Well I figured I would try my hand at building the ez engine plus I like the design of it. I have made an easy wobbler engine, now I am looking for something with a little more of a challenge but not over my head. So I had the day off from work and I decided to look around the place for material and get started on this. I had a slab of 1/4 x 5 x 24 laying around so i took and hack sawed 2 pieces off for the base and the frame. I then spent some time truing them up on the mini mill. I got the base all drilled and the bottom of the frame drilled and tapped. Going to finish the other frame holes tomorrow and maybe start working on a cylinder.
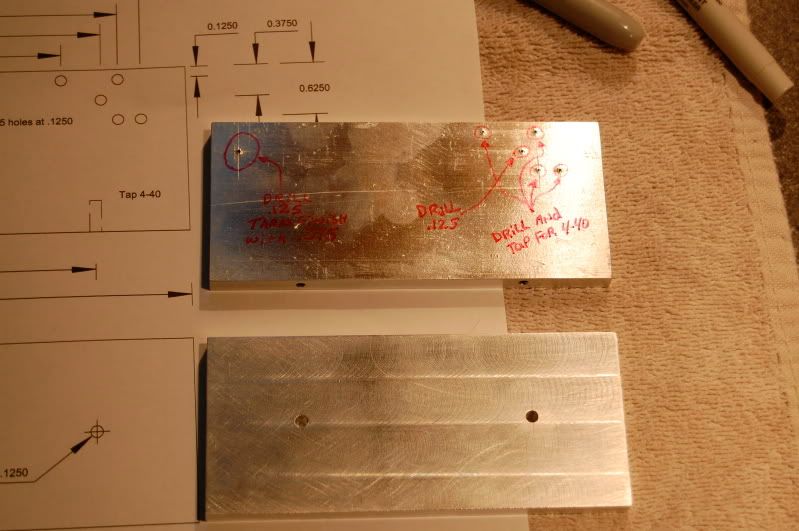
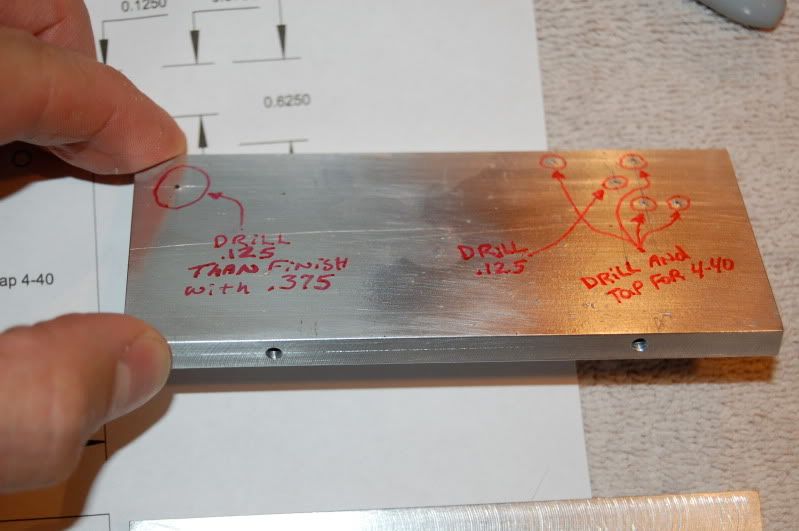