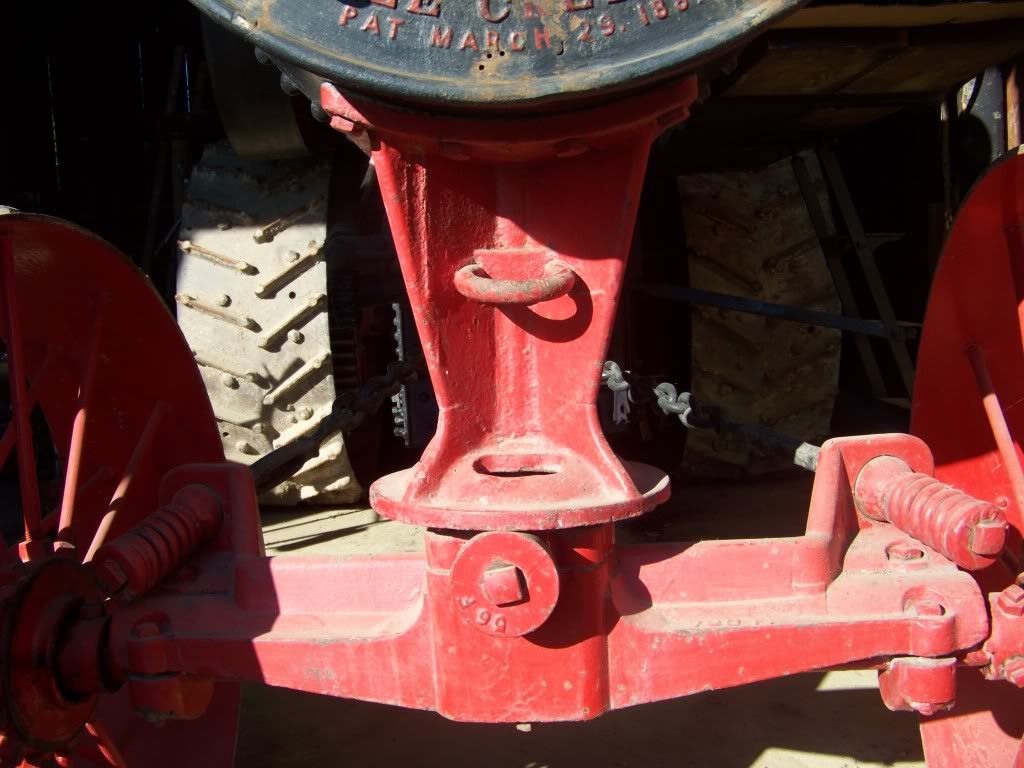
the pedistall and front axle on the original