- Joined
- Aug 25, 2007
- Messages
- 3,890
- Reaction score
- 715
I've wanted a sheet metal brake for as long as I can remember, but they always seemed a bit pricey for what they are and my priority list never seemed to include building one. Well, the time has come.
With only a 9" throat, this model won't handle anything very wide, but it will be very stout and should handle pretty thick stuff. The bed is made from a piece of 3" x 10", 3/4" thick hot rolled steel. Here is a picture of the bed mounted in the milling vice so I can mill out the clearance slots for the hinge.
Here I've finished both notches, each .4" wide and .5" deep.
The two side pieces are made from 2" x 2" x 1/4" angle iron. Each piece will be attached to the bed with 3/8" x 16 bolts. The hinge pin will be 3/8" drill rod.
Chuck
With only a 9" throat, this model won't handle anything very wide, but it will be very stout and should handle pretty thick stuff. The bed is made from a piece of 3" x 10", 3/4" thick hot rolled steel. Here is a picture of the bed mounted in the milling vice so I can mill out the clearance slots for the hinge.
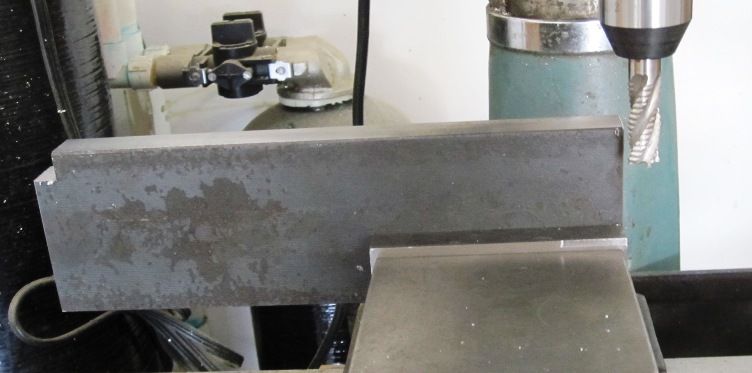
Here I've finished both notches, each .4" wide and .5" deep.
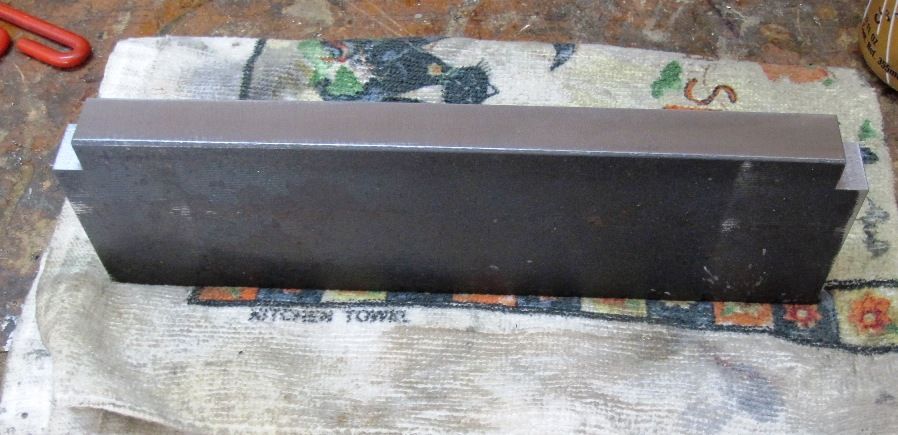
The two side pieces are made from 2" x 2" x 1/4" angle iron. Each piece will be attached to the bed with 3/8" x 16 bolts. The hinge pin will be 3/8" drill rod.
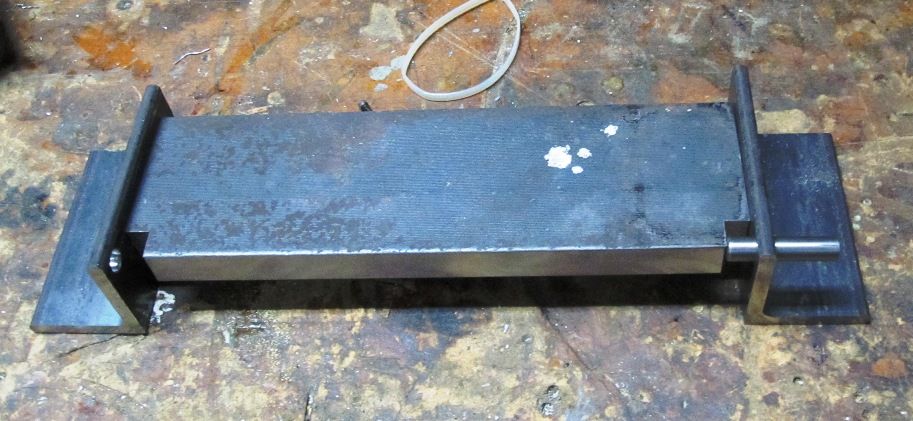
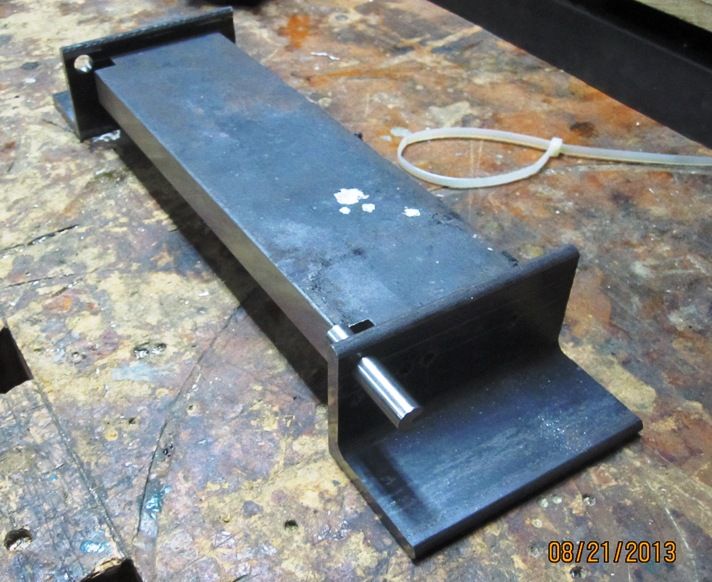
Chuck