Hello everyone thanks for looking at my project. This is the first time that I have posted an in-process build. As I am a new member here, the engine was started quite a while ago and is fairly well along. I plan to make a few posts to bring things up to date.
I am building a tweaked version of Jan Gunnarssons V-4 oscillating steam engine. I saw the plans in a book borrowed from the local library quite a few years ago. At the time I was interested in sterling engines, but this V-4 caught my attention. I have since gone back and scanned the plans as a starting point. I wasnt interested in building to the metric plans, so I redrew the engine, adapting the details to nominal inch sizes. An important objective was to retain the curb appeal that originally caught my attention.
So, without further rambling, here we go
This is Jans completed engine:
This is one end plate with steam pipes. The pipes are to be silver soldered in place at a later date. At this time the end plates are still oversize- they will eventually be cut down into the Y shape.
Here are the connecting rods and stainless steel pistons. The con rod bore is 0.25 and the bolts are 2-56. Piston diameter is 0.375.
More to come...
I am building a tweaked version of Jan Gunnarssons V-4 oscillating steam engine. I saw the plans in a book borrowed from the local library quite a few years ago. At the time I was interested in sterling engines, but this V-4 caught my attention. I have since gone back and scanned the plans as a starting point. I wasnt interested in building to the metric plans, so I redrew the engine, adapting the details to nominal inch sizes. An important objective was to retain the curb appeal that originally caught my attention.
So, without further rambling, here we go
This is Jans completed engine:
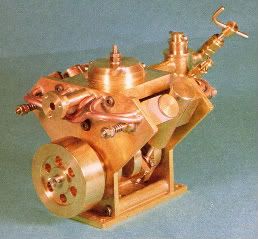
This is one end plate with steam pipes. The pipes are to be silver soldered in place at a later date. At this time the end plates are still oversize- they will eventually be cut down into the Y shape.
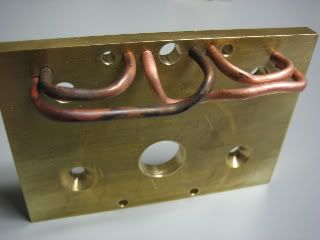
Here are the connecting rods and stainless steel pistons. The con rod bore is 0.25 and the bolts are 2-56. Piston diameter is 0.375.
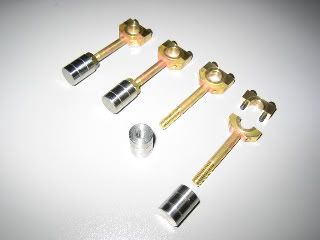
More to come...