Choosing valve springs for these small engines is always kind of a crap shoot. I generally try and get a spring closest in size to whatever I used on the last engine I built. In this instance, the intake valve spring I chose is made from 0.012" diameter wire, has approximately 13 coils per inch when spring is "relaxed" and will just fit over a 3/16" drill. Since there is no cam to operate the intake valve, the spring must be very light to let atmospheric pressure open the valve when required, yet strong enough to close the valve against any friction in the valve guide/cage. Consequently, the valve must move very freely in its guide. Once the valve is closed and the piston starts to come up on compression stroke, the internal pressure will seat the valve even tighter if everything is working properly. The exhaust valve spring is 0.024" wire diameter with 10 coils per inch when the spring is "relaxed" and it too will just fit over a 3/16" drill. The exhaust valve has a mechanical cam to open it, so the spring can be stronger. In fact, it has to be stronger, because not only does it have to close the valve, but indirectly it also moves the rocker arm and the lifter mechanism, and holds the bearing on the end of the lifter mechanism firmly in contact with the cam. The exhaust valve spring as purchased is 2" long. I will probably cut it in half and start out with a spring 1" long, but that may change depending on the operation of the engine. The intake spring is 1 1/2" long, and I will probably cut it in half as well. I purchased my springs at Brafasco in Barrie. Fastenal is another fastener company that has a selection of springs.
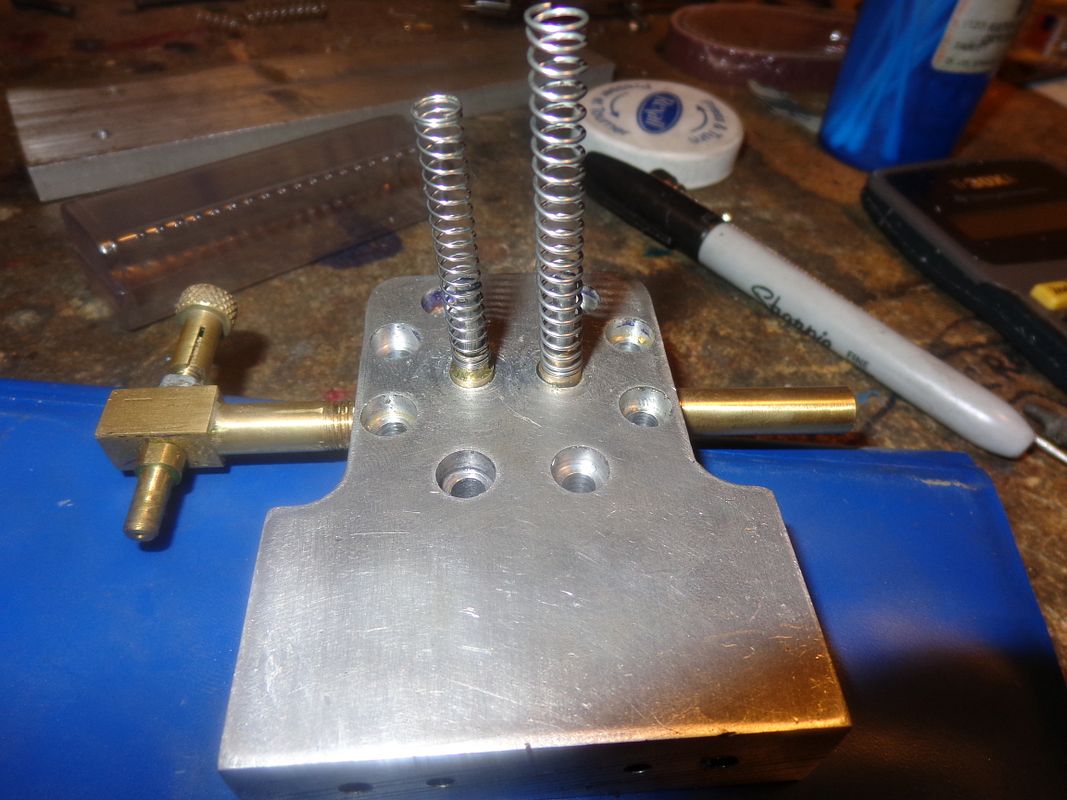