- Joined
- Jun 4, 2008
- Messages
- 3,285
- Reaction score
- 630
Today I painted the frame and tank of the tender (separately). Here's the tank:
I found that the beading around the upper edges are indeed brass, so I'm not sure how well the paint will adhere. It will get a second coat tomorrow.
Yesterday I took the boiler over to a fellow club member's house where he Tig'ed the ring for the firebox door onto the boiler. He also tig'ed the brake lever parts where I'd had difficulty attaching them with silver solder:
Finally, I bought a spray basket strainer at Tractor Supply. It has an 80-mesh strainer as shown here:
Since I'm going to be using injectors, the tender water supply needs to be strained to prevent small particles in the water from clogging the injector. My tender is not well suited for putting a well in the bottom, so I was planning to use this strainer inside the tank to connect to the valves via tubing. However, the size and design of the plastic enclosure makes this a no-go. So I plan to make caps for the ends of the strainer basket and connect both valves via barbs and tubing.
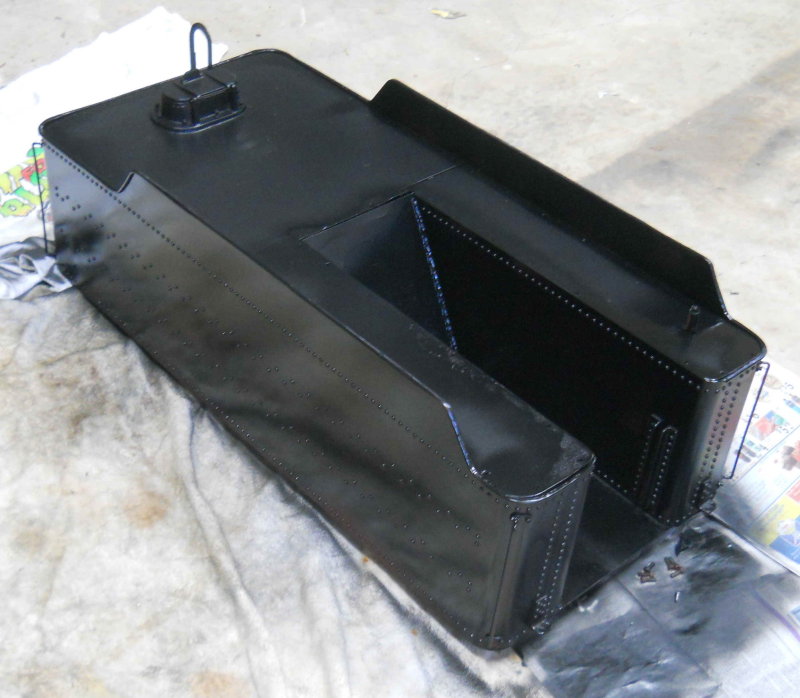
I found that the beading around the upper edges are indeed brass, so I'm not sure how well the paint will adhere. It will get a second coat tomorrow.
Yesterday I took the boiler over to a fellow club member's house where he Tig'ed the ring for the firebox door onto the boiler. He also tig'ed the brake lever parts where I'd had difficulty attaching them with silver solder:
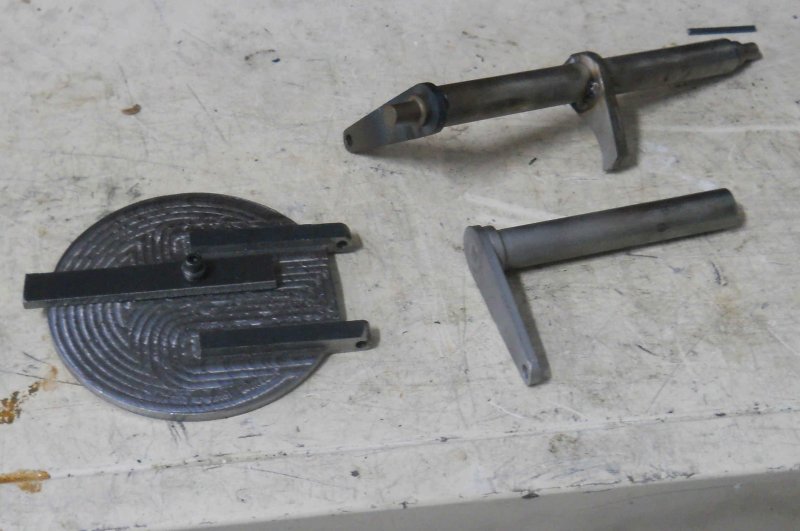
Finally, I bought a spray basket strainer at Tractor Supply. It has an 80-mesh strainer as shown here:
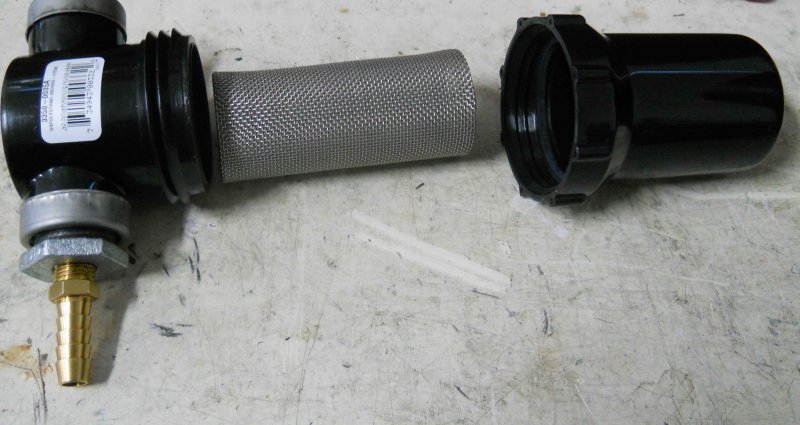
Since I'm going to be using injectors, the tender water supply needs to be strained to prevent small particles in the water from clogging the injector. My tender is not well suited for putting a well in the bottom, so I was planning to use this strainer inside the tank to connect to the valves via tubing. However, the size and design of the plastic enclosure makes this a no-go. So I plan to make caps for the ends of the strainer basket and connect both valves via barbs and tubing.